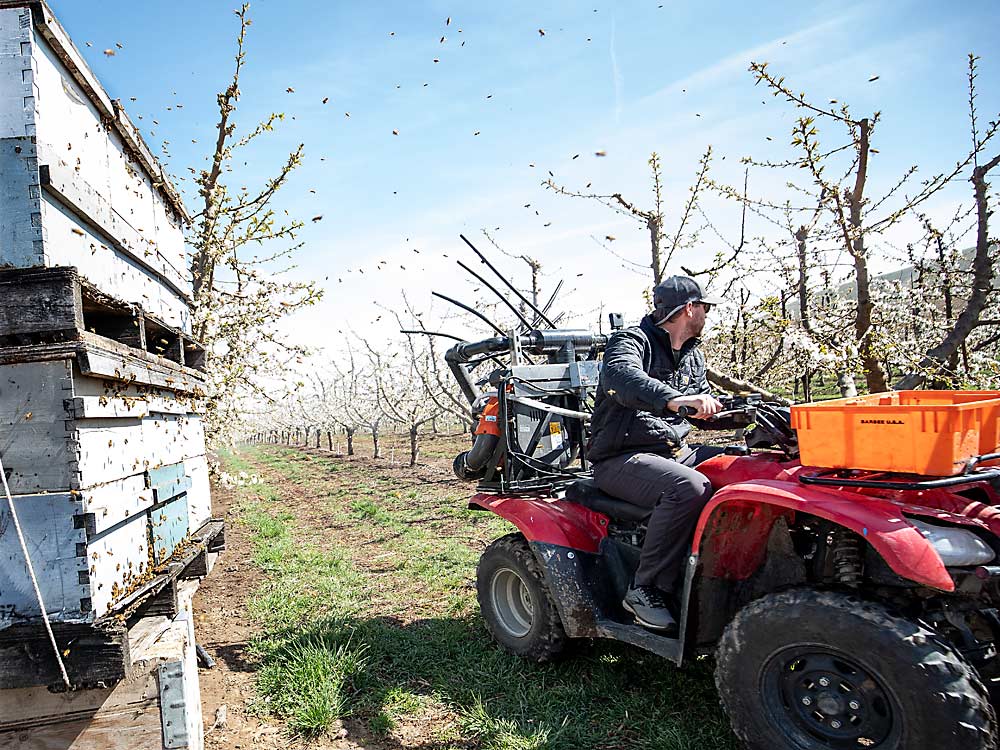
Cherry growers don’t have anything against honey bees. They spend upward of $200 per hive each spring.
They just don’t completely trust bees. Cherries are too high-value to risk the crop on bee pollination alone when the bees and blooms are at the mercy of variable weather.
“You almost need every cherry to set,” said Keith Veselka, co-owner and orchard operations manager for NWFM, a farm management company with fruit blocks throughout Central Washington.
So, cherry growers are turning to machinery to give their insect pollinators a little help. Veselka and other cherry growers have invested in equipment to spray a pollen slurry or drop it from drones. One industrious duo even mounted a backpack leaf blower onto an ATV to emit dry pollen in undersetting blocks.
“As a pollen company, we provide the pollen, but we’re just trying to find the best way to apply it,” said Scott Beddard, general manager of Pollen Pro of Moxee, Washington, one of the pollen vendors helping drive some of the innovation.
The techniques range from commercial to experimental. None of these supplemental pollen practices is aimed at replacing the work of bees, and all capitalize on static electricity.
Bees build up a positive charge by buzzing their wings, which sheds electrons. Flowers have a negative charge, which both attracts those bees and helps pollen stick to the stigma, where it will be most beneficial, according to Beddard and other pollen specialists.
From the air
Dropcopter, an unmanned aerial vehicle startup, designed its drone to maximize static electricity. Helicopter rotors produce an electrical field, but the company built a six-rotor drone using proprietary materials that accentuate the charge, said Mike Winch, chief technical officer of Dropcopter. The Syracuse, New York-based company touts about $1.5 million in venture capital investment.
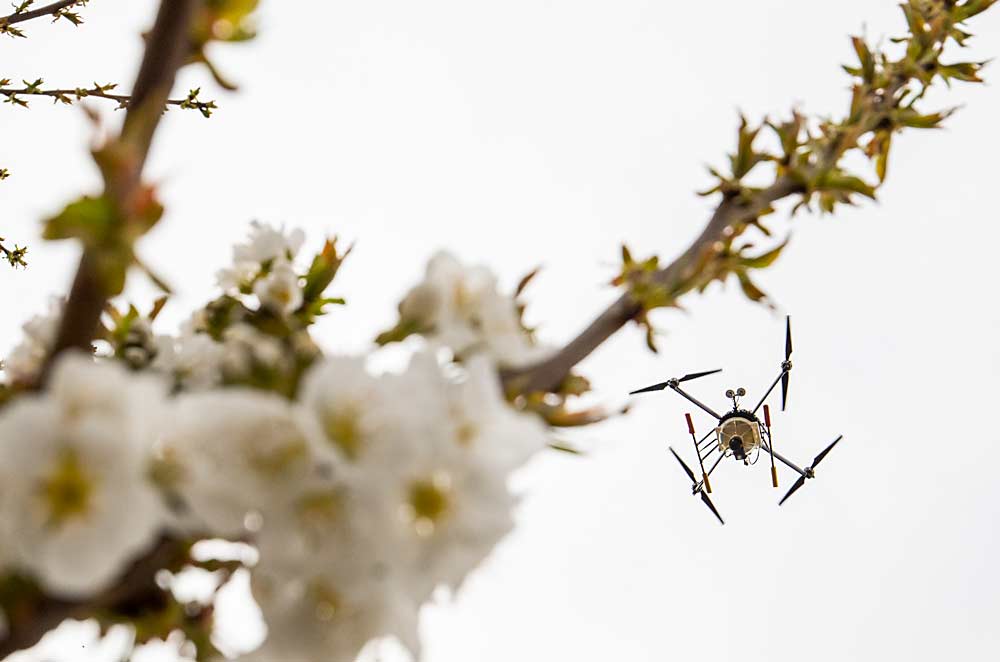
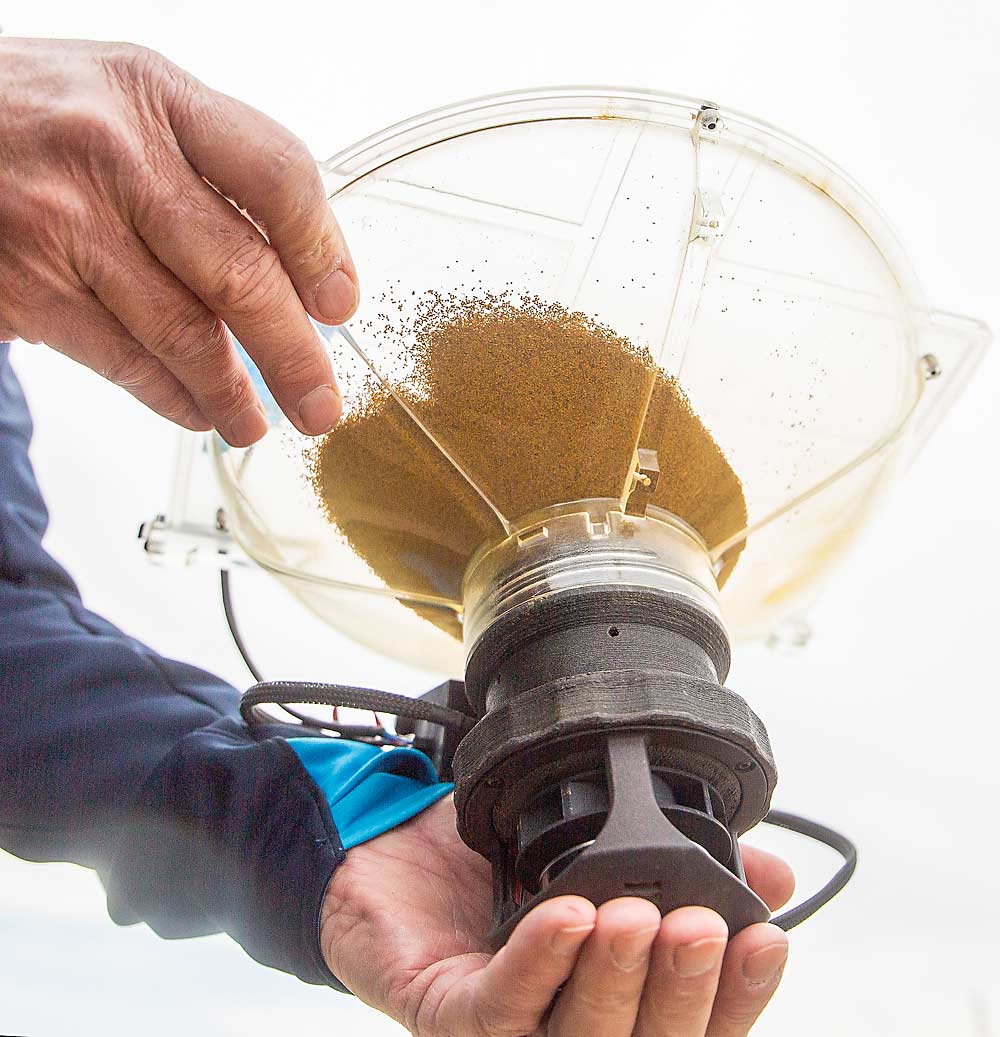
The specialized drone hovers just a few feet over the canopy and propels pollen downward at a prescribed rate. The company also built a pollen hopper that attaches to the drone and designed the mapping software to control the copter.
Though pollen is hard to see falling from the drone, it penetrates beyond the canopy top; staff have caught the grains on sticky test strips near the trunks of mature trees, Winch said. The company has commercial clients of up to 100 acres in New York and smaller customers in California and Washington.
Veselka tried out the service this year on a block of Early Robins near Benton City, Washington, a windy site that sometimes grounds bees. Moreover, Early Robins bloom early, when weather might be too cold for bees.
“I think we’re looking to augment bees,” Veselka said.
To measure how well the applications worked, he used ATV-mounted sensors developed by Australian agricultural technology firm Green Atlas to count blooms. FarmCloud, the Washington-based Green Atlas license holder, planned to return with the camera system later to count fruit.
An empirical verdict is still out for David Mendrin of Fresno, California, but he liked what he saw this year from Dropcopter.
Mendrin, a field representative for packer Morada Produce, brought in Dropcopter to test its pollination services on about 15 acres owned by his father. He knows the row where the company pilot started his flight, but not where he ended. However, he believes he has visually noticed a more consistent fruit set on the drone-treated rows and can tell where the copter stopped its application.
Uniform fruit set is the holy grail in California’s Central Valley, where cherries are finicky, he said. Consistent set helps growers minimize labor expenses, boost yields and deliver better quality to their packers. He grew up spreading pollen in beehive entrances.
“Every little niche advantage we can get adds up,” he said.
From the ground
In other developments, a proprietary pollen suspension developed by Washington State University researchers is now being regularly applied by two ground sprayers.
On Target Spray Systems of Mount Angel, Oregon, runs an electrical current through a tree-high stack of electrostatic spray manifolds that charge the fluid as it exits the valves. In fact, On Target was part of WSU’s trials over several years, before the university and Firman Pollen commercialized the sugar-based tank mix to which growers add dry pollen right before application.
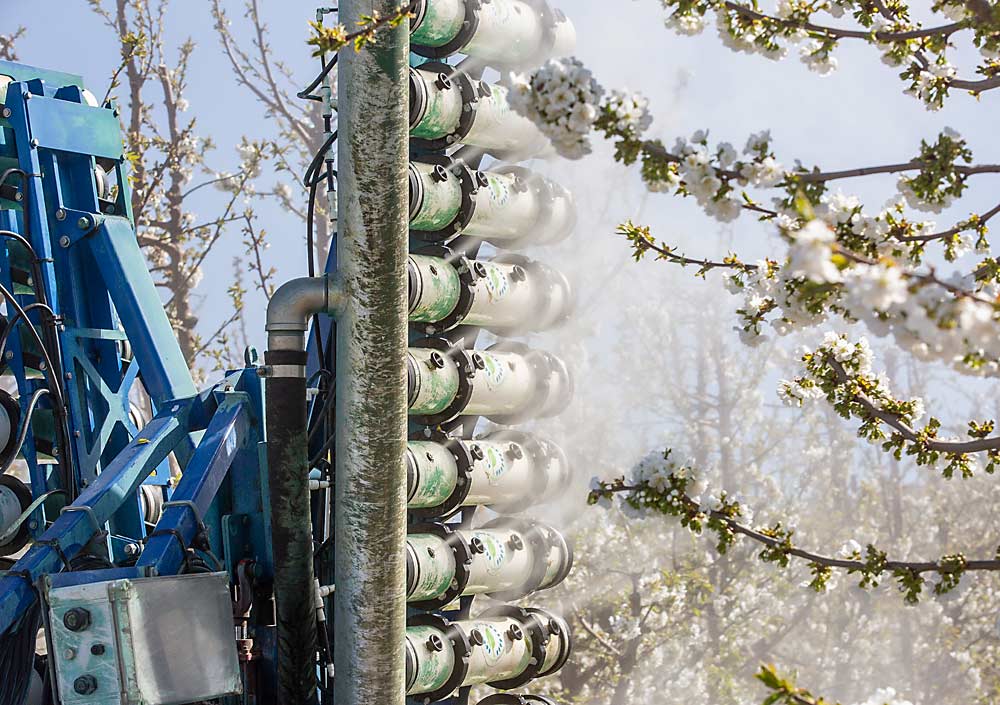
Progressive Ag of Modesto, California, is the other sprayer manufacturer that sprays the pollen solution. Its LectroBlast sprayers charge a metal plate near the valves to create the electrical field when applying the pollen.
Electrostatic spraying has been around for decades, but both companies have used the technology for pollination commercially throughout the West Coast for the past five years.
“We’re using it on thousands of acres at this point,” said Ryan Reisbick, co-owner and CEO of Firman Pollen, a Yakima-based company that grows its own pollen-only cherry trees to help feed the growing market. The pollen and tank mixture package runs roughly $240 per acre, about double the price of dry pollen alone, Reisbick said.
“The idea is to increase efficacy of our product,” Reisbick said.
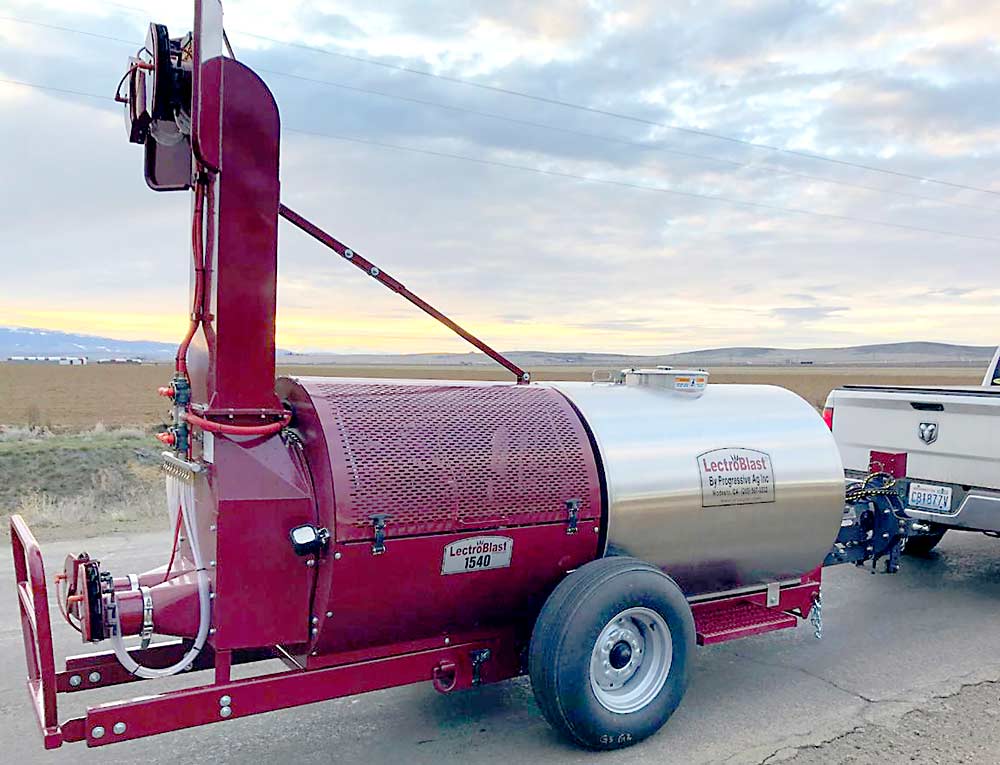
Shawn Gay, a grower with Central Washington cherry blocks in Kennewick and Benton City, has used the suspension with On Target sprayers for roughly four years. He has noticed a bump in fruit set, but it’s hard to measure, he said.
“We think it helps,” Gay said. “How much it helps depends on the year.”
In years with good pollination weather, the bees do well on their own. In poor weather, the pollen spray helps out more. But cherries are so expensive to grow and fetch such a tight margin, even a half-ton improvement per acre makes the investment worth it, Gay said.
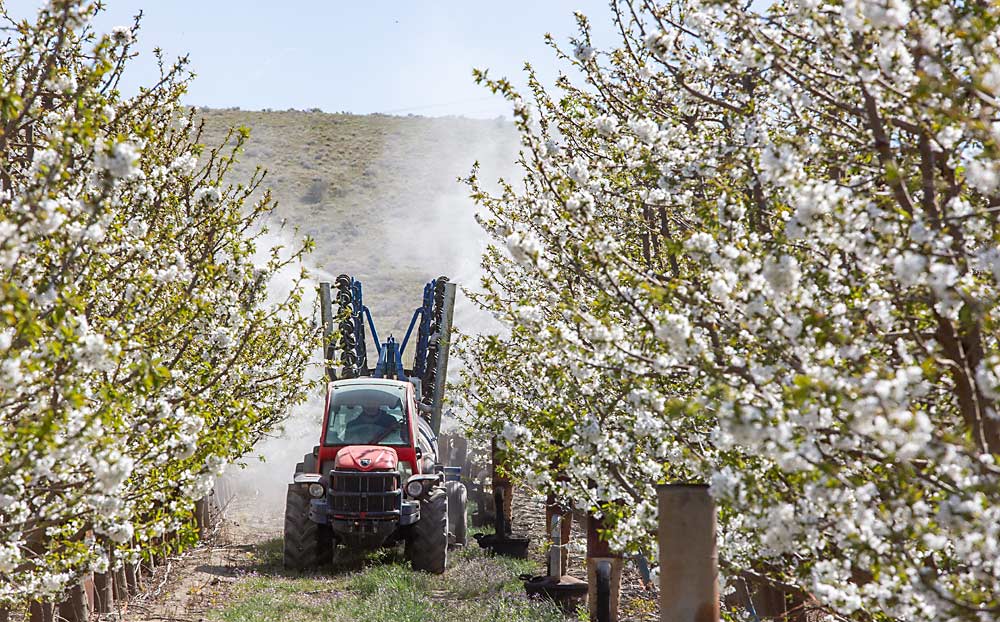
Matchmaker
Firman and Pollen Pro are both cultivating new techniques to give their grower customers new ways to apply supplemental pollen, moving beyond the beehive strips and dry puffers of yesteryear.
Beddard of Pollen Pro has played a bit of matchmaker: He helped link Dropcopter with Veselka. He also has teamed up with Moxee grower Craig Harris to build a proof-of-concept electrostatic dry pollen applicator that mounts to an ATV. Kyle Crowston, Harris’ operations manager with a background in electrical engineering, built the prototype with a backpack leaf blower and copper wire to create the charge.
Beddard got the idea from a business associate in California who used an electrostatic sprayer for powder coating machinery and later figured out a way to repurpose the technology to spray pollen in almond orchards.
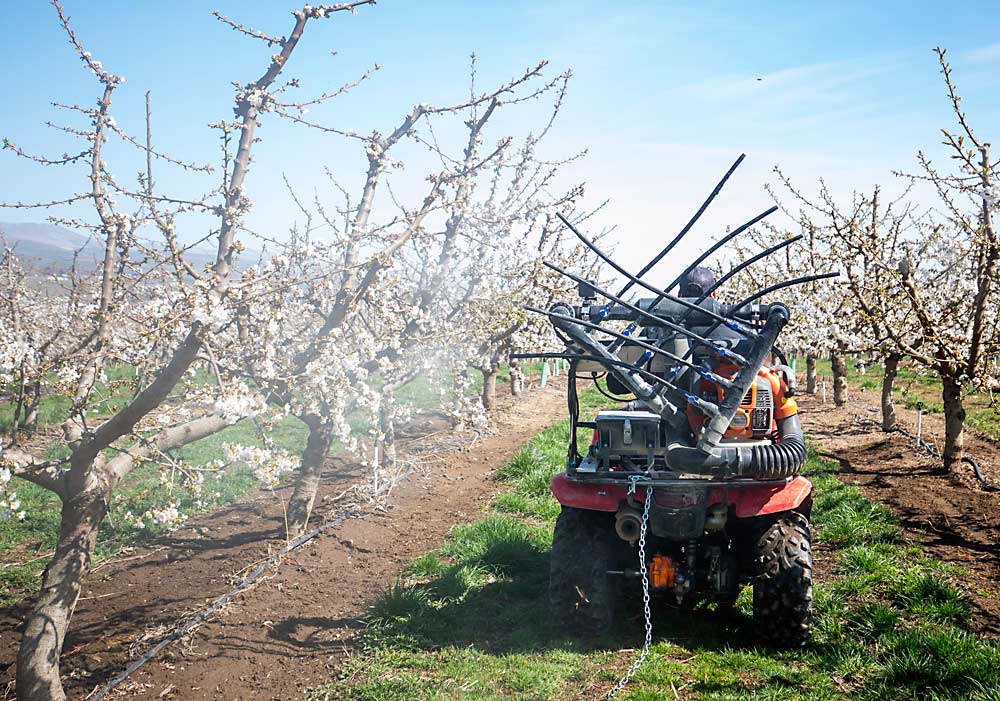
Harris tested it this year on his orchards. He grew up blowing dry pollen without an electrical field and placing extra pollen at the entrances of hives. Results have always been inconsistent, he said. So, he’s trying the new machine on blocks that tend to underset, often due to poor bloom coordination.
Beddard also has borrowed a pollen viability tester, a $60,000 piece of equipment that’s about the size of a microwave and runs an electrical charge through dry pollen to determine if it’s alive in a matter of minutes, rather than hours with an agar dish. He doesn’t yet offer that as a service, but he aims to give his grower customers more assurances that his pollen is going to work as intended.
The fruit industry is ripe for advances in pollen technology, Beddard said. Some will work, some may not.
“It’s like a shotgun approach,” he said. “We’re just hoping the pollen lands where it’s supposed to and hoping the bees move it where they’re supposed to.” •
—by Ross Courtney
Leave A Comment