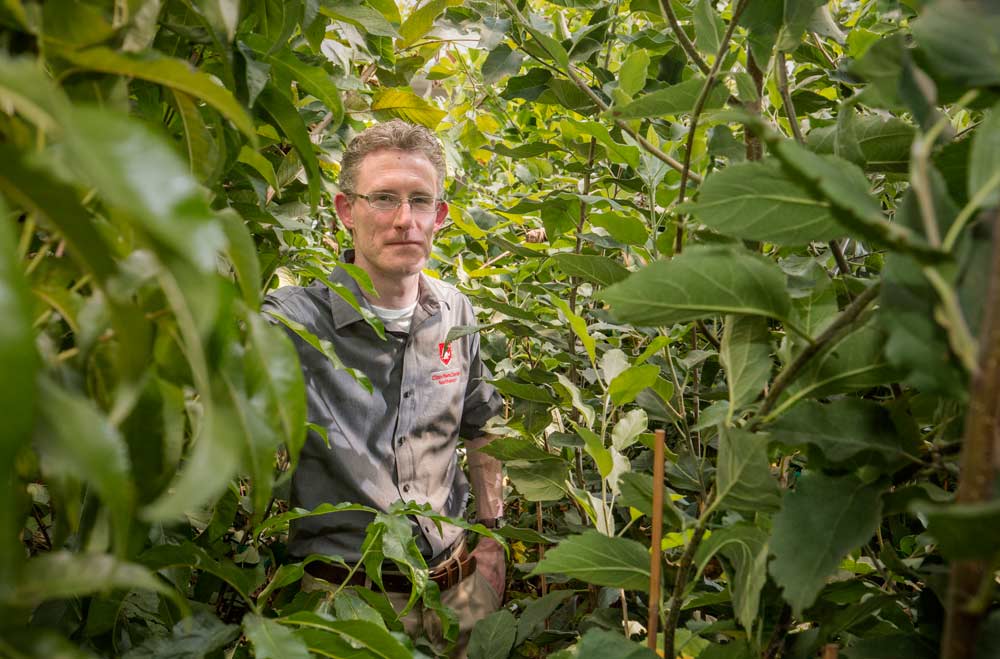
Clean Plant Center Northwest director Scott Harper is surrounded by fruit trees at the Prosser, Washington, center in August. The trees are being grown and tested for viruses and diseases before they can be considered clean and released to growers. Harper says many of the center’s facilities are at or beyond capacity to process the large amount of plant material they receive each year. (TJ Mullinax/Good Fruit Grower)
Starting a new orchard or vineyard with clean plants is the best way for growers to prevent virus problems, and demand for certified clean new varieties is growing.
However, funding for the critical work of propagating virus-free trees and vines is not keeping pace. The work of testing and treating hot new varieties and maintaining mother plants takes a lot of time and a lot of greenhouses.
For decades, the facility now known as the Clean Plant Center Northwest has led this effort and now, under new director Scott Harper, it seeks to renovate facilities, hire new staff and streamline procedures.
Today, the center — consisting of a collection of labs, trailers, greenhouses and screenhouses in Prosser, Washington — is home to both cutting-edge DNA tools and old greenhouses overflowing with shaggy trees.
It needs to keep up with the demands for new varieties and stay abreast of the best diagnostic and therapy tools, all while caring for a living library of plants put through a painstaking cleaning process so there is a source of certified wood for the future.
“We’re trying to meet the needs of the industry, but our funding and facility capacity right now can’t do that,” said Harper, a virologist from New Zealand who took the helm in January. “It’s an ongoing battle, but we’re making changes to make it more streamlined.”
The center is part of the National Clean Plant Network, which includes 27 centers across the U.S. working with tree fruit, grapes, berries, citrus, hops, sweet potatoes and roses. Created in 2008, the network is funded through the Farm Bill at $5 million annually. A share of that money in the form of grants, along with service fees, support the center.
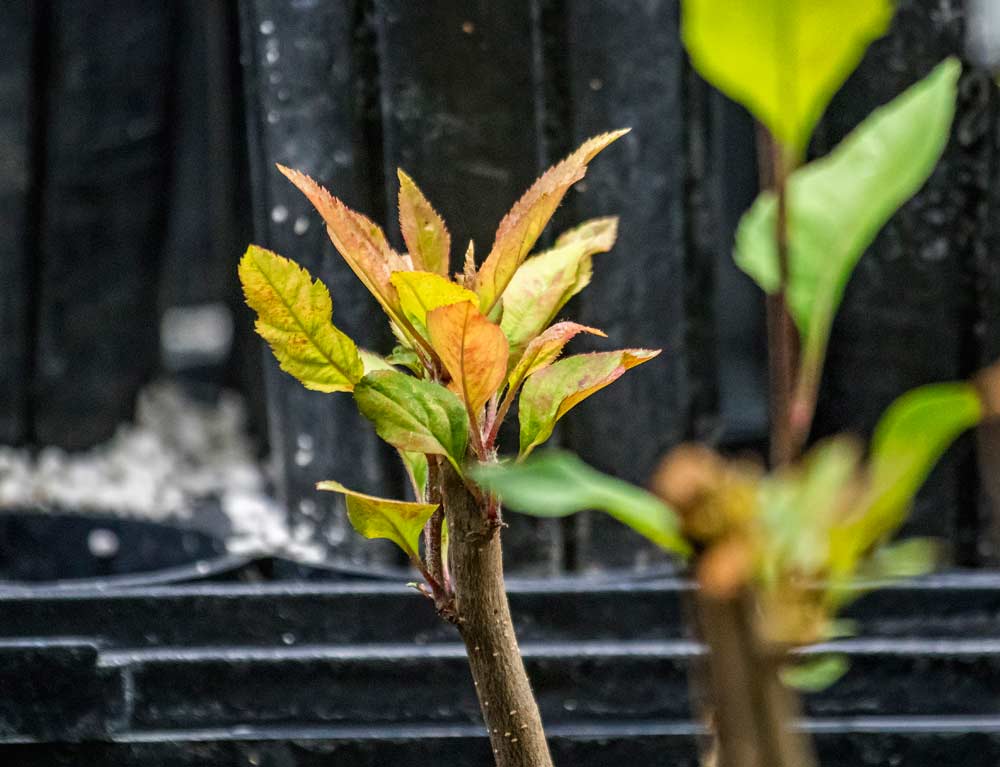
The Clean Plant Center Northwest grows, tests and certifies plant material from thousands of different fruit tree, grape and hop varieties at its facilities in Prosser, Washington. Some buildings date back to the Truman era at the Washington State University-IAREC campus. (TJ Mullinax/Good Fruit Grower)
Over the years, the number of fruit trees received by the center for cleanup has grown, but funding has not, said Bill Howell, who retired from managing the tree fruit clean plant program in 2011. There’s new technology to adopt and research to be done but it all takes money. Howell said he’d like to see more industry support for the vital program that many growers take for granted.
“Most growers are unaware of the program. They want healthy plants, but they are unaware of the program in large part because it’s been so successful in keeping viruses from being a problem in the industry,” he said. “It provides a pathway to access new varieties from around the world for our growers to be competitive on the global scale. There is no alternative.”
Testing
Housed in a collection of small laboratories at Washington State University’s Irrigated Agriculture Research and Extension Center, the Clean Plant Center’s Virus Diagnostic Lab offers growers tests for a variety of common crop viruses and serves as the first step in the clean plant process.
Many common crop viruses can be detected with an ELISA test, which uses a known antibody to look for a match with a suspected pathogen.
It’s fast and cost effective, Harper said. For other viruses, the lab uses PCR tests, which look for and amplify viral DNA for diagnosis. Both these tests can only detect a virus that the technician knows to look for, Harper said, so standard tests look for usual suspects.
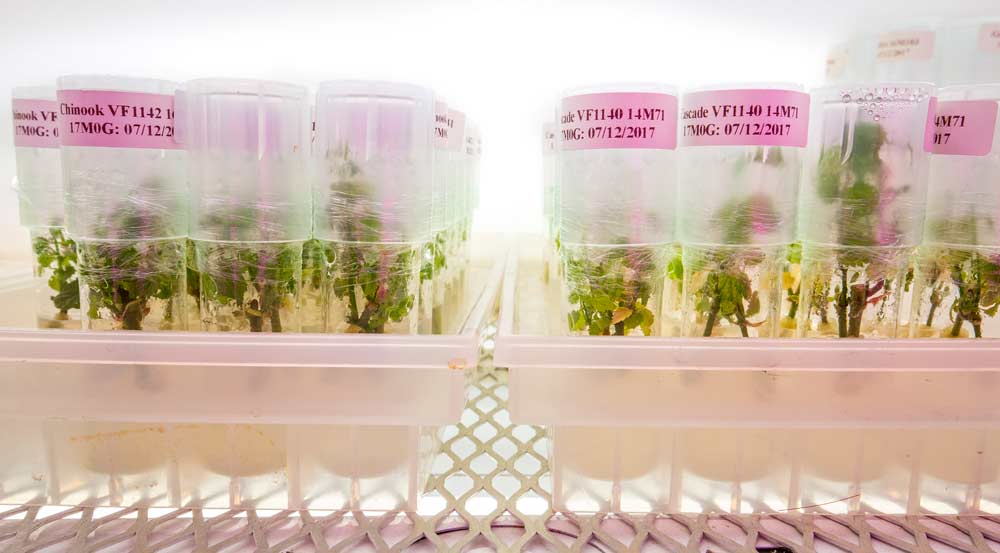
Samples of different hop variety tissue cultures grow in the Clean Plant Center Northwest indoor grow room. The lab grows hundreds of samples of grape, fruit tree and hop plants, screening for diseases and other issues to eliminate any viruses from the plant before it is selected as a mother plant. (TJ Mullinax/Good Fruit Grower)
When a grower wants to know what’s ailing his trees, these tests work well. When a plant is submitted by a nursery that wants to ensure it’s clean before propagation, the center sends samples to an outside lab for high-throughput DNA sequencing to identity every virus that might be present, even the latent ones.
Access to high-throughput sequencing was a watershed moment for clean plant programs, said Ken Eastwell, a virologist who retired from his role as director of the center in 2016.
Before that, he had to run about 60 ELISA and PCR tests on every sample submitted, along with the longstanding practice of grafting the material onto a bearing tree to look for signs of disease for several years.
That practice, known as woody indexing, has been the USDA standard for decades and only now is the agency starting to recognize the accuracy of the DNA sequencing as a valid alternative, Eastwell said.
The center continues to use woody indexing for all imports, as required by regulators, and usually uses it on domestic material because it remains a useful tool to detect problems and double check the newer tests, Harper said.
Woody indexing only catches viruses that cause symptoms, but DNA tests can turn up unknown viral “agents,” not just known pathogens, Eastwell said. The Clean Plant Center cleans up those as well, because what is “latent” in one scion rootstock combination or in one environment could cause problems in another.
“It’s a better-safe-than-sorry approach,” he said. That cautious approach, and transparency when new or unknown viruses are encountered, has built the center’s renowned reputation in the industry globally, Eastwell added.
About 70 percent of the tree fruit and grapes submitted to the center are infected with something, Harper said. In those cases, the plant moves on to propagation for therapy, but the tests continue to see if the therapy worked. The tree or vine has to pass two tests, including one a year after the therapy, before it is declared clean and released to its owner.
“Some of the viruses take a long time to come back to a testable level,” Harper said of the waiting period. In the meantime, the plants grow tall and gangly so there is plenty of material for cuttings.
In addition to testing plants, the center also tests its testing methods and works to develop new and more accurate diagnostic tools, for familiar pathogens and new ones. “There are new viruses being discovered every year. There were three or four new Prunus viruses found in the last year around the world,” Harper said. “Now we have to see if there are in here, too, so it’s a constantly evolving process.”
No quick cure
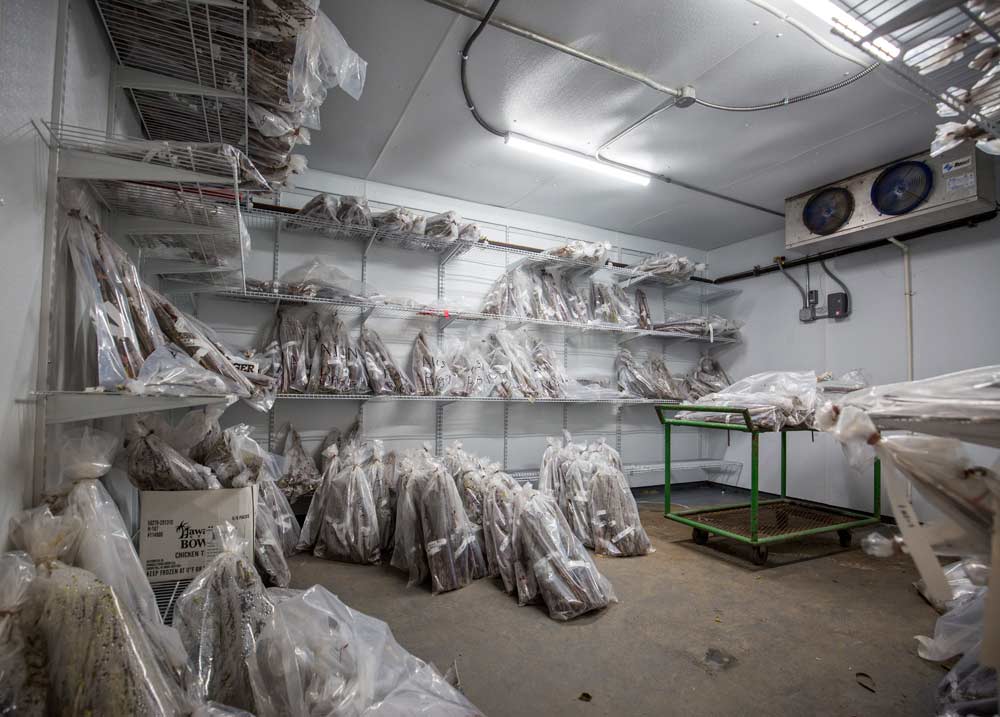
Certified clean fruit tree budwood is packaged for shipment to growers nationwide at the Clean Plant Center Northwest shipping room. (TJ Mullinax/Good Fruit Grower)
Many things have changed since the first clean plant program was established in Prosser in 1955, but the standard therapy for fruit trees remains pretty much the same. To defeat a virus, give the trees a fever. Plant viruses, just like human ones, typically don’t like heat.
“Above 35 or 40 degrees Celsius, the virus stops replicating. If it can’t replicate, it can’t move,” Harper said. “The theory is the virus will stay roughly put, but the plant will keep growing and grow away from the virus and you can chop off that piece and graft it onto a new rootstock and you’ll have your clean plant.”
But there’s no standard recipe for what each tree can tolerate and how hot it needs to be to subdue the pathogen, so it’s a trial and error process that takes many replicates to get through the treatment. One submission is turned into four plants for therapy, which are turned into 10 or 20 for testing, to result in a few clean specimens at the end.
“It’s a numbers game. Of every 10 that we treat, we might get two clean,” Harper said.
Therapy for grapes and hops is more cutting edge. Literally. Steady-handed technicians cut the vines down to just the meristem for tissue-culture propagation. It works because viruses rarely move into the meristem tissue. But, like heat therapy, the odds are still in the virus’s favor so it can take dozens of replicates in tissue culture to get a completely clean plant at the end.
Tissue culture therapy can be used for tree fruit as well, but it’s a new approach and they are still trying to develop the best methods, Harper said.
All that propagation requires skilled technicians and time. It costs about $10,000 to bring one apple variety through treatment over two years, assuming that the therapy works the first time. The center charges customers $4,000 and the rest of the cost is covered by the USDA. But the federal funding is allocated in advance, based on the center’s estimate of what it will need, and if the industry submits more plants for treatment, then the center has to cover that cost. For example, this year the center budgeted for 139 fruit trees, but received 152, Harper said.
“We’re trying to promote clean plants, so we can’t just say ‘no, go away,’” Harper said. The center uses a priority system to manage its limited funds.
“We will always take a public variety at a subsidized cost. After that, it’s proprietary varieties owned or sponsored by a Pacific Northwest company,” said Catherine Jones, the center’s coordinator. After that, it’s reintroductions and lastly proprietary varieties from outside the region.
Starting next year, after the full allocation of therapy spots partially funded by the USDA have been filled, the center plans to charge customers the full cost of the process. That will put the center on more stable financial footing to pay for investments in new infrastructure, which USDA funding can’t be used for.
Increasing fees concern Howell, who recalled the era before the Prosser center had an import permit, when people were smuggling in budwood that put the industry at risk from a variety of pests and pathogens.
“If the fees get too high at the station, we may be putting ourselves at risk,” he said, adding that for some other crops, growers decided to support clean plant work through a check-off program.
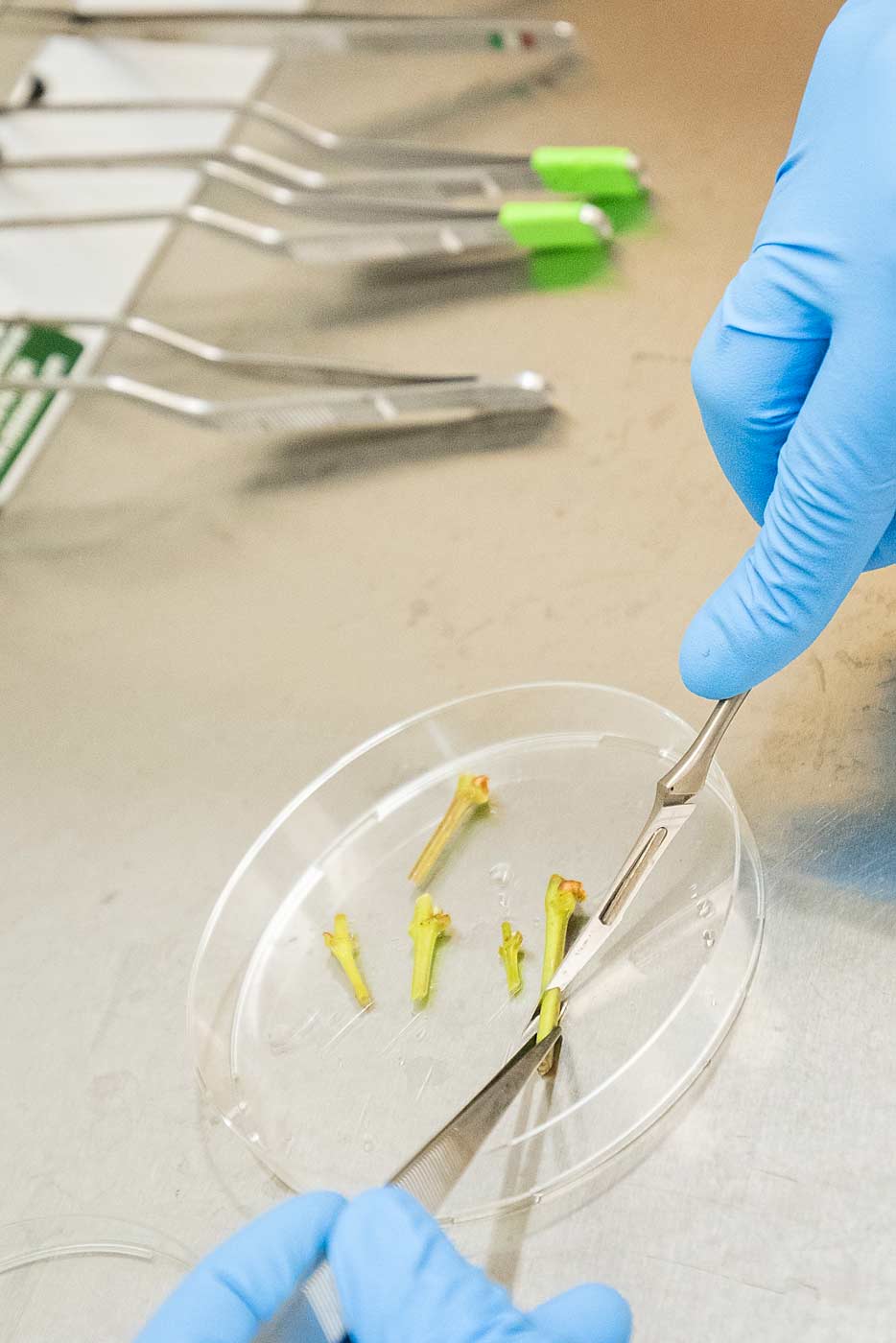
Martin Joseph, a lab technician at the Clean Plant Center Northwest, cuts grape samples during the first stage of the virus elimination process. (TJ Mullinax/Good Fruit Grower)
Foundations for the future
Once a plant has passed two successive tests to prove it’s pathogen free, it gets moved to the foundation to serve as a mother plant. Cuttings from foundation plants are then sent to certified nurseries for propagation into certified trees or vines, the second critical step in the clean plant process.
Unlike some other foundations in the National Clean Plant Network, in Prosser every mother plant is grown in pots in screen houses to insulate them from disease carrying vectors in the open air and soil.
Nine houses now hold several trees each of over 1,200 tree fruit accessions; another is under construction. About 250 varieties are public, which means the center gets requests every year to ship budwood from those trees to growers and nurseries around the world.
A walk-in cooler was filled with bags of cuttings when Good Fruit Grower visited in August, leftovers that were produced in case of orders that never came.
This coming year, they are changing the process to request orders early, so center staff know how many cuttings to prepare and cut down on wasted effort, Jones said.
In addition to propagation, center staff test each tree every five years, in an ongoing rotation of the entire collection, to ensure that they remain virus-free. It’s especially important as new pathogens are discovered and new detection tools are developed, Harper said.
New tests, new bar code systems and database to keep track of the living library, new tissue culture therapy tools for tree fruit, new staff, and new facilities to hold the ever-expanding foundation are all part of Harper’s vision for the center moving forward.
“We’ve really improved on the diagnostic side. Therapy is the area I’m focused on rebuilding and restructuring next,” he said. “Constant improvement is what we are trying to do here, because things are always changing.” •
– by Kate Prengaman
Leave A Comment