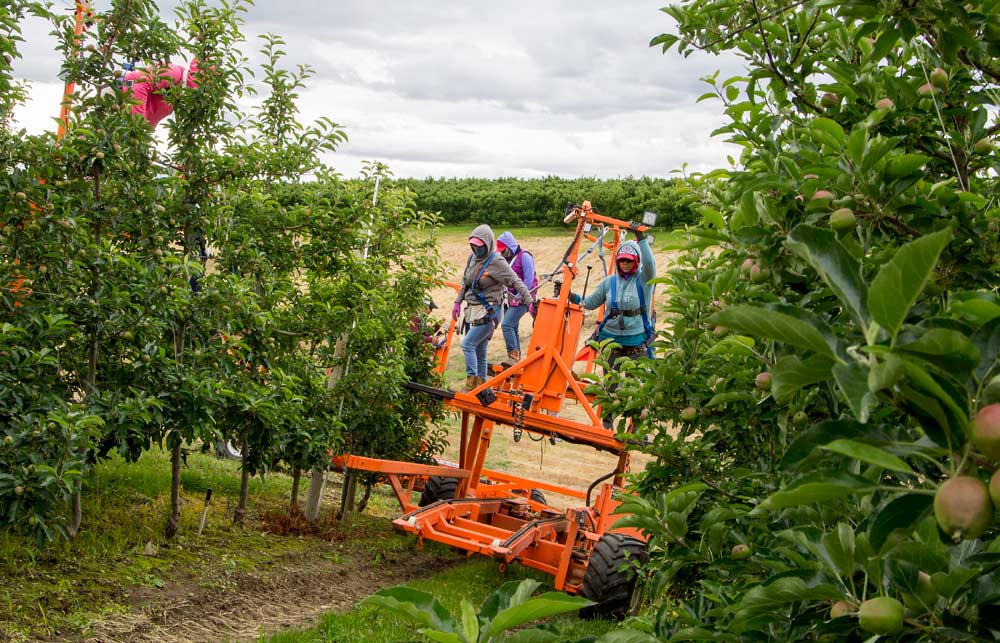
Workers on platforms thin apples and tie branches at a Kershaw Companies orchard in Zillah, Washington, in June. The goal is for a very controlled system with tied limbs and nothing that grows perpendicular to the row. (Shannon Dininny/Good Fruit Grower)
In today’s modern, high-density orchards, growers are constantly seeking new ways to match the biology of their trees with emerging technologies in mechanization. The goal: improve both yields and efficiency.
It’s true that some technologies don’t exist yet, but the compact, planar architectures with precision canopy management are most suitable for future mechanization and even for robotics, said Matthew Whiting, Washington State University research horticulturist.
“So it is kind of an exciting time for what will be a new era of tree fruit production, as more and more technologies become available,” he said.
Research labs and research orchards are driving new developments, but in many cases, they’re happening with innovative growers and private companies, he said.
“Growers are innovating with orchard systems and varieties and architectures, and that’s fueling university research in many cases, and conversely, universities are driving new genotypes and how to manage and grow them best,” Whiting said. “It’s all coming together as it has never before, and it is an exciting time.”
At the same time, employing the mechanization tools that already exist can take a variety of forms, across all four seasons.
Those platforms you’re using for harvest? You can use them for pruning, green thinning and training, too.
Two growers whose companies have been pushing forward with platforms, hedgers and other tools shared their insights for automating tasks in winter, spring, summer and fall with Good Fruit Grower.
For Rod Farrow, who farms 520 acres of apples at Lamont Fruit Farm in Waterport, New York, the emphasis has been to increase income with high-value varieties and to reach maximum potential income on his standard varieties, Honeycrisp, Fuji and Gala.
Almost everything is planted on Budagovsky 9 rootstock in 11-foot by 2-foot spacing, and he’s been planting and pruning to a fruiting wall for almost 18 years.
“It’s less about employing mechanization by season than about deciding the orchard system — as much as anything, making sure the system that you plant now is suitable for robot use,” he said. “If it’s not, you’re going to be in trouble in terms of how you can adapt that new technology, which is coming really fast.”
In the past two years, Farrow also has elected to install 3-foot taller posts in new plantings, allowing for a 2-foot taller system intended to increase production from 60 to 70 bins per acre to a more predictable 80-bin range.
“In terms of being competitive with the West Coast, I wondered if our original plan was going to work going forward,” he said. “We realized we might have to shift radically.”
On the West Coast, Dave Gleason is horticulturalist for Kershaw Fruit, a fifth-generation farming operation based in Naches, Washington. Older Gala blocks are plants at 16 by 8, yielding 85 bins to the acre. However, newer plantings are either spaced 11 by 3 on verticals or 12 by 2 on a V-trellis, and they’re designed to maximize mechanical aids and robotic harvesting.
Older plantings are another story, he said. “When you have existing structures that are profitable, it’s hard to look at transitioning those and making moves that take sections out of production for a while,” he said. “In our case, we started looking at hedging our blocks to make them more light efficient and more pedestrian friendly over time.”
Dormancy
In older systems, pruning was much more of an art form — how best to enable light penetration through the system. In newer, high-density plantings or fruiting walls where growers aim to employ mechanization, it’s more about setting the box — the principle of growing apples inside a defined space.
During the dormant season, Farrow mechanically hedges fruiting walls to branches to within 14 inches of the trunk. “It’s always the temptation when you get apples outside of there to keep them, but once you break the rules, you start to lose the concept,” he said.
He hedges just before the end of dormancy and, depending on the variety, begins to hedge the bottoms of trees in the third or fourth leaf. “Hedging is dependent on rootstock, variety and the natural vigor of your orchard. Don’t do it if it isn’t physiologically beneficial,” Farrow said.
In the Kershaw orchards, Gleason said pruning can actually be done all winter long. “We’ve found even in wider rows, we can get rid of ladders.” A mechanical hedger sets the box. Then, from mechanical-assist platforms, workers use long-handled loppers to reach the middle of the tree and remove older wood and detail prune. The workers are closer to their work and don’t spend time worrying about falling from ladders, he said.
“A huge part of any of these operations is the supervision that’s involved and the buy-in with people if they are not particularly excited about a particular tool,” Gleason said. “Even getting on a platform can be a challenge, but there’s huge savings that can be taken advantage of as long as everybody buys in.”
About five years ago, Kershaw Fruit compared the costs of using platforms to prune trees with the costs of using ladders and found that the company could pay for the at-that-time cost of a $35,000 platform in about four months.
“We’re also using less people and using people more effectively,” Gleason said. “We’ve been transitioning since then, in a change of degrees.” Now, the company’s pruning is about 98 percent ladder-free.
Spring
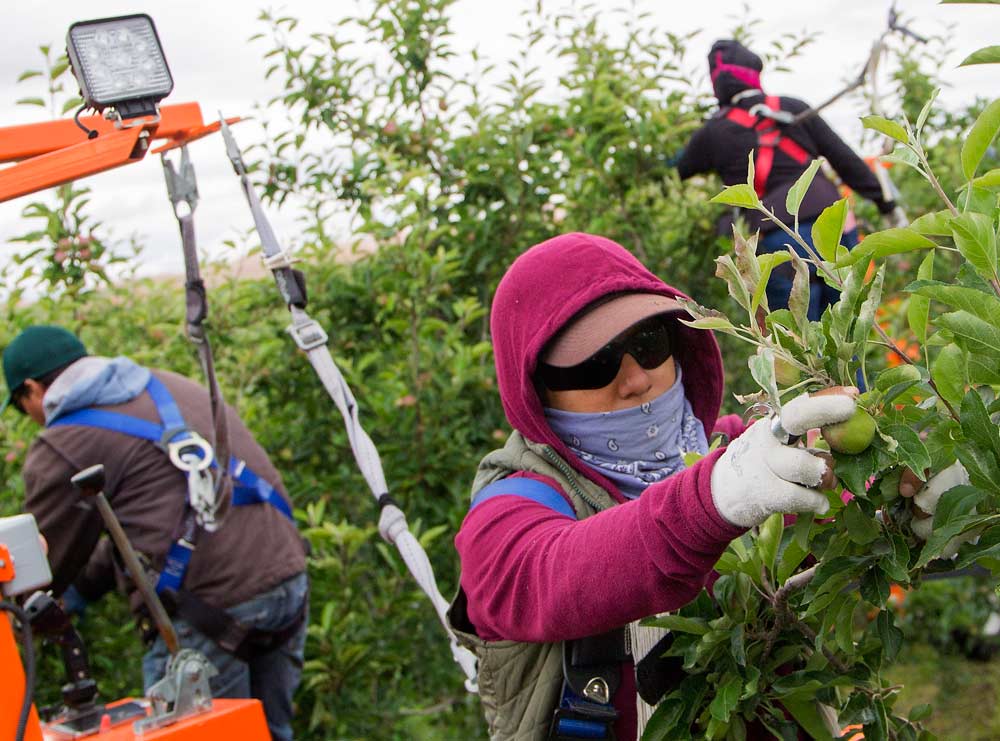
Platforms enable Kershaw Companies to hire workers with varying strength levels for tasks such as thinning, tying and harvesting. Here, workers thin apples and tie branches in a Zillah, Washington, orchard in June. (Shannon Dininny/Good Fruit Grower)
Farrow has been conducting a study of mechanical thinning with researchers from Cornell, out of concern that carbaryl — a key component in the chemical thinning regiment for growers in the Northeastern U.S. — could be removed from the market.
The three-year study on 1 acre of Gala and Honeycrisp showed that running a Darwin thinner at 180 to 200 rpm, along with two shots of MaxCel (benzyladenine) at 64 ounces per acre, compared favorably to the grower standard of chemically thinning alone.
He had hoped to expand the study to 20 acres this year — 10 acres of Honeycrisp and 10 acres of Galas — but temperatures were so low this spring, never getting out of the 50s (Fahrenheit) for 25 days straight, growers across New York were concerned no fruit would set.
“We were finally happy we had some great results in 2016, to the point where we were ready to take this to commercial-size trials, and we’ll continue again next year,” he said. “If we ever lose carbaryl, this could be a mainstay of our thinning program.”
More and more, growers are moving to nonselective operations, such as mechanical hedging, which involves no strategic decision on which limbs to keep, said Whiting of Washington State University. It’s an idea that runs counter to the past, where a decision was made about every single cut.
“Moving away from that will be interesting to me, to see how one would counter-play the nonselectiveness with a very precise system,” he said. “The overwhelming cost of harvest is growers’ top expense, but second is pruning. You could take this nonselective hedging approach — and many growers have — and gain great advantages from doing so.”
Summer and fall
In summer and fall, it’s all about platforms.
At Kershaw orchards, work from platforms continues in the summer, with training and green fruit thinning. “We’re aiming for very controlled systems, with tied limbs, and nothing that comes perpendicular to the row — or just grow them on wires like shelves,” Gleason said. And if workers don’t have a lot of one thing to do, the time saved not having to move ladders enables them to sometimes tackle more than one task at a time from the platform.
Farrow also has workers hand prune trees from platforms during summer, leaving two to four fruit buds and one to two apples per short, stiff limb of 14 inches or less.
Kershaw orchards harvests all of its 12-foot systems from platforms, with workers coming in at 3 a.m. to get off early. Lights provide an advantage when workers are color picking. “With the sun in their face, they can’t see. With good supervision, they can do an excellent job of color picking at night,” Gleason said.
Farrow said his workers pick 80 percent of his crop from the ground and only the remaining 20 percent from the platform.
The result: Everybody now picks 4.5 bins of stem-clipped Honeycrisp a day, where in the past they would pick 3.5 bins.
(He’s seen about the same percentage increase for nonstem-clipped, multiple pick varieties from 6.5 to eight bins a day).
“It moved the whole crew average, because now nobody has to move or climb a step ladder,” he said. “Most people would rather work on the ground, without the machine, that’s been our experience with our crew, and at the moment, we see no reason to try to pick every apple from a machine, which lowers the capital investment. We need one machine and not five.” •
– by Shannon Dininny
Thanks for the article featuring mechanization in the Orchard…do you plan on featuring any other manufactures besides the Automated Ag? So far most of the articles regarding mechanization have only featured one picking/work platform manufacturer, what about the other manufacturers like Blueline, N.Blosi and Orsi?
Hi Chris. Thanks for the comment. We don’t ever set out to focus on one piece of machinery or one manufacturer. In this case, these happened to be the pieces of equipment these growers were using. There are more stories to come on mechanization, so stay tuned!
The last three articles I have read have all featured the same manufacturer so it clearly appears you are focusing on one over the rest
Chris,
The article never mentioned the manufacturer!!??
Very interecting article, I am an Orchardist in Hawke’s Bay New Zealand. Is there any more info on platforms?types,manufacturers and costs would be helpful. Thanks