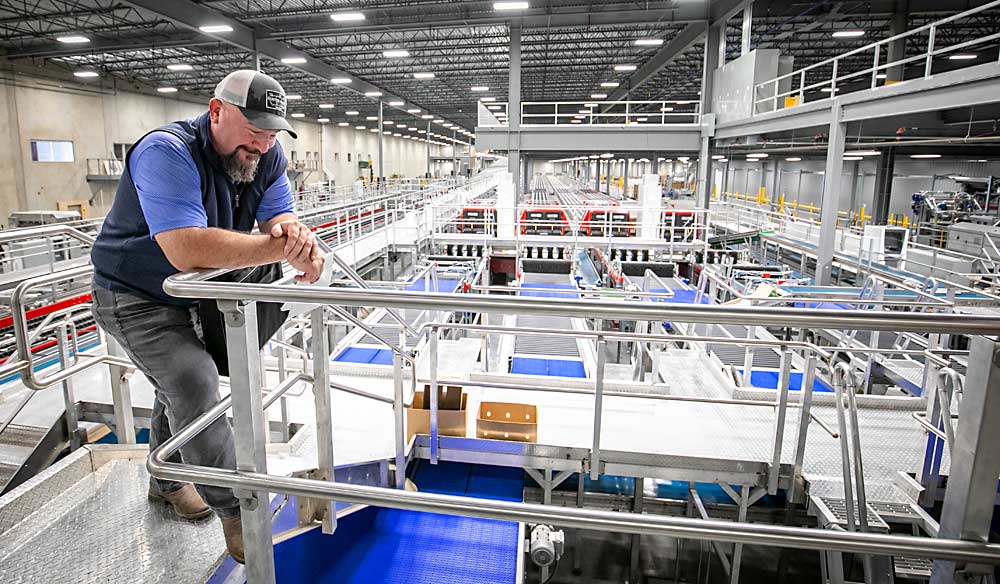
Al caminar por una línea de empaque con un experto en seguridad alimentaria uno puede tener una pequeña sensación de que está abriendo los ojos a un mundo completamente nuevo, en el que los riesgos acechan en rincones difíciles de limpiar, se esconden en las secadoras y flotan en los conductos.
Por otro lado, caminar por la nueva planta empacadora de Borton Fruit en Yakima, Washington, con el director de seguridad alimentaria y cumplimiento Jeremy Leavitt es ver soluciones innovadoras y asombrosamente simples.
Se tiene previsto que la planta de 550,000 pies cuadrados comience a operar este otoño, empacando de 150 y 180 contenedores por hora, dijo Leavitt, y está repleta de eficiencias que reducirán de modo considerable los costos de energía, de productos químicos, de agua y de mano de obra de la empresa.
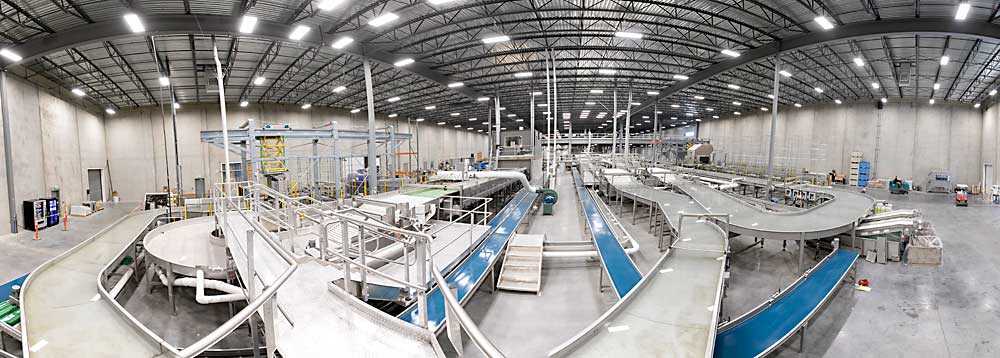
Invertir en la seguridad alimentaria reduce el riesgo de un evento de contaminación, pero también tiene sentido económico, dijo Leavitt. Según cálculos de Borton, el uso de ozono para el saneamiento reducirá el uso de productos químicos en un 25 por ciento, la calefacción radiante ahorrará un 15 por ciento en las facturas de energía y un sistema centralizado de suministro de químicos reducirá el costo del programa de saneamiento en un 35 por ciento.
“He tenido un 100 % de aceptación en todo, desde el diseño de las bandas hasta todos los productos químicos, el sistema de saneamiento de los contenedores”, dijo Leavitt. “En verdad ha sido estupendo poder trabajar para una empresa que aprecia el valor de construirlo bien desde el principio”.
Desde cero
El copropietario John Borton y el ingeniero en jefe Malcolm Hanks fueron quienes tuvieron la visión de las nuevas instalaciones, dijo Eric Borton, director de desarrollo comercial.
“Sin duda han puesto su alma en estas instalaciones”, dijo Eric Borton. “Para nosotros esta planta es una plataforma para que nuestra familia y empresa crezcan y se proyecten. Queríamos construir una planta e instalaciones de clase mundial con la máxima capacidad de limpieza en mente, para cualquier cosa que se nos presente, y establecernos para el éxito y la eficiencia”.
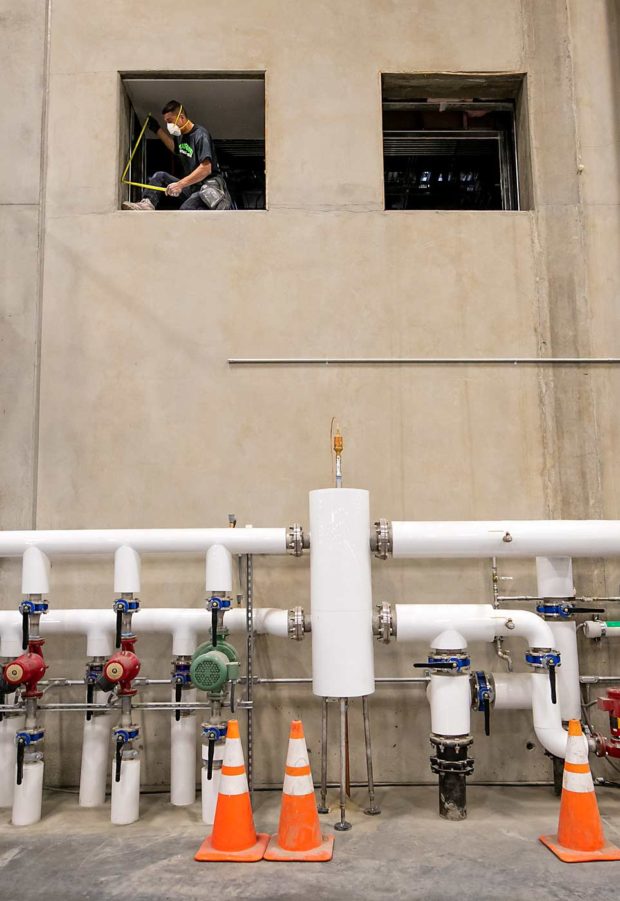
Con la oficina de Hanks justo al lado, Leavitt tuvo oportunidad de trabajar codo a codo con los ingenieros y propietarios para generar una mentalidad de seguridad alimentaria primero en las instalaciones, comenzando con sus cimientos literales.
“Al principio, todo comenzó con la inclinación de los pisos, los diseños de los desagües, que tienen forma de “U”. No se tienen esquinas, por lo que es más fácil limpiar”, dijo Leavitt. A quién si no a los expertos en seguridad alimentaria les entusiasma el diseño de los desagües.
Todo está conectado también debajo de esos pisos: calefacción y refrigeración radiante, por lo que no se esparce el polvo ni sopla viento; agua caliente a la temperatura adecuada; ozono acuoso y productos químicos premezclados para limpieza y desinfección abastecidos directamente a ocho sistemas de mangueras emplazados alrededor de las instalaciones.
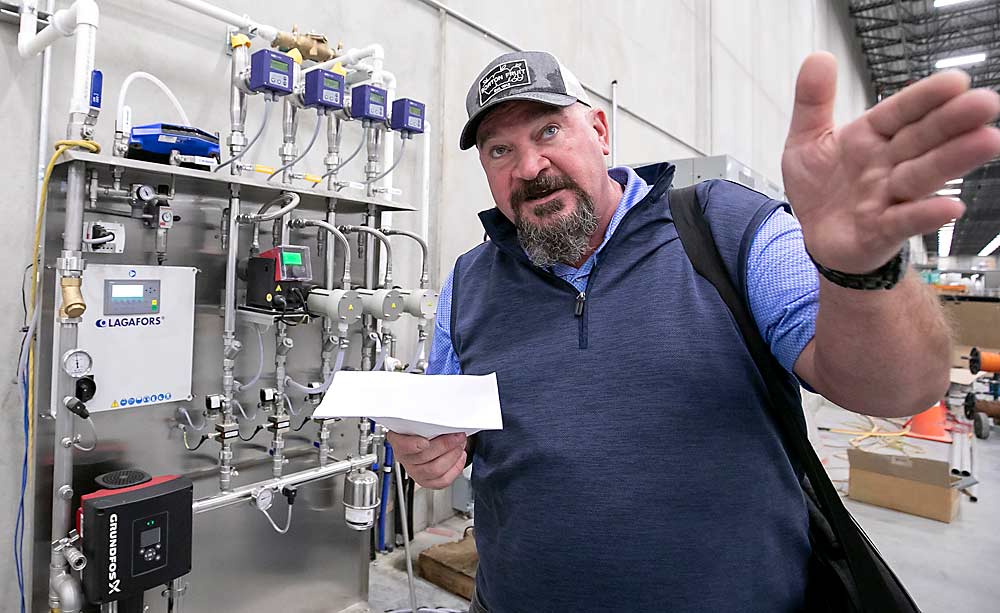
El sistema centralizado de abastecimiento de productos químicos es uno de los primeros en su tipo en el empaque de frutas de árboles, dijo Leavitt.
“Puedo decir que quiero usar 2 ppm de espuma de cloro y enviarla a ocho estaciones diferentes en la planta”, dijo. No mezclar a mano reduce el riesgo de errores, derrames y exposición a los trabajadores, además de que debiera hacer que los equipos de saneamiento sean mucho más eficientes.
Posteriormente, todos los datos de ese abastecimiento automatizado de productos químicos se rastrean y almacenan para su análisis.
“Sé cuánto tiempo se usó en cada estación, qué concentración se usó, y literalmente tengo una hoja de cálculo con la que puedo mostrarle al auditor exactamente lo que hacemos “, dijo Leavitt. “Puedo estar sentado en mi casa monitoreando a mi equipo de saneamiento”.
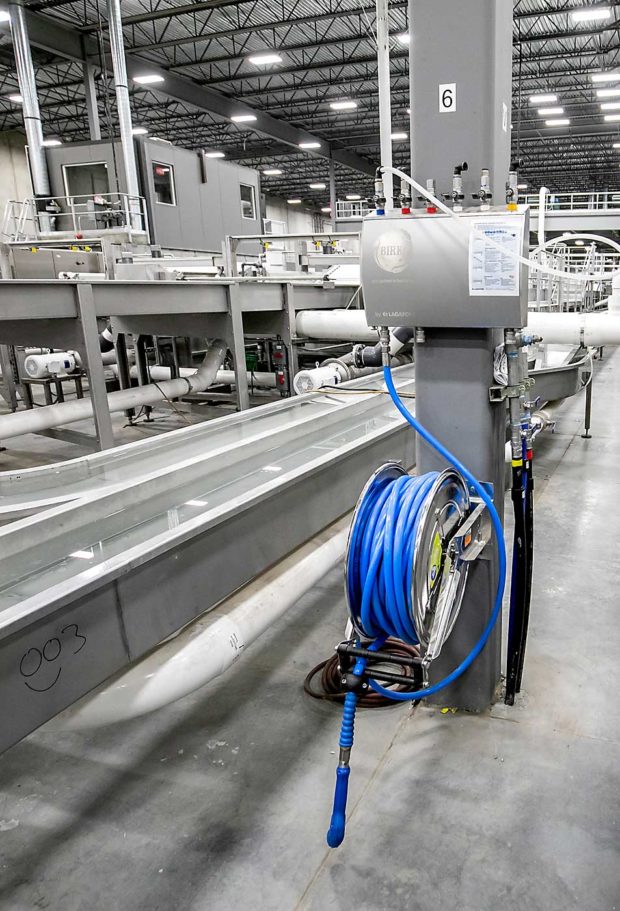
Esto constituye una gran ventaja debido a que comúnmente, los equipos de saneamiento tienen una elevada rotación en los trabajos difíciles que se hacen durante el turno nocturno, dijo Jacqui Gordon, directora de educación de la Asociación de Árboles Frutales del Estado de Washington. Hacer ese trabajo a menudo invisible con responsabilidad es el sueño para todos, dijo.
El sistema Birko de Lagafors puede autofinanciarse entre un año hasta 18 meses, en términos de ahorro de productos químicos y agua, dijo Bob Ogren, vicepresidente de equipos de Birko. La tecnología se desarrolló en Europa, donde los costos más elevados de agua, productos químicos y mano de obra han impulsado la eficiencia.
Actualmente, al enfrentar las mismas presiones, los fabricantes de alimentos de los EE. UU., en especial las plantas procesadoras de alimentos listos para comer y de carne están adoptando la tecnología al diseñar nuevas instalaciones.
“Hace diez o 15 años, el saneamiento era lo último en lo que se pensaba en las plantas. Se llegaba al final y se pensaba: “Oh, necesitamos limpiar este lugar”, dijo Ogren. “Es genial trabajar con una empresa como Borton porque decidieron poner la seguridad alimentaria en primer lugar”.
Diseño y datos
Para la línea en sí, Borton recurrió a Aweta, un proveedor holandés de equipos de clasificación y empaque.
“Nos interesaba una empresa que trabajara con nosotros para desarrollar algunas de estas cuestiones en torno a la seguridad alimentaria”, dijo Leavitt. “Estaban muy emocionados de aterrizar su tecnología en Washington”.
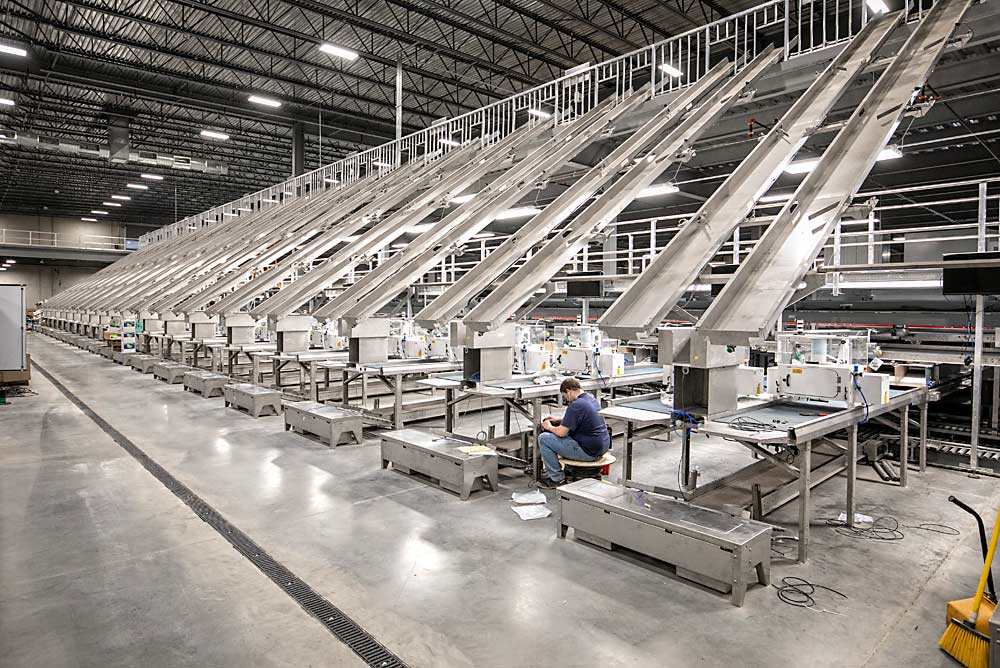
Algo tan diminuto como la etiqueta de una manzana puede tener un gran impacto en la seguridad de los alimentos, ya que las etiquetas adheribles pueden pegarse en las tazas de medir, dejando residuos pegajosos que son difíciles de limpiar. Por tanto, en Borton, todas las etiquetas adheribles se ponen hasta el final, dijo Leavitt.
“La gente podría no relacionar eso con la seguridad alimentaria, pero hará que la limpieza sea mucho más confiable”, dijo Faith Critzer, educadora de extensión de seguridad alimentaria en la Universidad Estatal de Washington, quien mencionó la decisión de la etiqueta adherible al final del proceso como una de las más destacadas características de las nuevas instalaciones.
Incluso la sala de equipos para el saneamiento está cuidadosamente diseñada, con secciones codificadas por colores para designar qué herramientas son para qué partes de las nuevas instalaciones, y tableros de sombra para garantizar que cada herramienta regrese a su lugar después del uso. De esa manera, nadie limpia accidentalmente un transportador con un cepillo utilizado para el drenaje, dijo Leavitt.

Otros elementos de diseño dignos de mención incluyen los túneles de secado que utilizan controles de humedad y calefacción radiante, en lugar del sopleteo con aire para secar la fruta; correas azules con propiedades antimicrobianas y un sistema de autolimpieza; lavadoras de contenedores que cepillan y desinfectan con ozono; y un sistema robótico de volcado de contenedores que arroja las manzanas suavemente al agua, en lugar de dejar que los contenedores floten en el agua.
También ayudó a diseñar un sistema de canal de dos fases para separar el primer lavado del paso de desinfección. La fruta subirá a un transportador y luego descenderá al segundo canal de agua limpia.
“Para mí no tenía sentido no tener una contención separada para estos canales. El agua más sucia está justo aquí cuando entra el contenedor, por lo que este sistema está completamente separado. Puedo desechar eso”, dijo, señalando el primer canal y luego el segundo, “y mantener esto de lo más limpio”.
Ese diseño de canal dividido significa que los desinfectantes aplicados en el segundo canal podrán hacer un mejor trabajo, dijo Critzer, quien señaló que el enfoque se ha utilizado recientemente en varias otras instalaciones nuevas en Washington.
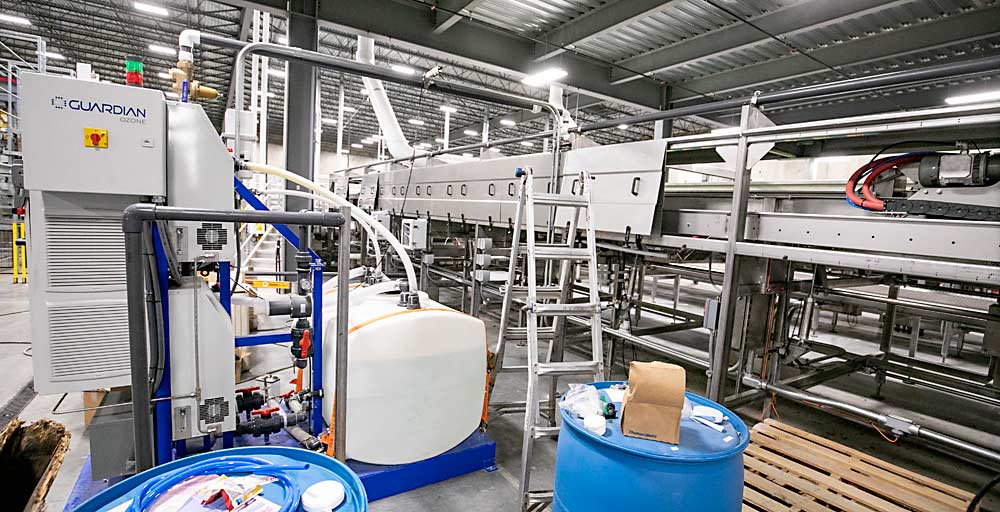
Pero una tecnología completamente exclusiva de Borton es un robot de limpieza con cepillo diseñado y construido por los propios ingenieros de la empresa. Corre a través de un riel sobre el lecho del cepillo, limpiando, desinfectando y luego secando.
“Teníamos claro que nuestro mayor desafío en las instalaciones de empaque de manzanas es limpiar los lechos de cepillos. Ahí es donde potencialmente va a estar la mayoría de los patógenos”, dijo Leavitt. “¿Cuál es la forma más fácil y efectiva de limpiar estas cosas sin cambiarlas? Nuestro propio sistema de lecho de cepillo tipo lavado de autos”.
Para el programa de monitoreo ambiental que garantiza que las prácticas de saneamiento estén funcionando, Borton ha dado el salto a lo digital. El software de Corvium rastrea cada punto de prueba en las instalaciones de la empresa y alerta al gerente de saneamiento de inmediato si se produce un resultado positivo de alguna prueba, para activar la reparación inmediata.
El software ayuda a las empresas a mantener pruebas rigurosas, responder rápidamente y mantener registros para estar preparados para las auditorías, dijo Dave Hatch, director de estrategia de Corvium.
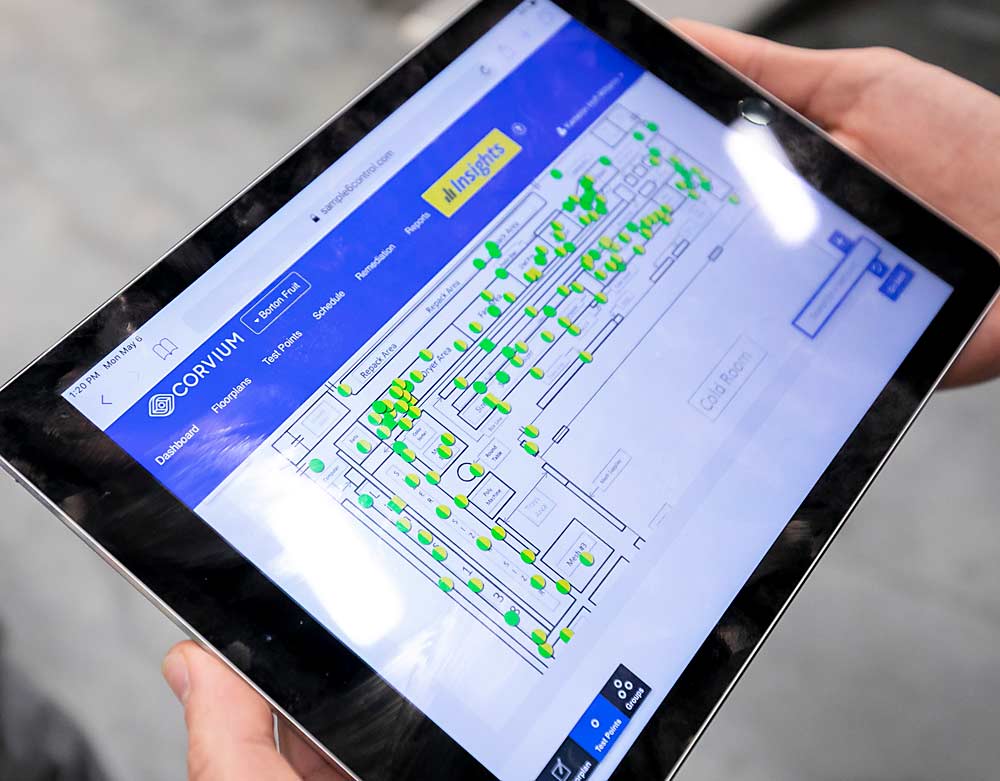
“Los programas de prueba adecuados están diseñados para encontrarlo, no para no encontrarlo. La clave está en emprender rápidamente acciones correctivas y probar y verificar que uno se ha encargado del asunto”, dijo.
Los datos del monitoreo ambiental, junto con los datos del sistema químico centralizado, quieren decir que Leavitt puede rastrear y mejorar los sistemas que mantienen la fruta lo más inocua posible sin necesidad de un paso de “destrucción de microorganismos”.
“Puedo sentarme en mi casa y tener una visibilidad completa de todo lo que sucede aquí”, dijo.
“Tendré datos para saber que estoy limpiando de manera eficiente y que tengo suficientes pruebas de patógenos para demostrar que estamos vendiendo fruta de la mejor calidad posible”.