—story by Kate Prengaman
—photos by TJ Mullinax
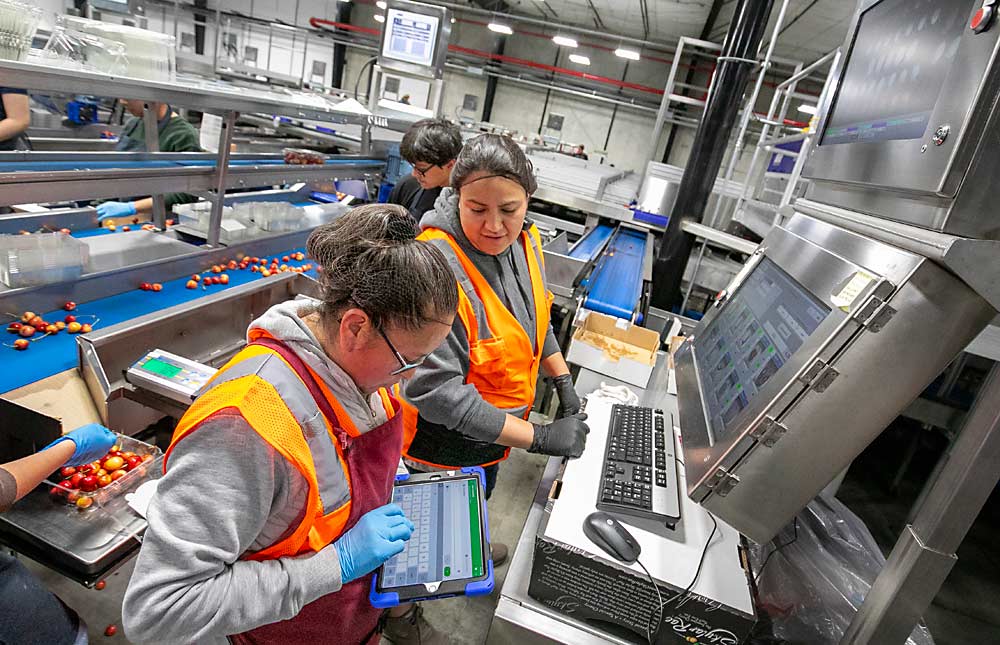
Every time I visit a cherry packing line, I’m shocked again at the tremendous work and technology that goes into getting the right fruit into the right package and on its way to the right customer within a day or two — at the highest price.
The integration of digitized data tools is helping Columbia Fruit Packers to more efficiently manage the chaos that is cherry season. At every step on a cherry’s journey through the facility, from receiving to outgoing packs, employees with brightly colored tablets enter quality data and snap photographs for documentation in an information management platform developed by AgroFresh.
“In cherry season, it’s critical,” said Isaac Balderas, production manager for the Wenatchee, Washington, company. “It’s real-time feedback as our operators take samples.”
Smarter data management tools are being pitched to fruit companies, from orchard to warehouse, and they’re coming from longstanding suppliers such as AgroFresh and new startups like Terrantic. It’s a lofty goal, but fruit companies say they are finding value in the packing-focused platforms.
“Different packing houses are going to be at different stages of digitization,” said Jon Cox, vice president of science and technology for Double Diamond, a packer in Quincy, Washington. He recently worked with Terrantic to bring the company’s quality control and storage data into one place, increasing operational efficiencies. “They met us where we were and are getting us to the next phase.”
The problem is not a data shortage. In fact, packers have so much data on their hands today that they need these new tools to make sense of it all.
“It’s about managing how the right people get the right data,” said Emily Gant of AgroFresh, speaking during an educational workshop the company organized. The company’s FreshCloud tool is simple for users on the packing line and customizable for each operation. “We can work with you to set up the right kind of alerts and make sure they go to who needs to know, so you can make decisions.”
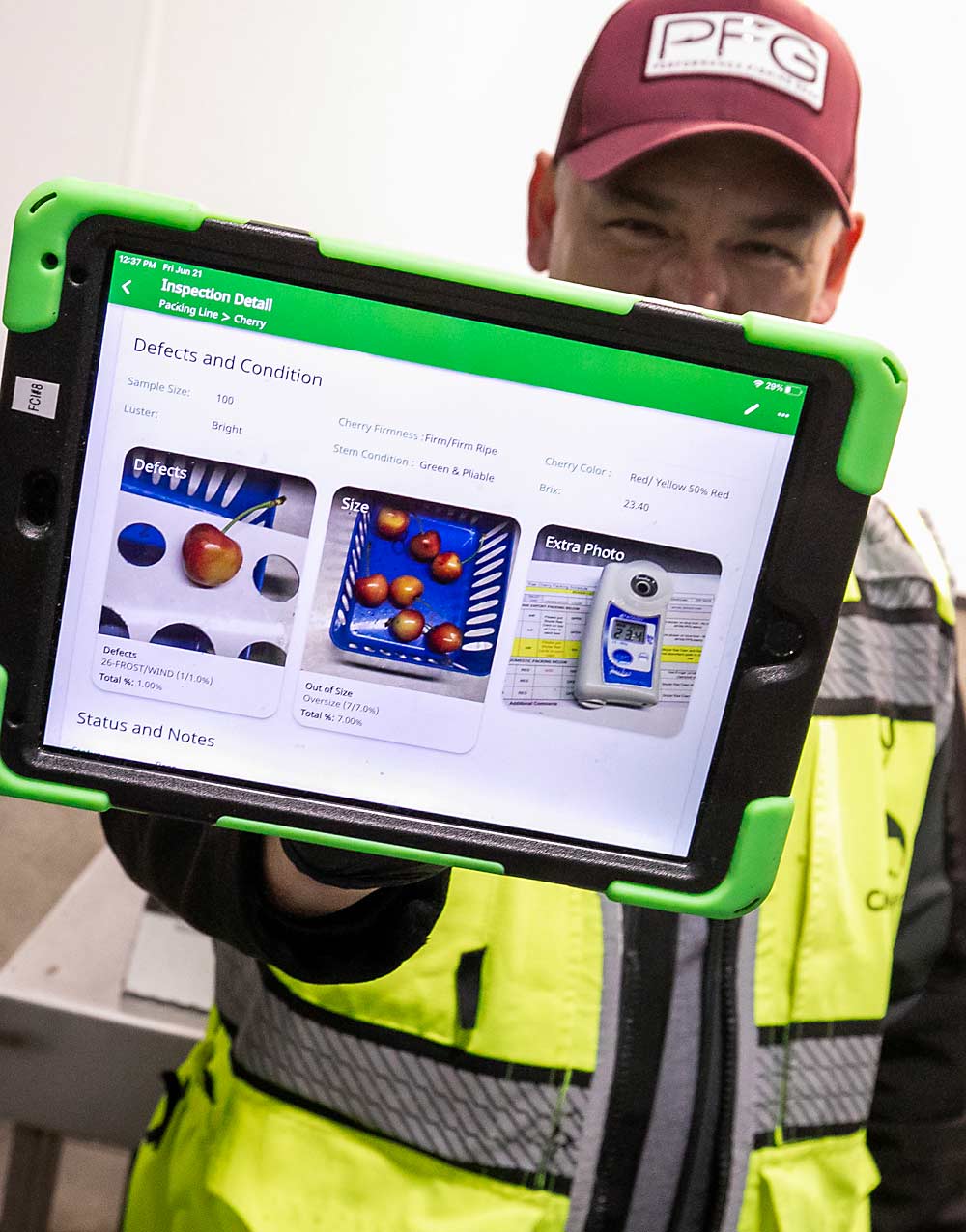
The digital data difference
At this point, FreshCloud isn’t labor-saving technology, but it saves Balderas time he previously spent chasing information kept on paper slips around the facility.
Now, if quality control workers on the line count too many good cherries ending up in the cull bin, for example, or too many cherries getting through despite a difficult-to-detect defect, such as roughed skin from frost damage, the technology flags the data so that the optical sorter can be adjusted for the lot of fruit, before it’s too late. In the control room, big screens display each lot of fruit running that day, color-coded for quick alerts.
“These operators can see receiving, they can see how the ladies are grading, they can see the cull samples, everything is connected,” Balderas said during a June tour. “With paper, by the time we knew we had a problem it was too late to adjust.”
The benefits of digitizing data go beyond cherry season.
“We have an abundance of information, but it didn’t always get out to the people that needed to know,” said Kelli Canterbury, quality control manager at Blue Star Growers, a pear packing cooperative in Cashmere, Washington. “Every shift would turn in paper inspection sheets. It was kind of unorganized chaos.”
For pear and apple packers, FreshCloud connects the storage inventory data with the incoming orders, Gant said. The platform offers some predictive analytics and also integrates with inventory and traceability tools from Croptracker.
“The whole goal is to eliminate food waste. We want to put the right fruit in the box, and the more we can do with customers to preplan, the better chance it makes it in the right box the first time,” she said.
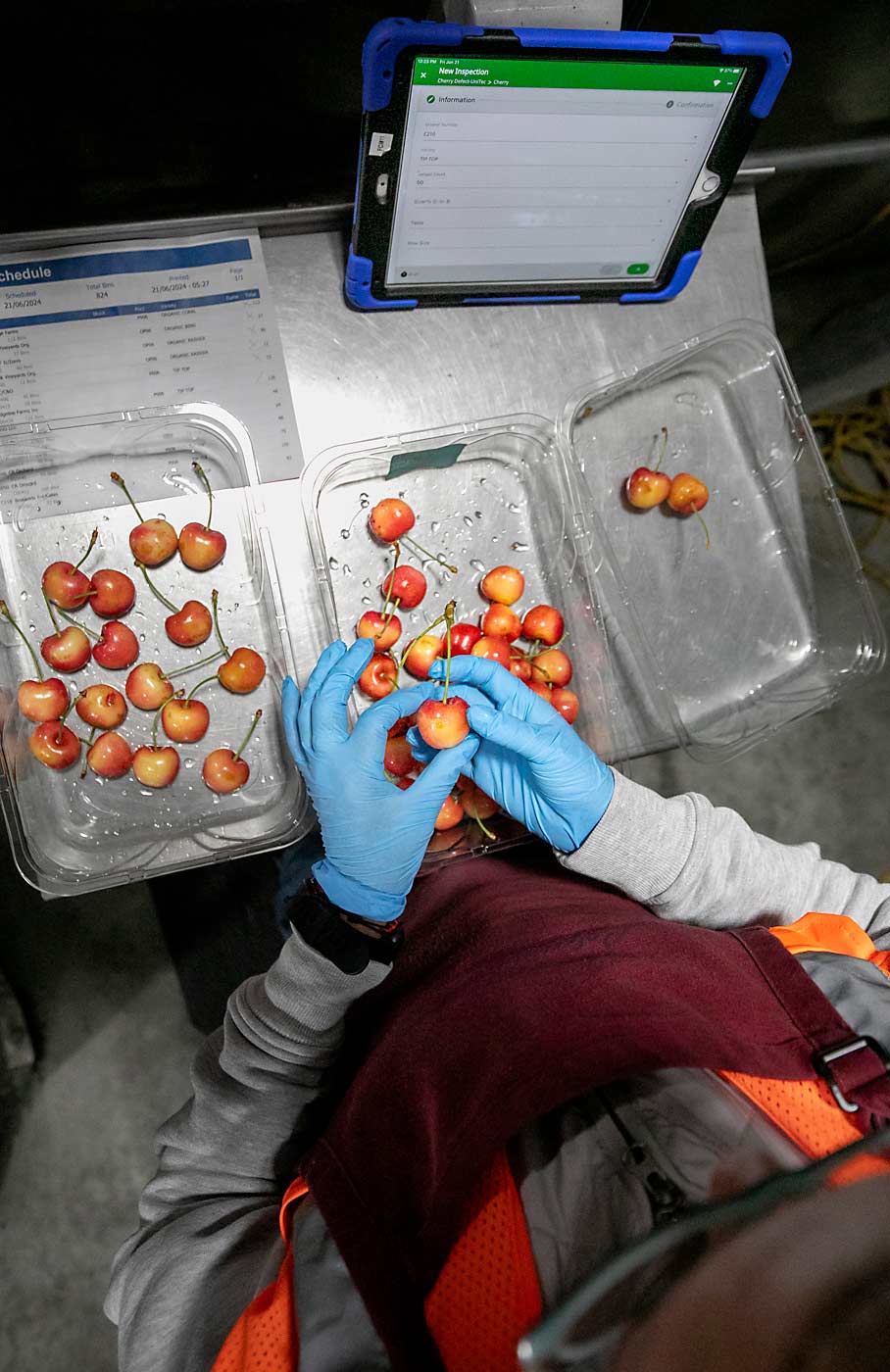
Canterbury said the company hesitated at first to adopt FreshCloud but quickly saw the value of it throughout its operation.
“I can dial into lot, pack date, shipping inspections and see what our last set of eyes saw on it,” she said. With the inclusion of photos, “it’s a lifesaver, everything is documented.”
Back on the cherry line, employees using the tablets echoed her appreciation of the photos. In receiving, Yolanda Ponce uses the app to take pictures as she collects and enters data on size, Brix, firmness and defects, providing documentation that can be used if growers have questions about how their fruit looked.
At the other end of the chain, Francisco Velazquez of CMI Orchards (Columbia Fruit Packers’ sales partner) inspects packed fruit heading out the door — a final check to ensure it meets standards for size and quality. If it does not, the system automatically alerts Balderas that he has a problem.
Velazquez sang the praises of the digital platform for organizing the information and documenting the packing process.
“If a customer has a concern when they receive the fruit, we have pictures of how good the fruit looks,” he said. “It proves we did our part.”
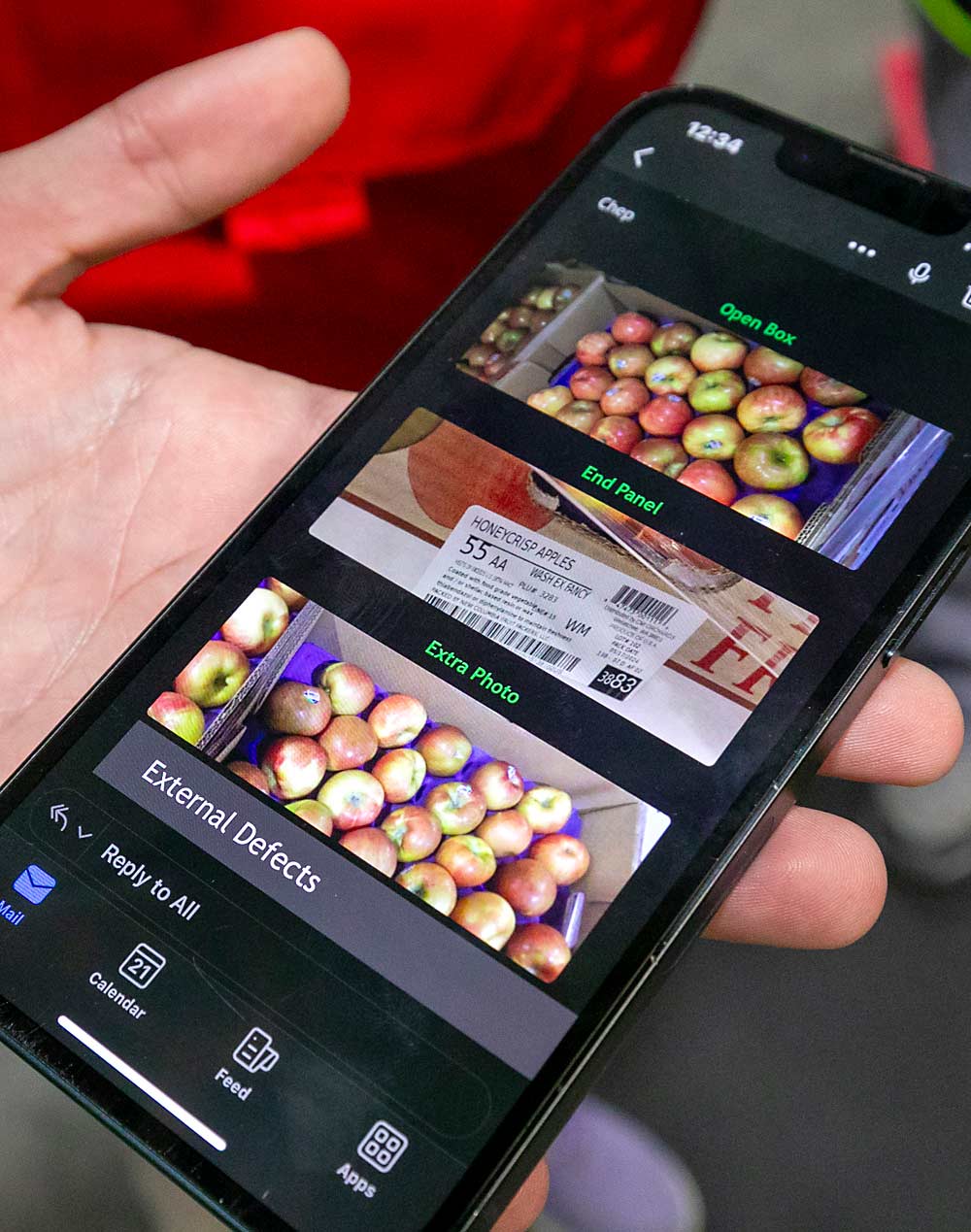
From patterns to plans
Terrantic sees the data digitization as a first step, but founder and president Trevor Cox believes there’s more value to come by using that data to automate decision-making.
“Our core technology is around using AI for data integration,” he said. Traditional operations management systems struggle to keep up with all the data sources now at play in high-tech packing lines, he said, but his company’s approach breaks down “data silos” and “pulls things into a data model so it’s all in the same format.”
The data can then be put to work to improve grower reporting, provide better data integration with sales desks and streamline the spreadsheet management for production planning.
That last step has already helped Double Diamond find efficiencies in its apple packing, said Jon Cox (no relation to Trevor). Previously, the assistant production manager spent a lot of time tracking down that information from different systems when planning meetings, he said. Now that job is easier.
Terrantic envisions making the production manager’s job easier, as well, as its data analysis tools interpret the data and make recommendations.
“It’s a super-cool concept to have our order data, our inventory data, and have it generate a packing plan,” Jon Cox said. “We’re excited about that possibility — but first, I just needed to get these spreadsheets to talk together.”
The central challenge packers face is input variability, which limits efficiency, Trevor Cox said. Better data management can get ahead of that. He cites the success of his previous company that developed inventory management tools for the mining industry. After selling that, he co-founded Terrantic to bring the lessons learned to agriculture.
Steve Caudill, the chief technology officer at Columbia Fruit Packers, said he’s impressed by how Terrantic’s approach to data solutions reduces complex problems of inventory variability to simple algorithms.
“Size, grade, QC, it’s just math. The problem is we have been doing this all in our heads, and it’s way too complicated,” he said. “When you have all the data, and you know how to run the math … it seems magic but it’s also very straightforward.” •
Leave A Comment