Las peras Diamond Fruit viajan a través de una línea de preclasificación como en casi cualquier otro par del sector frutícola, a saber, con sus carriles de lavado, control de calidad y tamaño; aunque con una gran diferencia. A medida que las peras avanzan a través de los clasificadores ópticos, se transportan en tazas en forma alargada que las voltean para capturar imágenes de ambos lados.
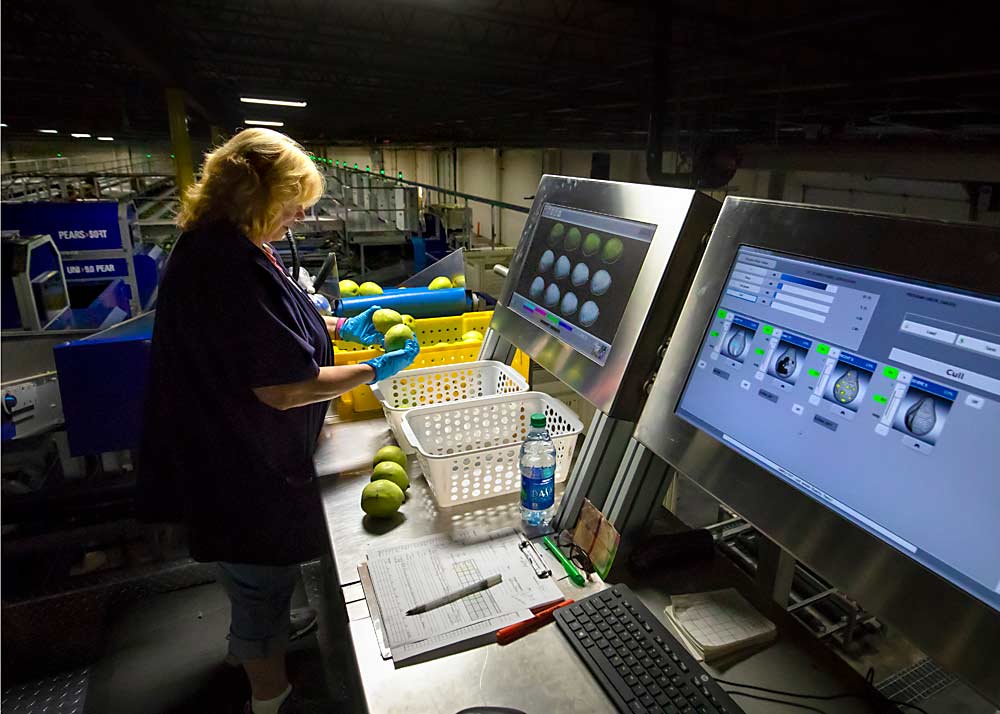
Las pantallas muestran varios tipos de defectos de la pera en la estación de trabajo de control de calidad de Denise Patton en el nuevo sistema de clasificación Diamond Fruit Growers de Unitec en su línea pre-tamaño en Hood River, Oregón, en septiembre. (TJ Mullinax/Good Fruit Grower)
Este paso rápido, puesto en línea en el 2018, puede ser un presagio de avances en un sector marcado por la falta de inhibición de crecimiento de portainjertos, nuevas variedades y vistoso equipo de embalaje que históricamente se ha reservado para la forma redonda de las manzanas y las cerezas.
“Es bueno ver en el sector de la pera que esta atención, este siguiente paso es lo que sigue en el sector de la pera,” dijo David García, gerente general de la cooperativa frutícola Hood River, con sede en Oregón.
En el horizonte del sector se perfilan avances similares, dicen funcionarios.
“Las líneas de pera han experimentado ciertos avances,” dijo Kevin Moffitt, Presidente y CEO de Pear Bureau Northwest. “Yo esperaría ver más en los próximos años”.
Por ejemplo, Mt. Adams Fruit Co. incorporará alguna tecnología de vanguardia en su nueva línea de embalaje, en construcción en Bingen, Washington, al otro lado del río Columbia desde Fruit Diamond, después de 2017 un incendio destruyó la instalación anterior.
Algunos de los cambios incluyen una estación de clasificación óptica de defectos para peras de segunda generación, que implica una mejora a la versión de 2016 destruida por el fuego, dijo el CEO Don Gibson.
Aquel sistema Greefa integrado, el cual hace rodar las peras para exponer todas las áreas para las cámaras, por sí mismo fue el primero de su tipo para peras en América del norte.
Otros incluyen enfriamiento rápido de aire forzado para peras embaladas y cuartos de preacondicionamiento, un almacenamiento de siete pallets de altura automático y sistema de recuperación, colocación de pallets robotizada y manipulación de cartón, lavado de contenedores y una sala de secado independiente.
La instalación fue programada para estar lista para el embalaje inicial la primera semana de enero con operaciones completas previstas para el 1 de marzo, dijo Gibson.
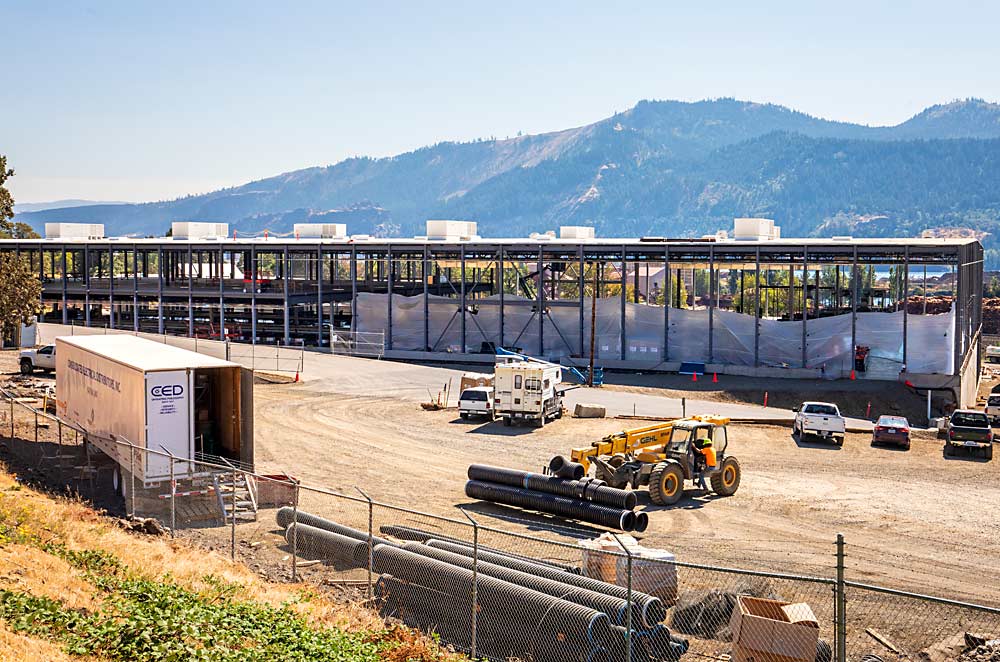
Trabajadores de la construcción fabrican una nueva instalación de embalaje para fruta en Mt. Adams Fruit Company en septiembre en Bingen, Washington, para reemplazar la estructura destruida por un incendio en 2017. (TJ Mullinax/Good Fruit Grower)
Durante años, los embaladores han sido incapaces de disfrutar de la velocidad y la precisión de los clasificadores ópticos en peras porque su forma les impedía girar como cerezas y manzanas. Es un tema importante de discusión en el Congreso Interpera 2017 y prioritario en la lista de la competencia entre fabricantes de líneas de embalaje alrededor del mundo.
“Uno siempre tiene que adaptarse un poco”, dijo Gibson. “Las peras se manejan solo un poco diferente.”
Diamond Fruit pensó que era momento de invertir y así mantenerse competitiva en el futuro.
“Queremos estar aquí otros 100 años”, dijo García. En 2013, Diamond celebra su 100 aniversario como una cooperativa.
Inversión Mayúscula
La cooperativa, que comercializa a través de los productores de Rancho Starr, con sede en Wenatchee, Washington, invirtió $7.5 millones USD en la línea preclasificación Unitec, que también cuenta con nuevos volquetes de depósito automático, mecanismos robotizados en cada extremo de la línea pre-tamaño y recuperación automática de muestras.
Gastar esa cantidad de dinero fue una decisión difícil para la cooperativa, una de las embaladoras de pera de invierno más grande del mundo, pero los productores-propietarios sabían que lo necesitaban para modernizar su planta de embalaje, que todavía utilizaba equipo convertido para papa que contaba con hasta 60 años de antigüedad, dijo Scott Halliday, Presidente de la empresa.
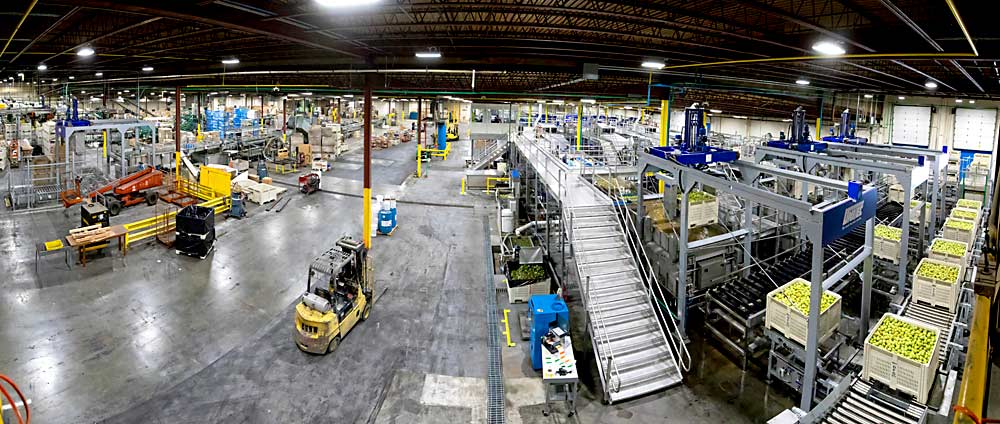
El mismo edificio en Diamond Fruit alberga la nueva línea pre-tamaño y la antigua línea de embalaje para peras. El equipo pre-tamaño, a la derecha, incluye una nueva clasificación y sistema de contenedores de gestión robótico encaminados a mejorar la seguridad alimenticia y reducir la mano de obra. (TJ Mullinax/Good Fruit Grower)
“Nadie en la base de producción se quejó, todos estaban de acuerdo,” dijo Halliday, un productor de cuarta generación y uno de los 85 miembros propietarios, en Hood River Valley.
La empresa compensó el costo por el cierre de otra línea de preclasificación situada en la cercanía de Parkdale, Oregón, dijo Halliday, aunque la empresa todavía cuenta en esa parte con almacenamiento enfrío y atmósfera controlada.
La empresa comenzó a revisar sus opciones aproximadamente hace seis años en un intento por modernizarse y encontró muy poco de valor. Encontraron líneas de manzana que habían sido ajustadas pero poco en algo específico para peras.
Luego se encontraron con Unitec, más reconocido por sus cerezas. El fabricante italiano quería construir un prototipo y lo entregó en marzo de 2017. Diamon Fruit intentó utilizar peras en éste.
Después de esa visita, la cooperativa acordó invertir y pidió a Unitec construir una línea permanente. Optaron por un mecanismo que permite girar la fruta en tazas en forma de pera en lugar de rodarla, para evitar rascar la piel sensible.
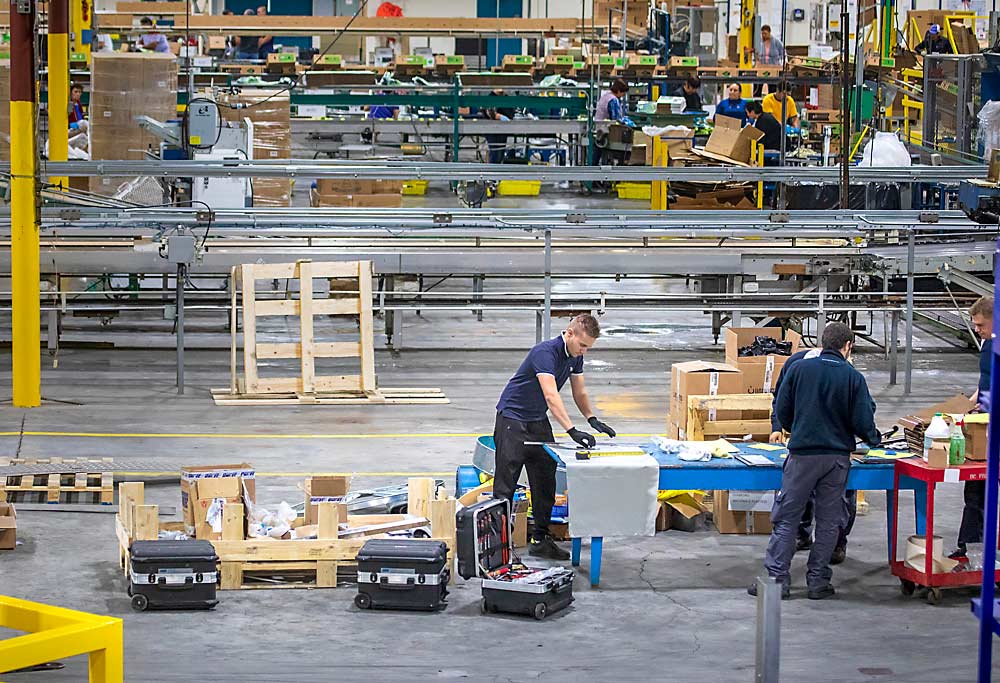
Técnicos de Unitec trabajan en pequeñas piezas específicas, calibrando el nuevo sistema de gestión pretamaño y contenedores para peras de Diamond Fruit. La anterior línea de embalaje manual de Diamond se ve en el fondo. (TJ Mullinax/Good Fruit Grower)
“¿Es perfecta? No,” dijo García. A veces la fruta más pequeña todavía rueda.
Sin embargo, la clasificación ha sido acertada hasta el momento y la empresa funcionaba con Bartletts and Anjous previamente medidas en diciembre, más tarde que de costumbre, con muy poca fruta dañada.
“Nos da mucha confianza la suavidad de la máquina”, dijo García.
También en diciembre, los trabajadores transportaban peras Bosc a través de la línea y están convencidos de que la maquinaria funcionará a largo plazo en la variedad con cuello largo y delgado.
Mientras tanto, el embalador ha mejorado su capacidad con el equipo nuevo. La línea pre tamaño corría alrededor de 75 contenedores por hora antes de las mejoras y ahora un promedio de alrededor de 100 contenedores por hora. Podían llevarlo hasta 120 contenedores, pero el resto de su infraestructura no pudo mantener ese ritmo, dijo García.
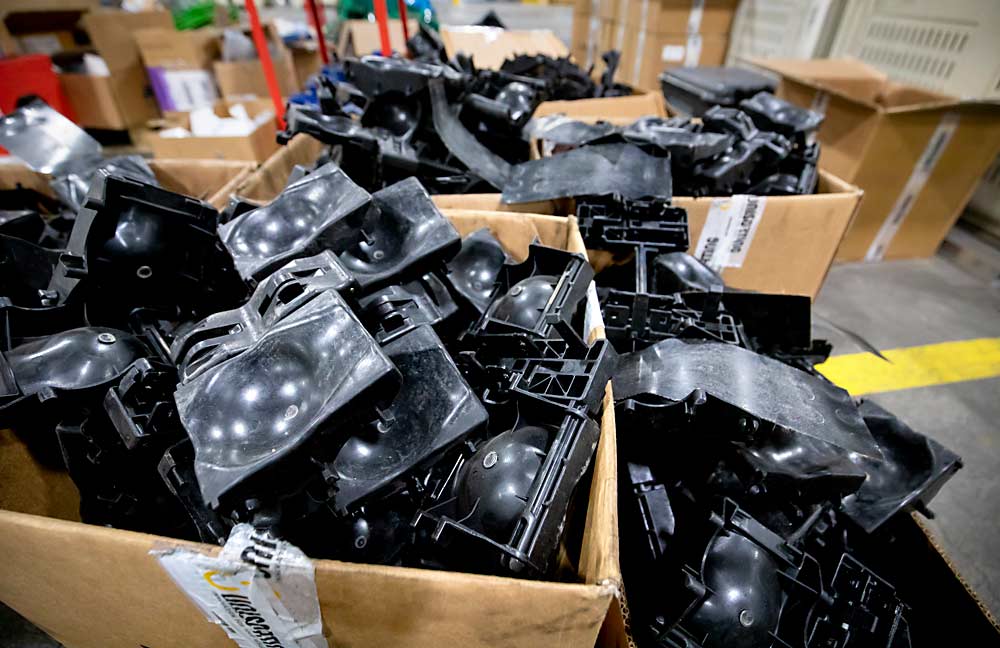
Cajas de nuevas tazas clasificadoras para fruta en espera de su instalación en la línea pre tamaño de Diamond Fruit. Aunque las tazas son en forma de pera, también se podrían utilizar para mover las manzanas a través del proceso de clasificación. (TJ Mullinax/Good Fruit Grower)
La empresa también recortó a su personal clasificador pretamaño de 75 a siete. Esas personas han sido recolocadas en la empacadora del edificio y la empresa de embalaje todavía necesita a más empleados, dijo García.
A juzgar por sus visitantes, Garcia concede que los avances específicos para peras vienen desde otra parte del sector. “Algunas personas han venido a verlo,” dijo.
Una selección de destacados de empacadoras
Las plantas empacadoras se actualizan constantemente con nuevos equipos y tecnología.
Seleccionadores ópticos. Colocadores de pallets robóticos. Empaquetadores inteligentes. La lista continua.
Good Fruit Grower ha creado esta imagen con unas cuantas notas destacadas de todo el sector, como se ve en giras del sector a lo largo de 2018.
Kershaw Fruit y Cold Storage
Kershaw Fruit y Cold Storage en Yakima, Washington, regresaron a una forma simple y antigua de tecnología para enfrentar la nueva amenaza de listeria tras el brote vinculado a manzanas contaminadas en Bidart Bros. en California: burbujeadores.
La empresa simplemente borbotó aire en el agua del tanque de canal para crear turbidez. Como las manzanas flotaron sobre las burbujas, se voltearon y giraron, exponiendo los cálices y los tallos a la solución de saneamiento.
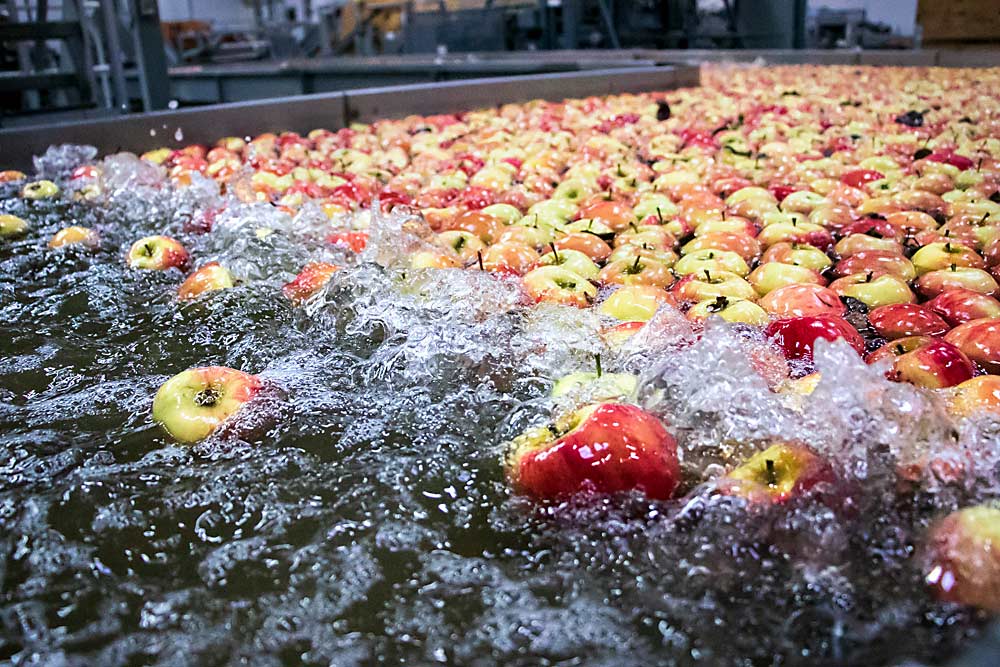
Las manzanas, moviéndose de derecha a izquierda, voltean y caen sobre los rápidos causados por burbujas de airetwist en las instalaciones de Kershaw Fruit and Cold Storage en marzo de 2018. Las burbujas, una herramienta de seguridad alimentaria, fuerzan a la fruta para dar vuelta, exponiendo los cálices y tallos al saneamiento fluido. (Ross Courtney/Good Fruit Grower)
“Se trata de algo que se usó antes durante años y luego simplemente se perdió”, dijo el Gerente de producción y operaciones de Kershaw Fruit, Aaron Arndt, durante un recorrido del sector en marzo de 2018.
Sin los rápidos, las manzanas flotarían tallo arriba o encima de cáliz, lo que dejaría dos puntos propensos a contaminantes en el proceso de saneamiento.
Kershaw instaló su nueva línea en 2012. En 2014-15, un brote de listeriosis que envió 34 personas al hospital fue rastreado hasta la línea empacadora de Bidart Bros.
Por ello, los gerentes de Kershaw comenzaron a buscar formas de agregar turbidez a la línea. Algunos de los veteranos mecánicos y gerentes le dijeron a Arndt que las líneas empacadoras empleaban burbujeadores en la década de 1990 para crear más impulso. Arndt y sus equipos ensayaron durante unos meses y soldaron los detalles de su versión final, un soplador de 1.5 caballos de fuerza con tubos de acero inoxidable, en 2016.
La actualización cuesta menos de $1,500 USD, según cálculos de Arndt.
La empresa se sorprendió con otro beneficio después de la adición. Los burbujeadores de hecho aumentaron la eficacia de su línea al brindar a la fruta cierto impulso para moverla a través de algunos giros pronunciados de 90 grados, que fue de hecho la razón de introducir los burbujeadores en un principio.
Washington Fruit and Produce
Aunque los apiladores de pallets robóticos no son precisamente nuevos, no todos los lugares cuentan con ellos todavía, dijo Hanks Mikey, un operador del sistema en Washington Fruit and Produce Co., situada en Yakima.
La empresa instaló sus brazos robóticos en 2010 y ahora cuenta con 10 celdas, o puntos, con empaquetador robótico, dijo.
“Todo el mundo los quiere, pero no todo el mundo los tiene”, dijo.
Hoy en día, los robots apilan de 70 a 80 por ciento de las cajas en pallets, dejando a los pocos trabajadores en la sala dividida con poca mano de obra manual. La maquinaria embala, en un día ocupado, 20,000 cajas por cada turno de 10 horas.
También alinean cajas perfectamente, de 8 pies de altura, lo cual proporciona a la pila una sólida estructura al tiempo que daña menos las manzanas en comparación con el apilado manual. Esto es cierto independientemente del tamaño de la caja o el estilo, algo que no podría hacer un colocador de pallets convencional, dijo.
Sin embargo, nada es perfecto. Incluso los robots se desvían un poco y tiran algunas cajas de vez en cuando, dijo Hanks. Es raro pero sucede.
Columbia Fruit Packers
Una remodelación en el almacén de Columbia Fruit Packers en East Wenatchee, Washington, incluyó un túnel de secado independiente lo suficientemente alto para que los trabajadores entren y limpien eficientemente.
El gerente de planta Jack Crowe dio un tour de la nueva línea, junto con Josh Heinicke, Subgerente de planta.
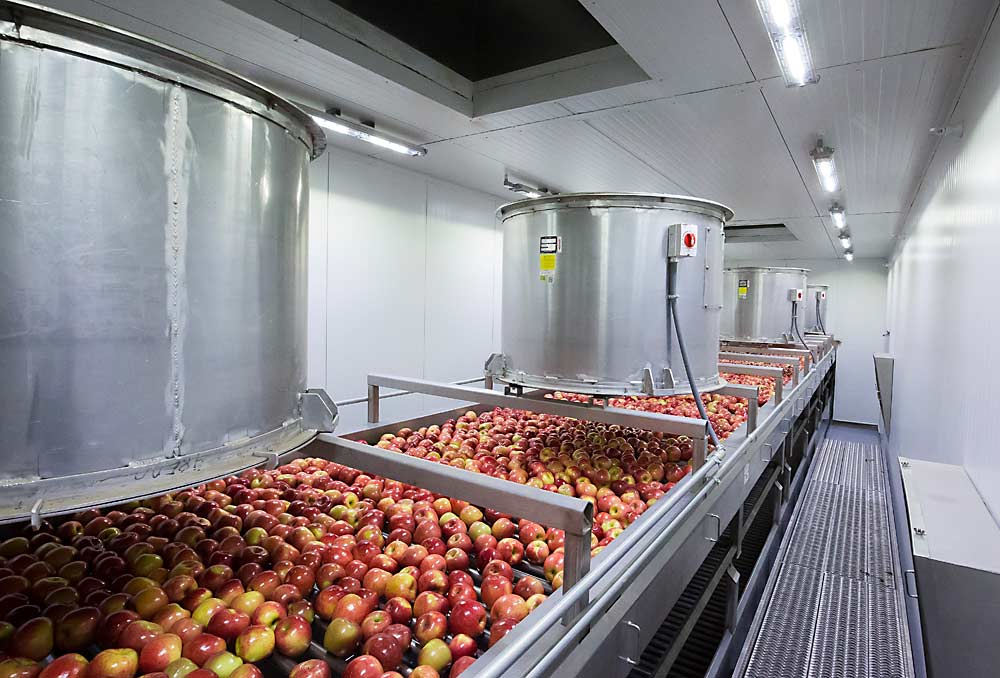
En marzo de 2018 en Wenatchee, Washington, las manzanas Kiku se mueven debajo de enormes ventiladores en la sala de secado hecha a medida de Columbia Fruit Packers. Los ventiladores y el alto calor encerrados dentro del cuarto aislada secan rápidamente la fruta antes de que se clasifique y embalan. Este cuarto fue parte de una remodelación de 2017. (TJ Mullinax/Good Fruit Grower)
El cuarto que se mantiene a una temperatura constante de 120 grados Fahrenheit, con una humedad regulada, cuenta con dos quemadores alimentados con gas natural y un extractor. La fruta se mueve a nivel del pecho sobre rodillos metálicos, aunque como la fruta no rueda, no sufre magulladuras, Heinicke dijo.
Los trabajadores pueden utilizar cepillos para limpiar los rodillos, lo cual se hace rápido, y dado que los componentes, como el cableado eléctrico, se encuentran en las paredes exteriores del túnel, la limpieza del área de secado y otras partes complicadas se vuelve más eficiente, dijo.
“La estructura del túnel va por el exterior, por lo que solo hay paredes pulcras para nosotros”, dijo. “Desde una perspectiva de seguridad alimentaria, es muy bueno”.