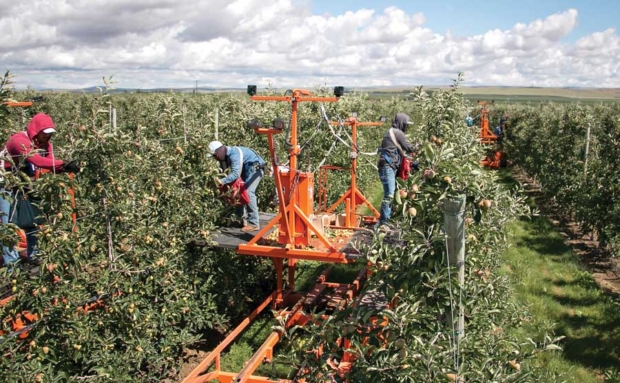
Crews of thinners atop three self-driven platforms work in June in a Stemilt Gala apple block in Quincy, Washington. Fostering teamwork is key to convincing reluctant employees to work on platforms. Ross Courtney/Good Fruit Grower
When it comes to platforms, crew supervisor Ismael Torres deals with two types of workers: Those who climb aboard and those who don’t.
In spite of the Stemilt foreman’s preaching that the tools will make everybody safer, faster and richer, some employees simply want no part. They prefer working on the ground and using ladders.
“I was just motivating them to try to see if it was going to work or not,” Torres said through an interpreter.
Platforms, mechanical thinners, hedgers and other tools of orchard efficiency make a lot of sense for growers and managers, but employees aren’t always as excited.
Many of them have spent a lifetime developing lightning quick skills that pay off under piece-rate wages, and they don’t want to change.
Multiple speakers discussed the issue at the February conference of the International Fruit Tree Association (IFTA) in Grand Rapids, Michigan. They all stressed communication and training with employees during the transition.
“Make sure that you spend and invest time in these people as well,” said Rod Farrow, a New York grower and IFTA board member. “Working with them and machinery is often difficult, getting them to accept it and work with it. They’re so used to what they are doing and so good at what they’re doing, it is difficult to get the efficiency gains. It’s easy to do in Europe, not so easy here when guys are already picking 10 bins a day of good fruit.”
Miranda Sazo, a cultural practices specialist with the Cornell University Cooperative Extension’s Lake Ontario Fruit Program in Newark, New York, encouraged growers and managers to bring Spanish-speaking employees with them to conferences to help win over employees back home.
Reasons to hesitate
Several skeptical workers declined interviews with Good Fruit Grower, but Torres, 49, shared the concerns he’s heard for the past several years as Stemilt has introduced self-driving platforms in its Quincy, Washington, orchards.
Some reasons:
On a platform, workers in crews of two, four or six all pick to fill the same bin, splitting the per-bin rate evenly come payday.
After decades of working solo with ladders, some are reluctant to hitch their fortunes to a group.
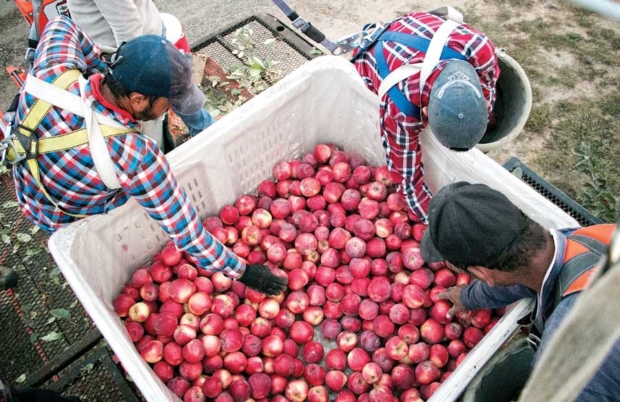
From left, Alejandro Salcido, Jesus Ventura and Anael Ruiz carefully place ripe SweeTango apples into a bin on top of an automated platform in a Stemilt orchard in Quincy, Washington, in 2014. Harvesting on platforms requires employees to pool their earnings and split them evenly, which some are reluctant to do. (TJ Mullinax/Good Fruit Grower)
Also, Stemilt deploys the platforms at night, when workers would rather spend time with their families.
Still, some employees simply don’t believe they will make as much money on a platform than with ladders, a concern that grows smaller each season as more workers prove otherwise.
A few fear falling from the machines, but not many.
Local, H-2A worker differences
Bernardo Reyes, Stemilt’s Quincy orchard manager, understands the reluctance to rely on a team, especially if workers are really fast on their own. He grew up picking fruit at piece rate, starting at age 14.
He recalls jockeying for position in a row neighboring another fast picker to push himself, almost as if they were racing.
“If they work picking, it’s because they’re really good,” Reyes said.
Reyes and Torres notice a big difference between the attitudes of the local employees and the H-2A guest workers. The H-2A workers adapt pretty quickly; the locals are the reluctant ones.
“They don’t want to give it a chance, to try it,” said Reyes, 32, who lives on the farm with his family.
Reyes and Torres suspect that H-2A workers travel and live as a unit and psychologically adjust to teamwork more easily.
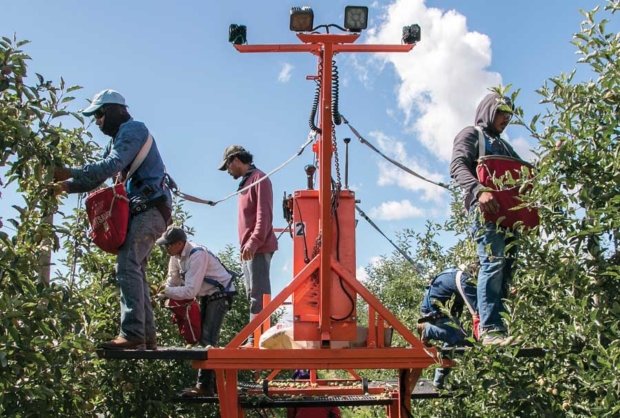
Ross Courtney/Good Fruit Grower
Ismael Torres, center, a Stemilt supervisor, oversees a crew of H-2A laborers thinning Gala apples in June in Quincy, Washington. Torres has noticed H-2A workers more easily adjust to the teamwork required by platforms than local workers, who prefer to work solo on ladders. “If the group works together, they can make more money,” Torres said. (Ross Courtney/Good Fruit Grower)
Luiz Perez Cerna, a guest worker from Michoacán, Mexico, started at Stemilt a year ago.
At first he was skeptical of blending into a platform team, but a veteran H-2A employee convinced him to try. Now, he feels safer on platforms and believes he is making more money.
“The whole time you’re using your hands to pick, not to move the ladder and climb the ladder,” said Perez Cerna, a 24-year-old father of two.
In early June, Perez Cerna and three H-2A crewmates stood high atop a bright orange platform, strapped with harnesses, thinning Gala apples. Two men worked each side, each at different heights.
Because they were being paid collectively per tree, Perez Cerna, charged with thinning the very tops, hopped over to the other side to help during the occasional break in action on his own side. Two other platform teams crawled through the orchard following the same routine.
Reyes estimated each man would make about $17 per hour that day on the platforms but would have made only $13-$14 per hour on the ground.
That doesn’t mean all domestic workers will resist mechanization. Some take no convincing at all.
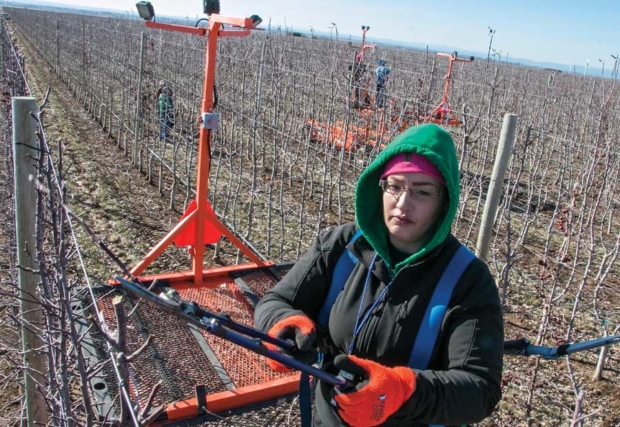
Jessica Medina of Columbia Fruit Packers prunes Kanza apples in February from atop a self-driving orchard platform while another passes in the background in Ephrata, Washington. (Ross Courtney/Good Fruit Grower)
Nearby in Ephrata, Columbia Fruit Packers also has introduced self-steering platforms at its Winchester Ranches orchard.
Candy Giron, a four-year supervisor, could think of no employees unwilling to work from a platform while pruning Kanza apples in February.
Giron, a mother of two from Moses Lake, cited safety as one her favorite benefits.
“Sometimes when there was too much snow, you were more scared of falling or when the floor was too wet, the ladder dips in,” Giron said.
Giron’s platform partner Jessica Medina, born and raised in California, also warmed to the idea of working from a platform right away.
“You get tired of carrying the ladder all day,” said Medina, also a mother of two. “You still get tired on here, but it’s not the same as when you’re carrying the ladder all day and you’re bruised up from your ankles or from the front of your legs from banging on the ladder.” •
– by Ross Courtney
Tips to help convince workers
Growers, orchard employees and experts offered a few tips for how to convince workers to use platforms:
—Pay extra. Stemilt has offered bonuses to convince workers to work from platforms and even larger bonuses to use them at night.
—Recruit workers who have made more money using platforms to tell their story to the reluctant ones.
—Invite seasoned workers and crew supervisors to conferences.
—Stress safety. Platforms reduce falls.
—Give the platform crews some level of autonomy. Stemilt lets the workers form their own platform crews and occasionally allows them to vote off a team member they don’t believe is pulling his or her own weight.
Great article Ross, congrats!
It was a great idea you interviewed the final users. Here in NY I used your article and described some of your main take home messages to Hispanic workers during the second Hispanic fruit summer tour conducted on August 13.
I hope more editors from GFG will continue interviewing the Spanish-speaking labor force, in WA, NY, or Michigan
Thanks again for your educational efforts!
Good article!