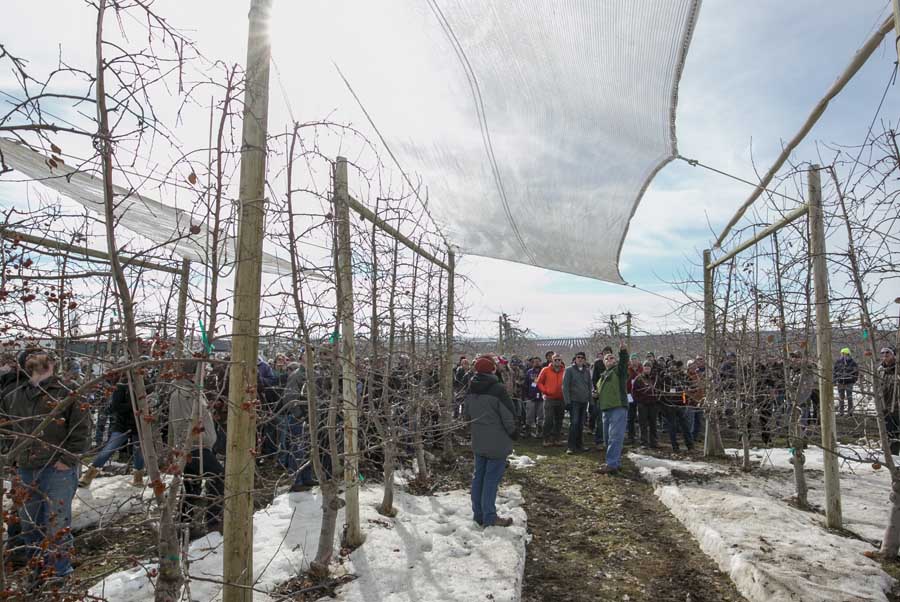
Mike Robinson talks to IFTA participants about his partial, tilted shade cloth in one of his Mattawa, Washington, apple blocks. The smaller size and tilt helps Robinson protects against sunburn and hail. (TJ Mullinax/Good Fruit Grower)
At Willow Drive Nursery in Ephrata, co-owner Jim Adams explained how mechanization is helping the labor-intensive business meet growing demand for new trees. “We harvest about five million rootstocks and we can harvest the whole crop in eight to ten days,” Adams said, as attendees checked out his custom-built harvester.
And a tree sorting line that can grade 66 trees a minute significantly increases how many trees his staff can pack every day, Adams said. But it only works for some varieties; the more fragile or branchy varieties still need to be packed by hand, he added.
Preparing for mechanization and maximizing labor efficiency continued to be a common thread on tours of three orchards on the Royal Slope and in the Mattawa area.
At BMR orchards, co-owner Mike Robinson discussed how he is trying to prepare a bi-axis Fuji orchard for mechanical harvest. Experiments with a mechanical hedger illustrated that growers face trade-offs in adopting new technologies.
“We can’t have hard wood sticking out into the row,” Robinson said, shaking a shorn branch remaining after a mechanical hedger trial. “The mechanical hedger will not work with the mechanical harvester. We need to hand prune it and train it first to get that wood out of it.”
Further south at a Stemilt Growers orchard in Mattawa, a Fuji block was planted on vertical system with a 12-foot spacing. That’s key to successful use of a picking platform, Stemilt’s Robin Graham said. “The platforms can come in and pick the top first and pick the bottom when they are ready,” Graham said. “With 10-foot spacing, you have to pick the bottom before the platform can get in.”
After a day admiring trellis systems, attendees at the ended their second day of tours watching Ambrosia apples roll through McDougall & Sons’ state-of-the-art packing house in East Wenatchee.
Now in its third season of operations, the apple facility features a 12-lane sorting system that has the capacity to move 500 bins per day per shift, said McDougall’s Brent Milne on the tour. Negative pressure is used in the wet room to keep down humidity and positive pressure is used in the packing room to prevent airborne contamination, Milne said. Designed with new food safety regulations in mind, crews use dry steam to clean the wet room lines between every shift and a sanitizing foam coats the wheels of forklifts that come in and out of the room.
Leave A Comment