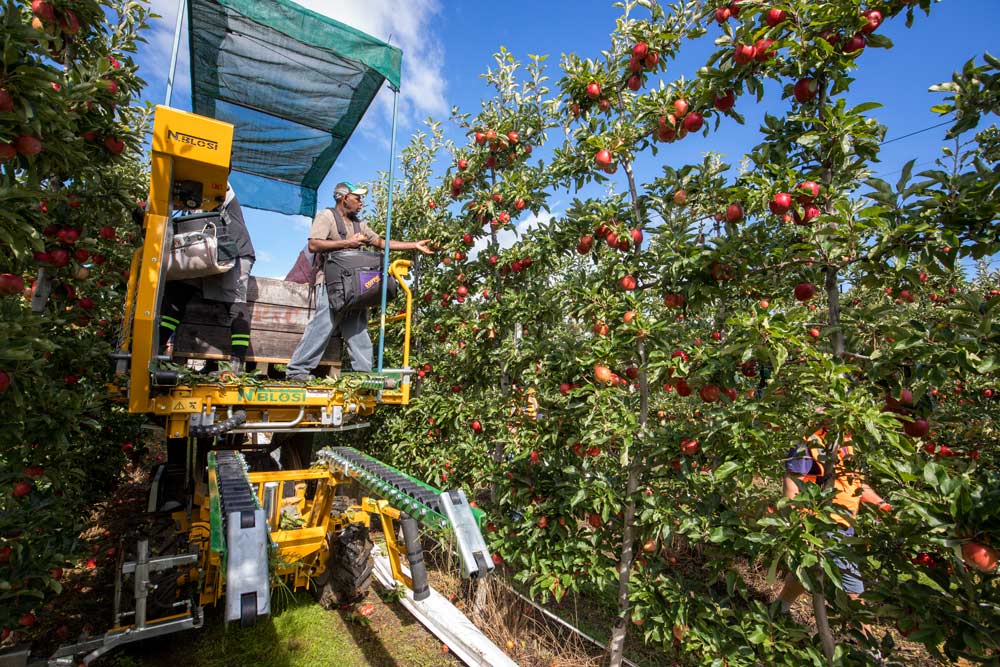
From a platform, a crew of four workers pick Royal Gala apples at Hoddy Fruit Co.’s orchard in the Nelson, New Zealand, area in February 2018. This narrow 2D system, coupled with open “windows” allowing light through, was one of the International Fruit Tree Association study tour stops. (TJ Mullinax/Good Fruit Grower)
The aging, four-dimensional trees in Hoddy Fruit Co.’s New Zealand orchards were still producing 50 tons or more per acre, but the fruit at the bottoms of the trees too often was shaded from sunlight, and overall fruit quality wasn’t what it could be.
Given that New Zealand sits some 12,000 miles from key export markets, every piece of fruit has to be top quality, because that is the island nation’s only point of difference in the global marketplace.

The 2D system at Hoddy Fruit’s orchard allows for even distribution of light to fruit from the top of the trellis to the bottom evenly through open “windows” in the canopy. (TJ Mullinax/Good Fruit Grower)
“So one of our biggest drivers, when we made the decision on the different growing system, is what is going to maximize the number of fruit that is actually going to be a good eating piece of fruit,” said Andrew Kininmonth, who shares management of the orchard with his father-in-law, Michael Hoddy. “It has to be quality, has to be consistent, and it has to be people wanting to come back and grab our apples every week.”
That’s why Hoddy Fruit Co. is among a growing number of orchards transitioning to two- and three-dimensional orchard systems, similar to other key growing regions of the world, with a goal of increasing production and improving fruit quality.
In time Hoddy Fruit and others expect to be more efficient through automation and robotics down the road.
Hoddy Fruit is moving more to 2D systems, which Kininmonth said relates to one thing: the need to harvest light.
Creating windows in the canopy enables dappled light to fall across and through the entire canopy, including shaded apples near the bottom. That improves packouts.
“If we do our jobs, create windows, keep the windows open in the canopy, we do well,” he said. “We’re not apple growers. We’re actually farmers of light.”
“Everything we plant now, we have to find a reason why wouldn’t we plant it on 2D,” he said.
The concept of farming light was a familiar refrain during the International Fruit Tree Association annual conference and study tour in February.
Researchers and growers alike shared their experiences with highly uniform, trellised systems, both 2D and 3D, intended to improve the quality of the fruit throughout the canopy, not just in the treetops, and to improve overall yields.
Researchers at the New Zealand Plant and Food Research Center have been investigating the potential of planar cordon intensive planting systems for several years.
Those are systems designed to intercept sunlight and then use that sunlight to push yield potentials and quality to “close to the upper limits biologically,” said principal scientist and plant physiology group leader Stuart Tustin.
Researchers are testing the limits for spacing, planting rows close together and leaving a very tall, narrow, slim, porous canopy where leaves are oriented and arranged to allow good light distribution from the bottom to the top of the tree. So far, they’re testing 2 meters and 1.5 meters between row spacing. (1 meter is a little over 3 feet.)
“Theoretically, the rows more close together are going to give us higher sunlight utilization, but we may get into problems of shading if the rows get too close,” he said. “It is too early to say which is better at the moment.”
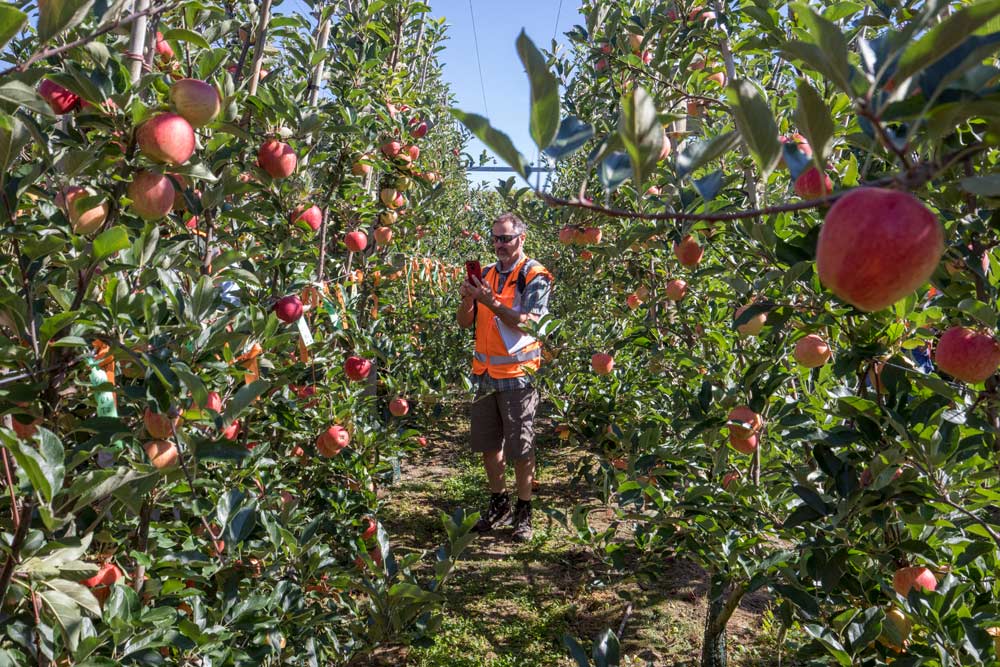
Chris Paganelli, from Yakima, Washington, isn’t taking photos of being swallowed by an apple orchard — he’s actually standing in one of Stuart Tustin’s future orchard system test blocks at the New Zealand Plant and Food Research Center in the Hawke’s Bay area. (TJ Mullinax/Good Fruit Grower)
Other practical considerations must be considered as well, he said, including the ability for multiple row spraying and amenability for robotics once they are developed.
“I like to think that they would be developed to work in a confined space, not an expansive space,” he said. But, either way, “we are talking about doubling the productivity of apples.”
Video – 360 VR
Step into the orchard with Tustin as he talks about increasing apple system productivity at the New Zealand Plant and Food Research Center. (Be sure to use your mouse in a web browser or move your mobile device around to “look” around Tustin’s trial block.)
In the orchards
Birdhurst Orchard, located in the widest part of the Motueka Valley near Nelson, New Zealand, once was a 15-acre tobacco and cattle farm. Today, the expanded farm is planted in 500 acres of intensive dwarf apple trees —Royal Gala, Jazz and Braeburn blocks averaging 1,200 trees per acre — and 150 acres of kiwifruit.
Together with Heywood Orchards, the two farms also comprise the joint postharvest venture Golden Bay Fruit 2008 Ltd., whose goal is to get as much of the export receipts back to the orchards — the growers.
Currently, Golden Bay averages about 70,000 bins annually, but with new plantings, systems and packing house expansion, that should be closer to 100,000 bins within three to four years, said Golden Bay’s Anthony Heywood.
A Jazz block planted on Malling 9 rootstocks, planted at about 810 trees per acre, should produce close to 101 bins per acre this year, up slightly from 2016, orchard manager Aaron Cederman said.
That’s because they’ve worked hard to push trees, with more long and skinny 6-to-8-inch side darts and less crop load on the ends of the branches, in order to better harvest light. The aim: about 217 fruit per tree with a 115-count harvest size.
Several years ago, the trees were under-pruned and carrying up to 27 branches per tree. That’s down to about 17 branches now. “By carrying most of the fruit on spurs, the flowering window is narrowing,” he said. “I’d rather have a long, skinny branch starting high and ending at my knees.”
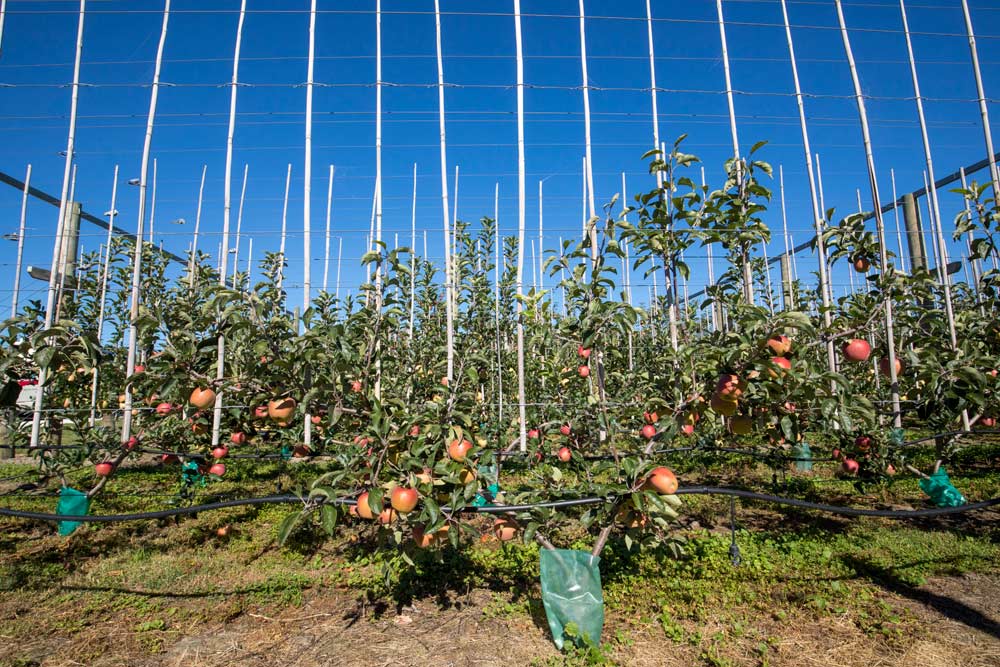
One of the experimental trellis systems at the New Zealand Plant and Food Research Center in the Hawke’s Bay area seen during the IFTA study tour in February. This particular row was candelabra-like, with 11 to 12 leaders per tree. (TJ Mullinax/Good Fruit Grower)
In a Royal Gala block, stiffer branches sitting at 45-degree angles can’t always be pulled down, so those branches going into the next tree come out and workers leave stubs, he said.
Row spacing is quite narrow at a Hoddy Fruit Co. Galaxy Royal Gala block, planted on Pajam 2 rootstock at 2.5 meters, or just over 8 feet. Trees are planted not quite 4 feet apart and stand 12 feet tall, trellised to an eight-wire system with wires spaced at 15 inches.
The canopy is at about 85 percent throughout the block, and the wires provide pretty good light interception, Kininmonth said.
He’s aiming for 90 percent color and 140 fruit per tree, with an average size of 100. When the visitors toured, workers had already skim picked the tree bottoms and were picking the tops with platforms.
So far, they haven’t needed to replace laterals along the wire, largely by keeping two to three ages of wood coming off a branch at a time, he said.
“We just chop it to two buds. We break all the traditional rules of pruning in a 2D system,” he said. “If there’s a spur of buds, we’ll just halve it.”

IFTA study tour attendees watched a demonstration of Intelligent Fruit Vision’s latest update to their vision system within one of Palmer Orchards’ 2D Envy blocks. (TJ Mullinax/Good Fruit Grower)
Meanwhile, shaping trees has been a challenge for Ian Palmer in an Envy block on M.9 rootstock at Palmer Orchards, planted on 3.3 meters by 1 meter along row spacing.
The site had a varied history when it was young, and with virtually no tree training in the early years, overcropping has been an issue, he said. This season, he estimated the block was 5 to 10 percent overcropped, largely in the tree tops. He expected to harvest nearly 110 metric tons. (A metric ton is just over 1 U.S. ton.)
Envy poses challenges with big fruit that can be hard to color, but reflective material has helped to improve packouts. He also applies magnesium every two weeks because, though soil tests show the mineral is in the soil, it doesn’t appear to be available to the plant. “If I can hold leaf color, the fruit will color well,” he said.
Craig Hornblow, AgFirst horticultural consultant, noted that in the winter, “there’s not much of a tree here.” Palmer said his workers aim to remove all the spurs from inside of the branches. A bonus: European canker had slowed the orchard, but with less light intensity in the block, he’s confident he can manage it.
Palmer grows a mix of Envy, Jazz, Ambrosia and Royal Gala. “The industry here is always looking for the next big apple. I think the ones we have now will see us through for a while,” he said. “Like any new apple, we have to learn how to grow it well to make a success of it.”•
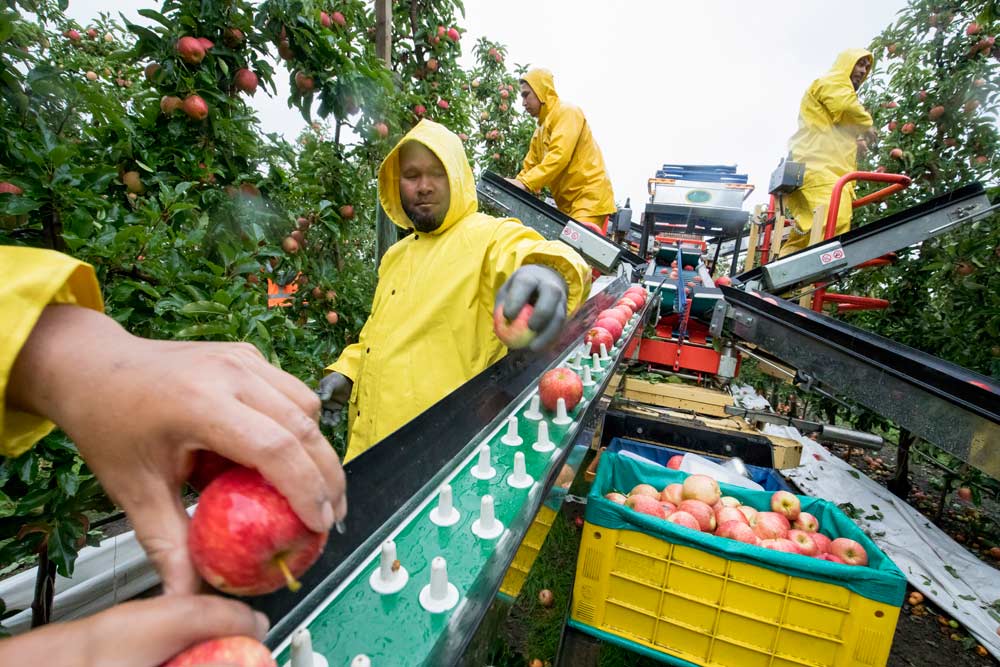
Workers harvest Galas through the beginning of tropical cyclone Gita at Vailima Orchards near Nelson, New Zealand, using platforms to navigate a narrow 2D trellis system. (TJ Mullinax/Good Fruit Grower)
Guest workers in New Zealand
Similar to the United States, New Zealand also has a guest worker program, though with residents of Pacific Island countries to fill seasonal farm jobs. Known as the Recognized Seasonal Employers scheme, the program enables growers to bring in workers from about a half-dozen island nations, with many drawing workers from Tonga.
Under the RSE, employers must attempt and be unable to recruit local workers before obtaining permission to recruit guest workers.
They also must pay half the cost of a return ticket for Pacific Island migrants, guarantee a minimum number of work hours and a minimum wage, and provide housing, health insurance and assistance with personal needs such as transportation for banking.
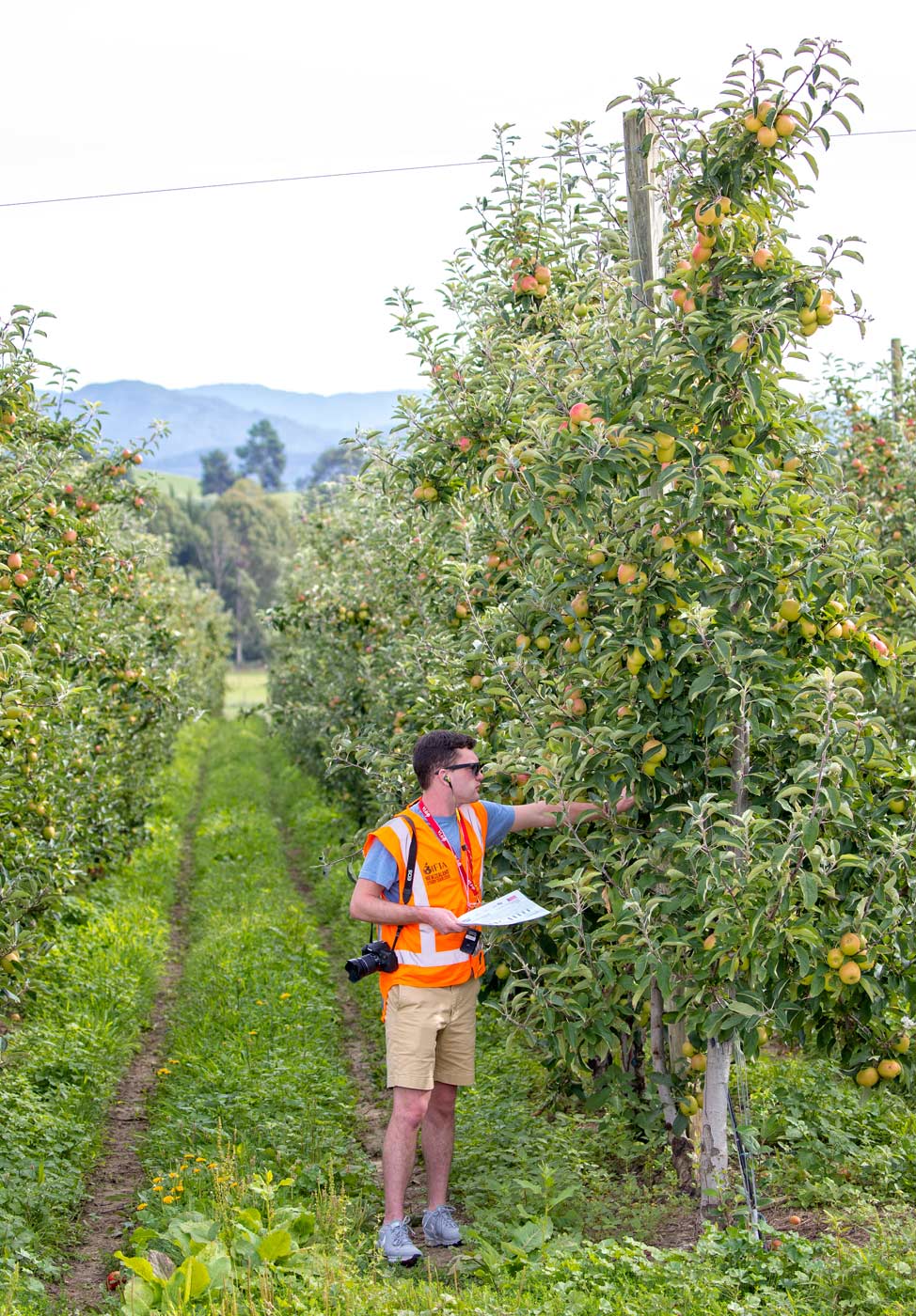
Matt Murphy, from Geneva, NY, inspects one of Fairfield Orchard’s uncovered blocks in Motueka, New Zealand during the 2018 IFTA New Zealand Study Tour in February. (TJ Mullinax/Good Fruit Grower)
Notes from Birdhurst Orchard
The farm aims to set as much fruit as possible on spurs, cutting blind wood in dormancy. About 25 people hand-thin the block on instructions from a supervisor, and when they’re told to thin, they’re told why.
“If they know the reason they’re doing it and why they need to do it a certain way, we’ve gotten a more consistent result,” orchard manager Aaron Cederman said. “They self-monitor, because a worker doesn’t want to pick that row that’s been thinned wrong.”
With the shift to planar canopies, the orchard also has been experimenting with multi-row sprayers that allow them to spray the farm in an eight- to 10-hour window, beginning at 5 a.m. before the heat hits. Standard spacing is 0.9 meters by 3.3 meters (not quite 3 feet by 11 feet).
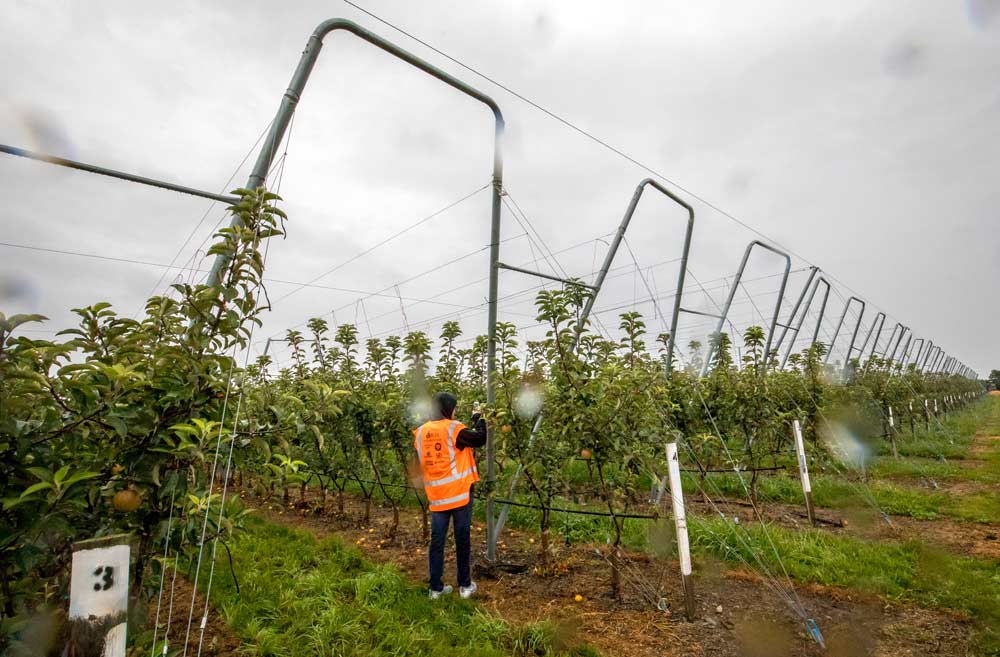
An IFTA study tour attendee takes photos of the steel work at Vailima Orchard during tropical cyclone Gita in the Nelson area of New Zealand in February. (TJ Mullinax/Good Fruit Grower)
Notes from Vailima Orchards
Everything the Hoddy family of Vailima Orchard does is leading edge, whether it’s pursuing new varieties or introducing multi-row sprayers and all-season platforms to their orchards years ago, said AgFirst horticulturalist Craig Hornblow.
The family also is among the first in New Zealand to turn to a V-trellis system, with metal posts, to improve efficiency and maximize the opportunities of new varieties, including Ambrosia, Jazz, Envy and Smitten.
Tree spacings vary too, as they learn more about the system for each variety. An Envy block grafted three years ago starts at 3.4 by 1 meters for the first 12 to 13 rows, then gets closer, to 3.4 by 0.8 meters.
An Ambrosia block on M.9 is planted at 1 meter apart, with 3.5 meters between rows and yields about 70 metric tons per hectare. (1 hectare is a little smaller than 2.5 acres.) Richard Hoddy said they put down reflectives to improve color and harvest in three picks over two weeks.
Generally, they’ve set a threshold for a minimum of 80 metric tons/hectare, and the goal is to reach 120 to 130 metric tons per hectare (or about 120 to 130 bins per acre), and “we think we’re going down a reasonably good pathway,” Hoddy said. “Already we’re getting 140 tonnes per hectare on Braeburn on Extenday.”
This season, Richard, along with wife, Sue, and sons, Matthew and Tristram, planned to harvest 30,000 bins. That’s expected to increase to 40,000 bins in five years as new orchards come into production.
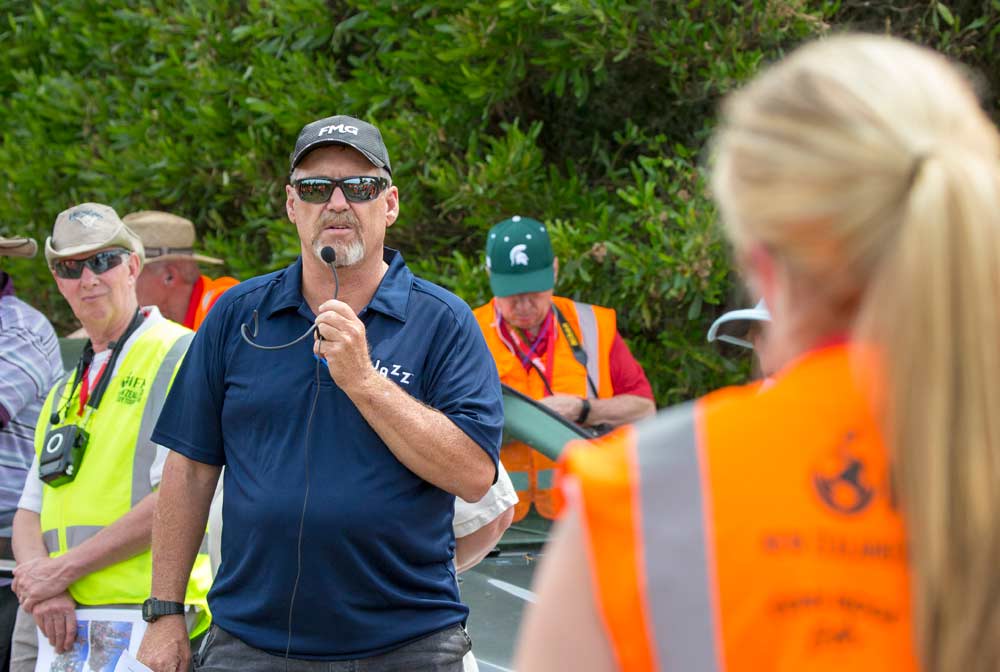
Ian Palmer talks to IFTA New Zealand attendees about how he instructs his workers to prune the 2D high-density Envy blocks in the Nelson area in February. (TJ Mullinax/Good Fruit Grower)
Notes from Palmer Orchards
Water is king to everything they grow in the Nelson/Tasman region, grower Ian Palmer said, and water is monitored and limited during drought years. That’s a key consideration in his light soils with low holding capacity.
In the temperate seasonal climate, not too far from the coast, king blooms emerge and shed
before the next bloom comes on. Palmer does two secondary thinnings and removes as much of the annual wood bloom as possible. For fruit thinning, he hand thins early and a month before harvest.
He also fumigates for any replant situation to avoid apple replant disease. “If we don’t, it’s a disaster,” he said.
—by Shannon Dininny
Leave A Comment