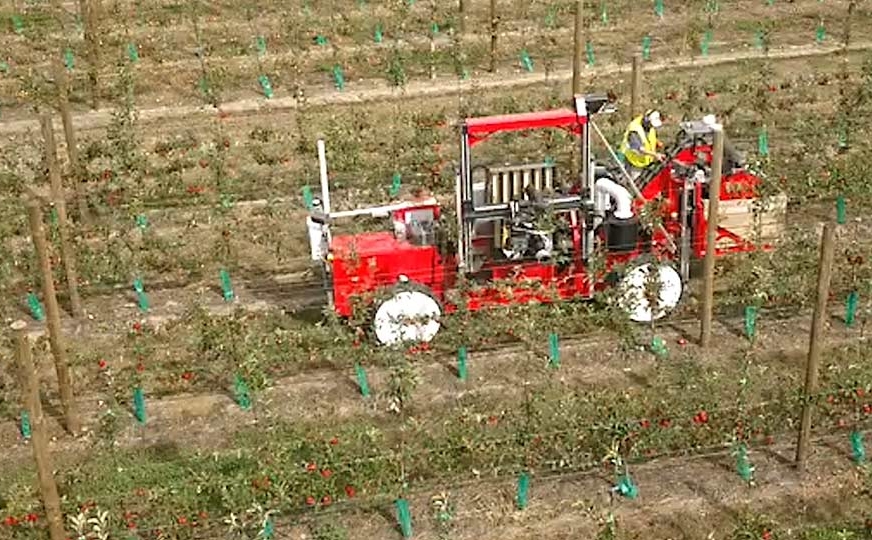
Seen in this image from Abundant Robotics’ announcement video, the latest version of its apple harvester works a commercial apple block in New Zealand. (Courtesy Abundant Robotics)
For years, T&G has been working to evolve its orchard and tree architectures to increase quality and productivity and has, in recent years, planted new orchards in two-dimensional and V-trellis systems rather than in a traditional slender spindle, COO Peter Landon-Lane said.
The goal: to increase sunlight interception and the conversion of that energy into fruit, thereby improving apple quality and consistency, as well as production per hectare.
So how have T&G’s orchards evolved in preparation for robotic technology?
Row spacing hasn’t changed much, with 3.5 meters between rows in both the slender spindle and V-trellis, and 3 meters between rows in a two-dimensional system.
However, the company has increased the distance between trees, because with the vigor seen in the Hawke’s Bay area, the trees are producing enough canopy to prune each tree in a two-dimensional shape.
The company also is pruning branches to follow along the row, allowing light interception on all layers of the tree.
It turns out those pruning and thinning decisions are more important than the details of the planting, according to Abundant Robotics CEO Dan Steere — as long as it’s essentially a high-density planting on the types of dwarfing rootstocks that have been used for a long time.
“Because of the evolution of the technology and the orchard itself, we will still be improving more as time goes by — fine-tuning our orchard practices in order to improve the productivity benefit we get from robotic picking, and also to use the technology as part of our overall mix of tools at our disposal,” Landon-Lane said.
For example, the robotic harvester can pick 24 hours a day, including at night.
The machine is handling the upper portions of the orchard, “so when people come through later, they can pick all the lower fruit on the tree, reducing all those vertical miles pickers typically have to do on ladders,” he said.
—by Shannon Dininny
Related: Robotic picking machine’s first apple harvest underway
Leave A Comment