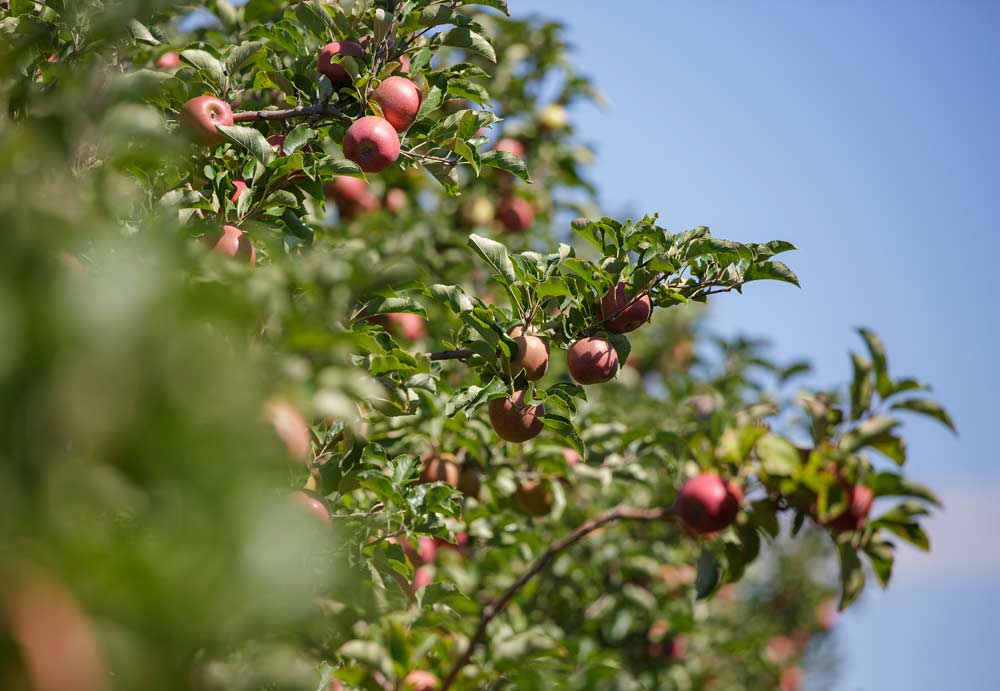
Each of these apples, grown by Mr. Apple fruit company, in the Hawke’s Bay region of New Zealand, are closely monitored and logged into software to help growers achieve optimum packout results. (TJ Mullinax/Good Fruit Grower)
It wasn’t unusual for the growers at Close Orchard to see a 50 to 100 percent difference between their lowest- and highest-yielding apple blocks.
So, the orchard’s owners began the process of benchmarking individual blocks to better track fruit through the growing, packing and storing process right to the customer. The growers divided orchards into bays, with each bay an area of the same variety, rootstock, age and generally similar attributes. A new software program they affectionately call “Billy the iPad” tracks every horticultural operation in the orchard, from sprays to green fruit thinning, with a goal of achieving a specific fruit number per tree, and yield target per bay, based on the fruit size they want.
It’s just one more example of how technology is changing the way growers do business in the orchard to maximize quality — and profits.
Looking at the bay’s previous history in Billy also enables Close Orchard’s managers to evaluate whether they’re “soft-budgeting” or whether there’s greater potential in the bay, according to Richard Hill, chief operating officer for Mr. Apple, which operates 13 orchard management groups, including Close Orchard, from its headquarters in the Hawke’s Bay region on New Zealand’s North Island.
“Interestingly enough, when you look at the information in most bays over a reasonably long period, it struck us very interesting that, often, the best yield it had had in a number of years was the year that had the best size as well as the best quality,” he said during the International Fruit Tree Association study tour in February. “And when you get those three things going together, you’re really starting to perform. Having all that information back at a small-area level of bays means we’ve been able to come with almost a recipe for each bay that maximizes the performance.”
Close Orchard encompasses six orchard areas and 156 bays of apples that include standard varieties and new ones — New Zealand Beauty, New Zealand Queen, New Zealand Prince, New Zealand Rose, Diva, Posy and Smitten among them.
Cropping is different for each of them, and everyone’s idea of an ideal crop varies as well, Hill said, leading to inconsistencies in orchard performance.
“Often, when we looked at the performance of individual bays, the difference was simply that they didn’t have enough fruit on them, that everyone had a different vision what a full crop was and how to go about it,” he said. “And with Billy, we came up with a target crop load and number of fruit per tree that you had to have in that bay.”
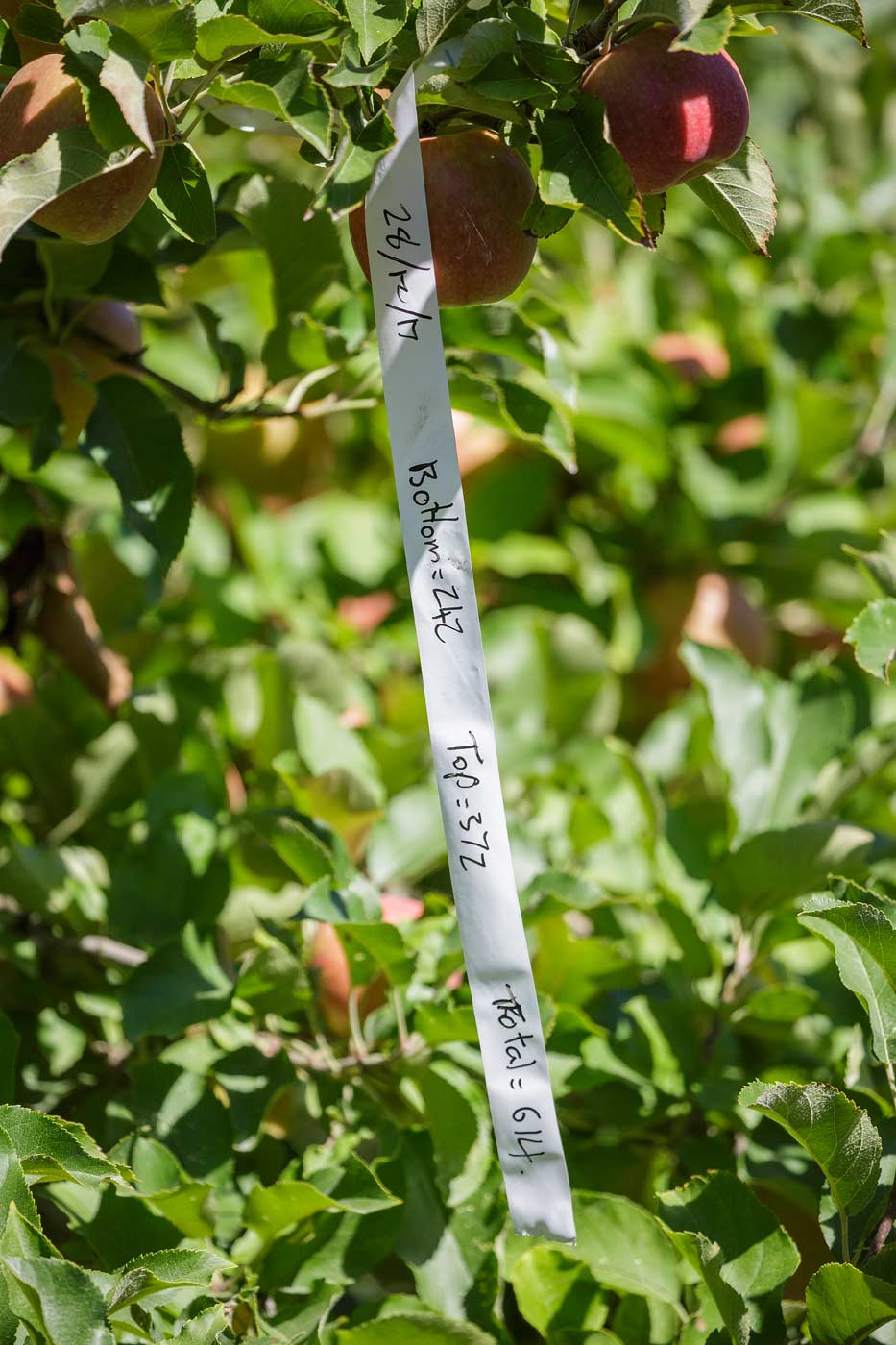
Ribbons placed at the beginning of each tree row at Close Orchard, in the Hawke’s Bay region of New Zealand, show the current season’s crop estimate calculated using custom software called “Billy the iPad.” (TJ Mullinax/Good Fruit Grower)
Billy at work
Mr. Apple’s Robbie McCormick shared insights into the use of Billy in determining horticultural practices in a Lady in Red block, grafted onto Braeburn on Merton-Malling 106 rootstocks in 2009.
Billy tracks yields for the bay beginning in 2012, showing the block varied in production as it came of age. In 2017, fire blight cut yields to just 3,000 cartons per hectare, down from 5,000 the previous two years, but the target for 2018 is 6,000. Bin size and actual export size is also recorded, allowing workers in the packing house to manipulate how they want fruit to be pooled for different markets.
One page tracks chemical thinning, showing by year what was applied to the orchard. “It’s a great tool. If you do have a really good year, you can look up the chemical thinning from that year and see what the recipe was, when it bloomed and what you used — what the secret was behind the success of that great yield,” he said. It also records the amount of money spent thinning per tree each season, — a budgeted number — but McCormick said they’d like to take that data gathering a step further by adding the actual cost each year.
A maturity monitoring page shows Brix, fruit firmness, starch and background color, among other factors, by season, with links to original comments from the lab.
An instruction page enables orchard managers to remind supervisors about generic rules that apply each year and specific directives. For example, this particular bay was experiencing an “on” crop year with medium vigor; the directive was to thin to singles, leaving the largest, and to remove damaged fruit.
A couple of general philosophies about orchard performance have factored into the development of Billy and overall target loads.
One: If you thin to singles, which is one fruit in a bunch, and you’re below the target crop load, get another job. The idea was said in jest by someone, Hill said, but everyone took it seriously. Secondly, if you’re going to make a mistake, leave too many fruit on the tree. One technical manager noted that if they thin to singles, they’ve lost an opportunity. “That’s been a key part of it that’s boosted our yields.”
The latter concept also enables the company to better meet individual market specs much more easily, by managing inventory through several picks. The company separates each pick from each bay through trucking, packing, storage and into the market, where each box carries a label that shows which orchard, bay and pick the fruit came from — and it’s all recorded in Billy.
The decision-making software program, written for the company, has revolutionized standing in a bay of apples, Hill said. But when asked when they’ll be selling the program for use by others, Mr. Apple folks demurred. They’re in the apple business, not the software business. •
—by Shannon Dininny / photos by TJ Mullinax
Leave A Comment