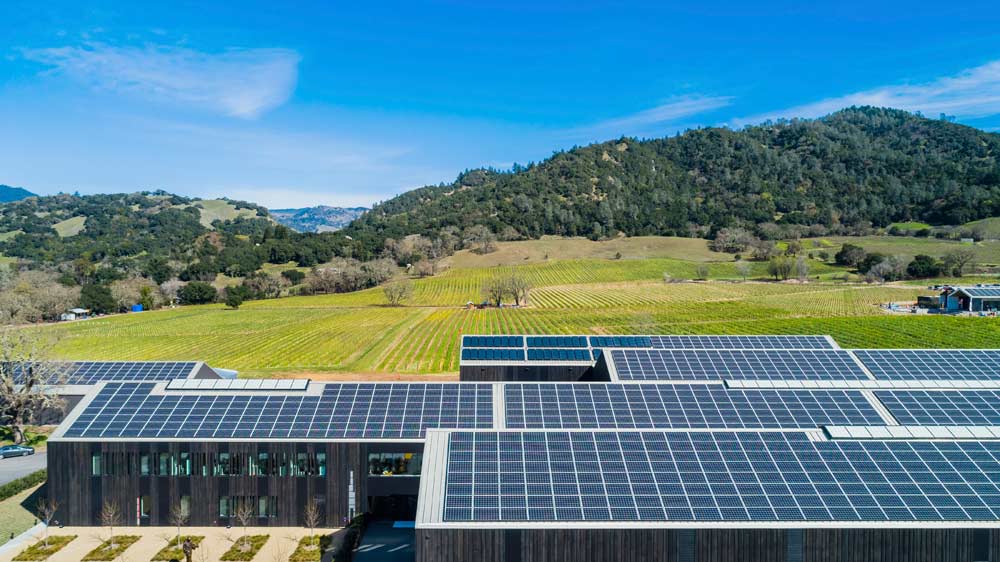
A California winery has become a sustainability superstar by implementing a wide assortment of water- and energy-conservation measures.
Silver Oak Cellars’ Alexander Valley Winery recently became one of only a handful of facilities to receive the U.S. Green Building Council’s demanding Leadership in Energy and Environmental Design (LEED) Platinum certification. What’s more, the winery is now pursuing Living Building Challenge (LBC) certification, an even more rigorous certification that demands, in part, that the facility shows net-positive energy consumption. That means it must produce more than enough renewable energy to meet its own annual energy requirements.
Silver Oak is the first production winery to have earned LEED Platinum certification, announced in August, which was a “really cool first,” said Haley Duncan, project manager for the Alexander Valley winery and tasting room in Sonoma County, California.
Duncan, 26, began pursuing certification at her family’s Silver Oak operation in the summer of 2014, shortly after the winery purchased the 113-acre Alexander Valley property and about a year after she earned her bachelor’s degree in environmental studies. The Alexander Valley winery includes a new 95,000-square-foot winery and office complex and an 11,000-square-foot tasting room.
Sustainability measures
To meet all of the wide-ranging energy, water use and other requirements of the LEED Platinum certification, Duncan led numerous efforts to obtain so-called “credits” toward certification.
On water use, for instance, the winery obtained credits for a membrane bioreactor system that allows it to recycle process water. “All of the water that’s used in our cellar goes to the membrane bioreactor for cleaning, and then it is sent back to the cellar and winery building for toilet flushing and other uses,” she said.
Other credits focused on using light-colored hardscape materials as a way to reduce dark surfaces, which can draw heat and force the building’s air conditioning to work harder, she said.
To improve indoor air quality, the winery performed a building flush-out — basically forcing outside air through the building right before installing furniture to remove all dust and volatile organic compounds.
Many of the energy credits came from the installation of solar panels, and the winery installed a lot of them — more than 2,500 solar panels on the roof. More are on the way as the winery now moves forward with the LBC certification.
“For LBC, the requirement is that you produce all of your own energy with renewable resources on your property, and it actually requires that you produce 5 percent more energy than your building needs,” she said. With the existing panels, plus another 800 that will go on a steel canopy over their water-source tank, she estimated they’ll be at about 80 percent.
To push it past 100 percent — and she said she believes the winery could go all the way to 115 percent — they may look to adding more panels to the refrigerated warehouse.
All of these sustainability measures have demanded considerable research and meticulous calculations, but one has been especially arduous. A unique requirement of the LBC certification is that applicants must screen all building materials used on-site for something called the “red list.” It is a list of about 800 chemicals deemed to be some of the most pervasive chemicals in building materials and also some of the most toxic.
That meant Duncan had to reach out to the manufacturers of just about every single material — insulation, carpet, everything — to identify the chemicals in a given product, she said. She also had to compile all of the relevant safety data sheets and document all of the correspondence she had with each manufacturer.
“That was a huge process, not just for me but for our contractor and all of our subcontractors,” she said.
The next step toward LBC certification is a 12-month performance period. “For that, we have to not only submit what the design and the design intent was, we’ll actually have to prove we’ve done it,” she said. “For instance, we’ll have to show that we truly do produce that much energy and recycle as much water as our engineers said we would.”
Worth the effort
Despite all of the work and cost that goes into LEED and LBC certifications, Duncan said they’re worth chasing.
“The requirements of the county and the state (here in California) are becoming stricter in terms of water use, energy efficiency and those kinds of things, so I feel like many of the things we did for the LEED certification would have been necessary anyway,” she said. “And customers have also become interested in purchasing sustainably and ethically made products.”
[/fusion_builder_column]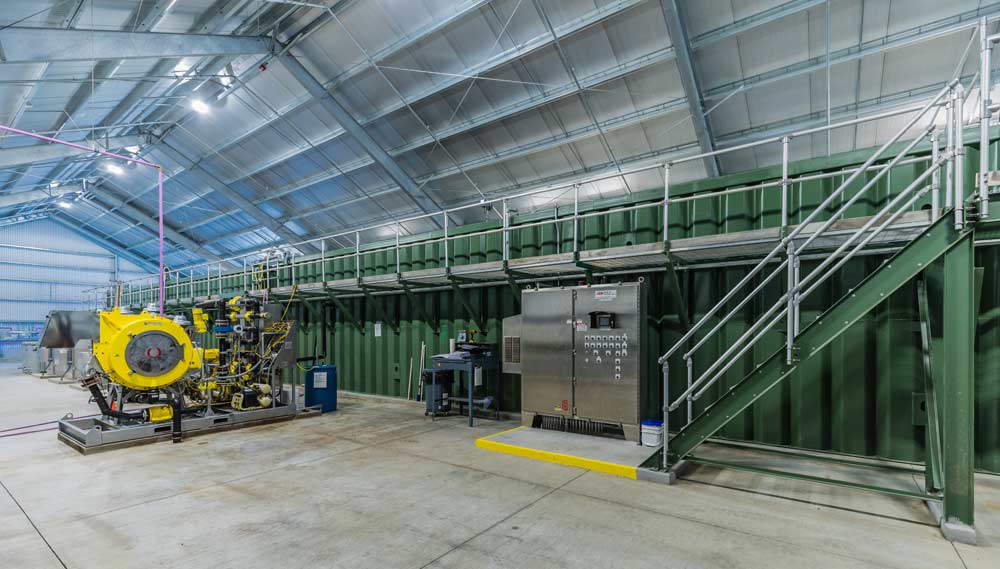
Sustainability measures can help financially, too. For example, Silver Oak’s solar panels will probably have a payback period of five to six years for the winery and just over six years for the warehouse, she said, adding that power company grants and other programs make them even more cost-effective. The membrane bioreactor also provided an indirect benefit, because it was much smaller than the standard wastewater-treatment-pond system they would have otherwise had to install.
“That meant we were able to increase the size of one of our vineyard blocks, and anytime we can add more vineyards, we have more control over the grapes,” she said. “That can only be better for our wine and wine quality.”
For other winemakers who are building new facilities and renovating older ones, she recommended they at least look at the LEED and LBC requirements.
“Even if you don’t go through with the certifications, I see both of these certifications as really wonderful frameworks to think about sustainability for new projects or existing projects,” Duncan said. •
—by Leslie Mertz
Leave A Comment