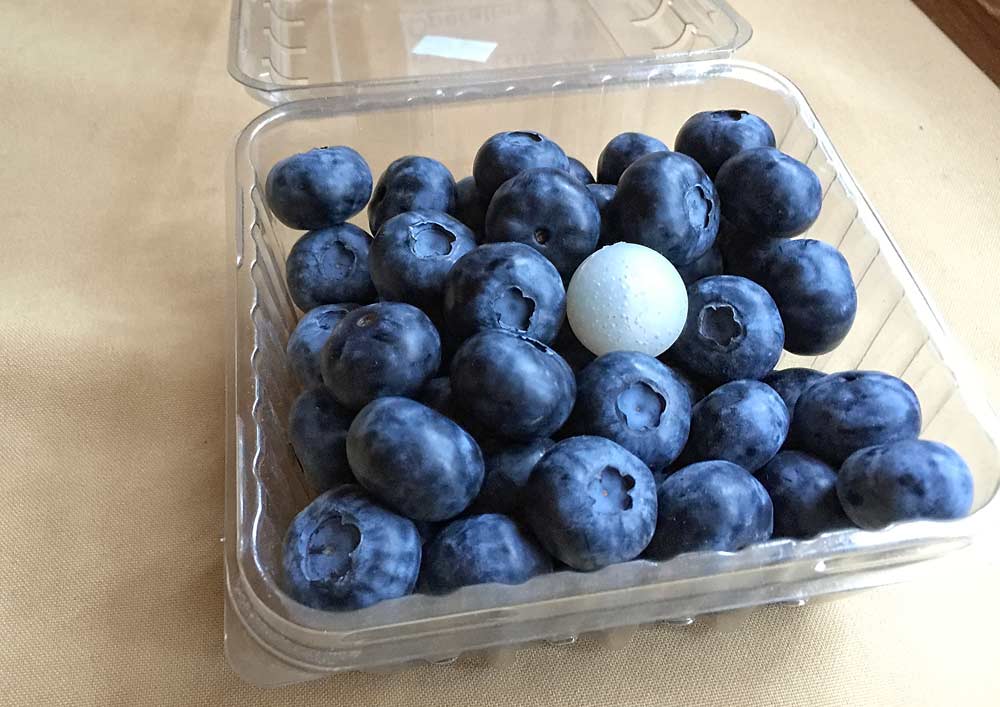
A Berry Impact Recording Device rests in a tray of blueberries. This second iteration of the tool, called BIRD II, was developed by University of Georgia researchers to measure the amount of force on blueberries during mechanical harvest and packing. (Courtesy Charlie Li, University of Georgia)
Everybody knows blueberries bruise when dropped. But a team of researchers at the University of Georgia has developed a tiny sensor that measures how much.
“It has a pretty good linear relationship between height and impact it records,” said Fumi Takeda, a U.S. Department of Agriculture research horticulturist in Kearneysville, West Virginia.
The idea behind the project is to identify the points of impact during blueberry harvesting and packing that cause the most fruit damage, then look for new ways to soften those blows.
The researchers call the sensor the Berry Impact Recording Device, or BIRD. It’s a 6-gram sphere of rubber, resembling a bouncy ball sold in a pizza parlor vending machine, that fits through a No. 12 cherry sizing hole. Inside the rubber are three accelerometers with a battery, microprocessor and memory chip that records at 2,000 times per second how much force it “feels” when it strikes another surface.
It was invented by Charlie Li, the principal investigator at Georgia’s Bio-Sensing and Instrumentation Lab, and Rui Xu, a graduate student. They are on their second iteration of the BIRD, which they call BIRD II. The U.S. Patent Office has recently approved their patent application and Li’s team intends to commercialize it. Takeda has worked with Li to evaluate packing lines and blueberry harvesters with it.
The device is just one of five parts of a research project funded with a $2.3 million Small Crop Research Initiative grant.
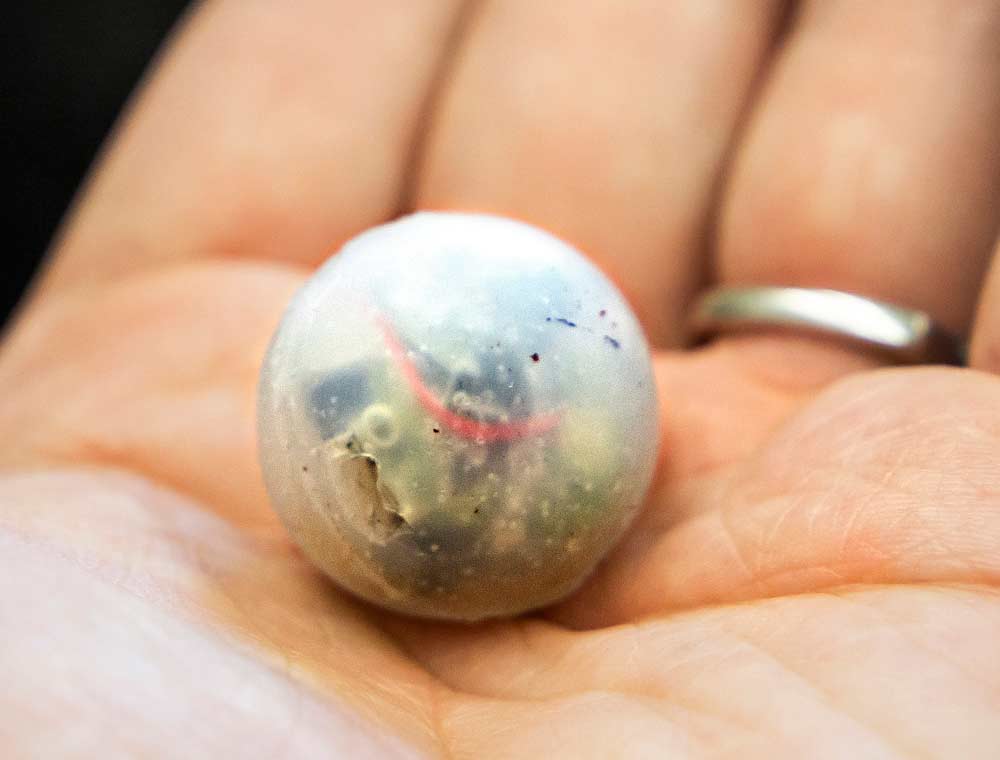
Weighing 6 grams, the BIRD device consists of rubber-encased sensors that measure impact. (Kate Prengaman/Good Fruit Grower)
The BIRD is a smaller spin-off of a sensor for potatoes, apples and tomatoes made by Techmark of Lansing, Michigan, Takeda told growers in March at the Washington State University Fruit School in Prosser. It is capable of measuring small impacts that can damage blueberries.
The researchers have tethered the ball to bushes during harvester trials of three types of mechanical harvesters and run it over two dozen packing lines in the United States and Chile. The team has leased the BIRD to some companies and loaned two of the devices to the U.S. Highbush Blueberry Council, which has made them available to its members.
Not surprisingly, the highest points of fall cause the most force and therefore the most bruising.
The biggest culprits on a packing line are the drop through the electronic sorter and going from a conveyor belt to a stainless steel hopper, Takeda said. One idea to reduce bruising: simply reconfigure lines to lower the drops. The other is to pad those points somehow. Simply changing the surface from steel to neoprene cut the force of the impact by half in tests so far, Takeda said.
The BIRD works as both a research tool and a diagnostic service for harvester and packing line operators and manufacturers, said Lisa DeVetter, an assistant professor of berry crops for Washington State University at the Northwestern Washington Research and Extension Center in Mount Vernon and one of the research collaborators on the project. The biggest impact point during harvest is the fall from the bush to the catch plates on the machine, she said.
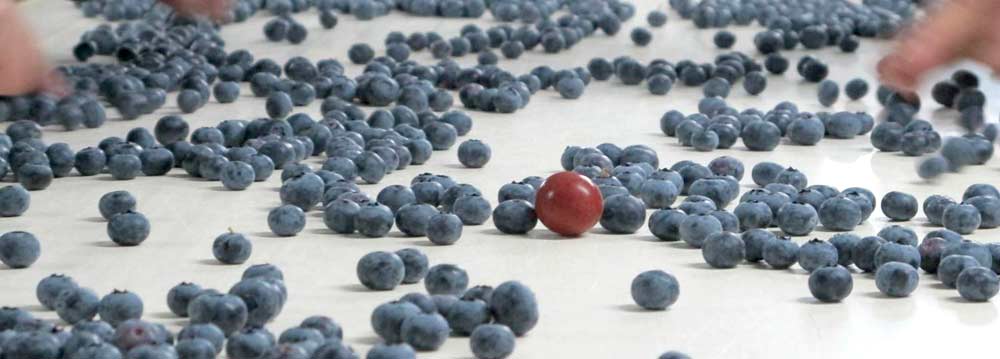
A larger, earlier iteration of the BIRD sensor moves along a packing line. (Courtesy Charlie Li, University of Georgia)
Takeda and the team have been working with Oxbo International, a Lynden, Washington, equipment manufacturer on gentler designs for mechanical blueberry harvesters, such as padded catch plates.
Meanwhile, the researchers are still working on calibrating the BIRD to different blueberry varieties and morphing it to work with other small produce, such as cherries or table grapes.
“We are also working on developing wireless charging, communication and waterproof BIRD sensors,” Li said.
Also, they plan to research the food safety risks involved with the padding they suggest on harvest and packing equipment, work funded by the Washington Blueberry Commission, Oregon Blueberry Commission and other sources, DeVetter said. •
—by Ross Courtney
Leave A Comment