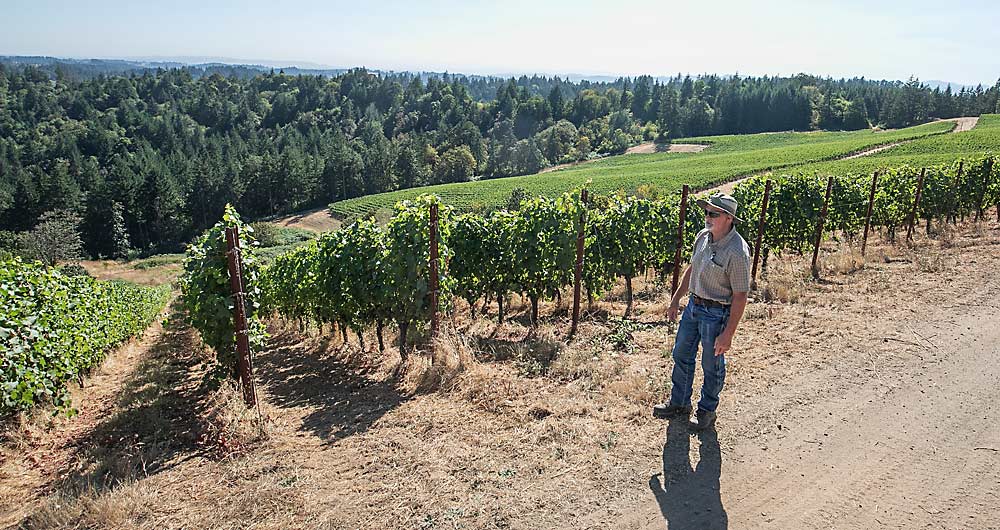
Achieving the perfect Pinot Noir block, with shoots positioned and leafed to create the picturesque wine-country visual expected by tourists in Oregon’s Willamette Valley, requires a lot of hand labor.
Four passes for shoot positioning. Three passes to move wires. Thinning. Leafing. And with increasing labor costs and new overtime regulations, even high-end vineyards can feel the squeeze.
Different price points have long had different farming expectations, said Daniel Fey, president of Results Partners, a vineyard management company with clients throughout Oregon and Washington.
That, of course, is spelled out in management contracts.
But as grape prices fail to keep pace with rising costs of production, growers who want to remain profitable have three options: reduce input costs, produce more fruit or find ways to market the grapes for more money. The first options may involve embracing new viticultural approaches for the region, and although his business is based on providing labor, Fey wants his customers, and others in the region, to know they have more options.
“It’s a customer-service business,” Fey said. “If you are not setting up someone for long-term success, you are not doing a good job.”
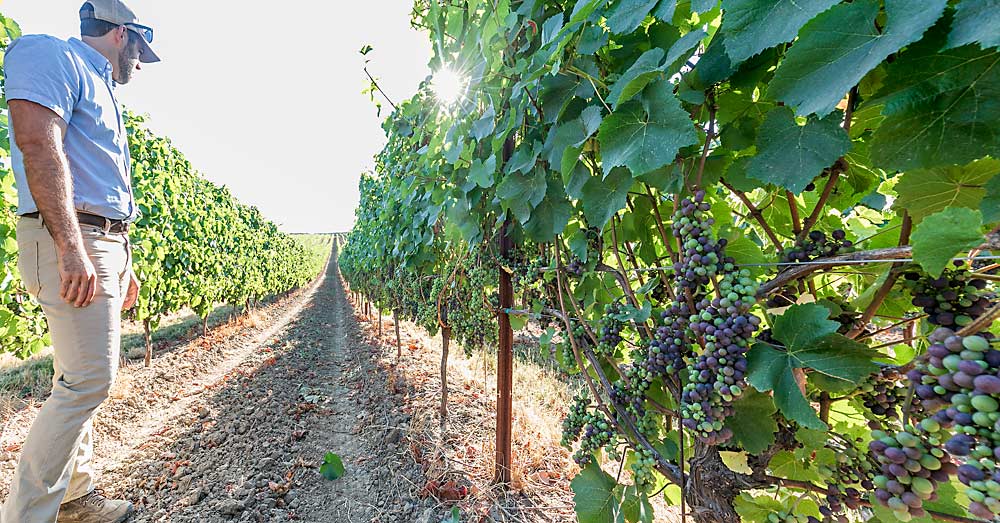
Good Fruit Grower visited several vineyards in the Willamette Valley, located on Oregon’s historically verdant west side, to see some innovative approaches for profitability amid labor challenges.
Finding efficiencies
While production vineyards often embrace mechanization for hedging and harvest, that’s nigh impossible on the steep slopes, patchwork plantings and narrow rows at many vineyards in the region.
Take Fairsing Vineyard, for example. This 42-acre vineyard in Yamhill, the hill country southwest of Portland, features scenic, steep and meticulously managed rows — designed in an era when labor was cheaper and more available — and offers no economies of scale. The vineyard would be nearly impossible to mechanize.
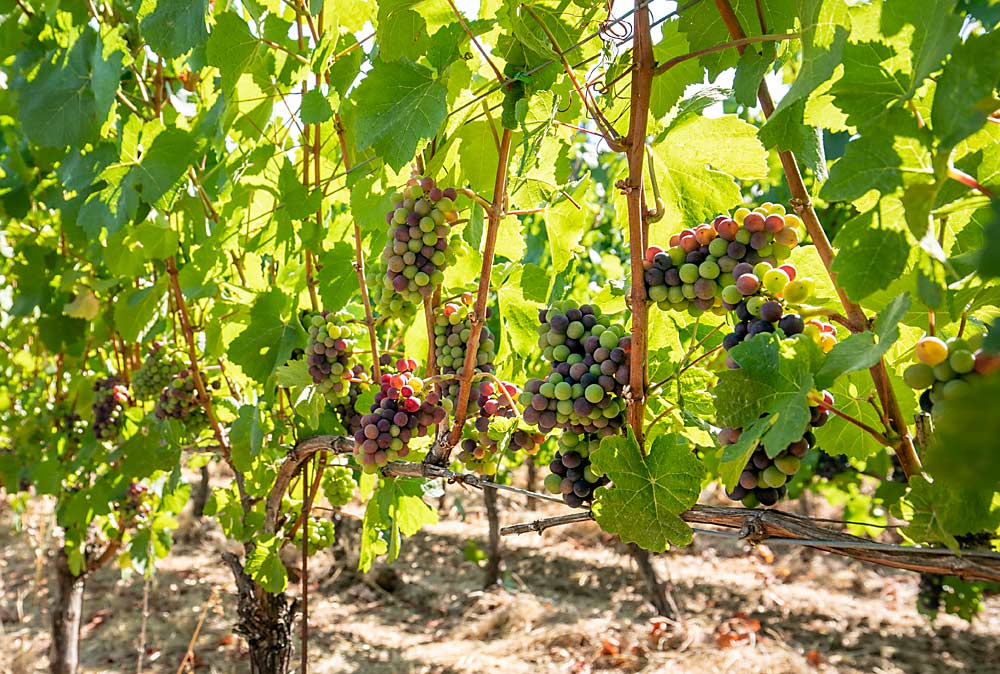
“The view is spectacular, but the farming is a challenge,” Fey said. He estimates his farming costs there at $9,000 per acre.
Fairsing’s Pinot Noir prices justify those costs, he added. But for others facing shrinking margins, Fey points out how a few changes in vineyard design can help to reduce those costs.
Just down the hill from Fairsing sits 32-acre Saffron Fields Vineyard, another that Fey manages. It’s planted at a lower density — 8 by 5 feet — which translates to half the vines per acre while hanging a similar crop of 3.5 tons per acre of Pinot Noir. That spacing reduces the amount of canopy management needed and gives more space for flexibility.
The vineyard design also took advantage of the terrain to plant longer rows for more efficient mowing, spraying and hedging.
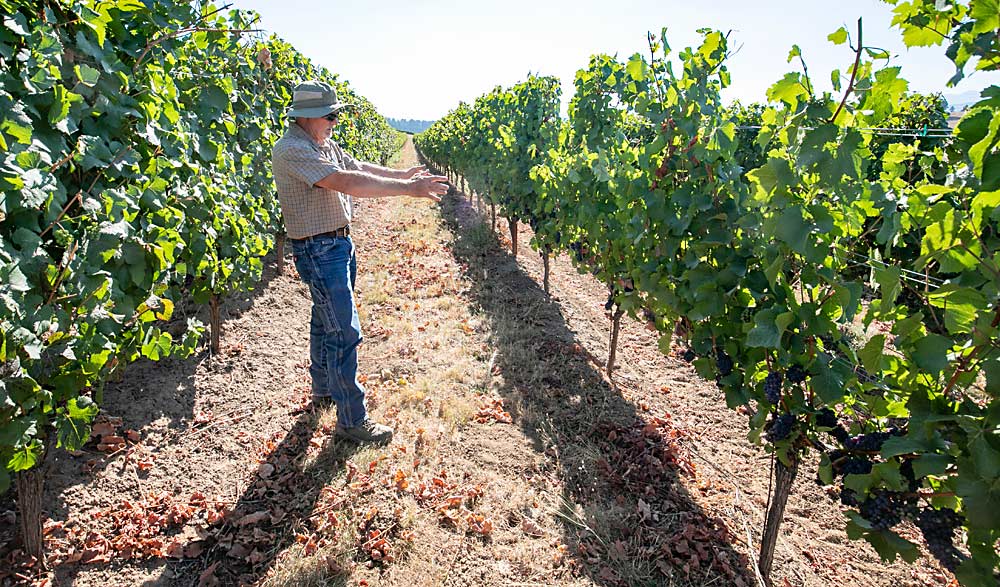
Fey estimates the farming cost in such a setup at $7,500 an acre, and the vineyard design offers more options to mechanize in the future, if desired. He recommends planting new vineyards with that eye toward efficiency and flexibility.
But at existing vineyards, some owners are finding ways to boost production to balance out rising labor costs.
At Maverick Vineyard near Carlton, the owner opted to transition from a typical vertical shoot positioned system, planted at 9 by 6 feet, to a Scott Henry system, which employs two tiers of canes that send fruiting shoots up and down. In one block that just made the system switch last year, Fey estimated the crop load at 4.5 or 5 tons of Pinot Noir, with farming costs around $7,500 per acre.
“Yield is going up, but you are not spending a lot more farming it per acre,” he said. “The owner here is a famous winemaker who wants quality at a price point that makes sense for him.”
Outside the box
Alex Cabrera, Results Partners’ director of vineyard operations, took Good Fruit Grower around two vineyards where management approaches fall further outside the box of the region’s traditional viticulture.
At SeaBreeze Vineyard near Perrydale, the owners replanted many blocks over the past decade to an 8- by 5-foot spacing that allows “more wiggle room for tractor drivers and for different canopy approaches,” Cabrera said. He sees the 5-foot, in-row spacing as the “Goldilocks.”
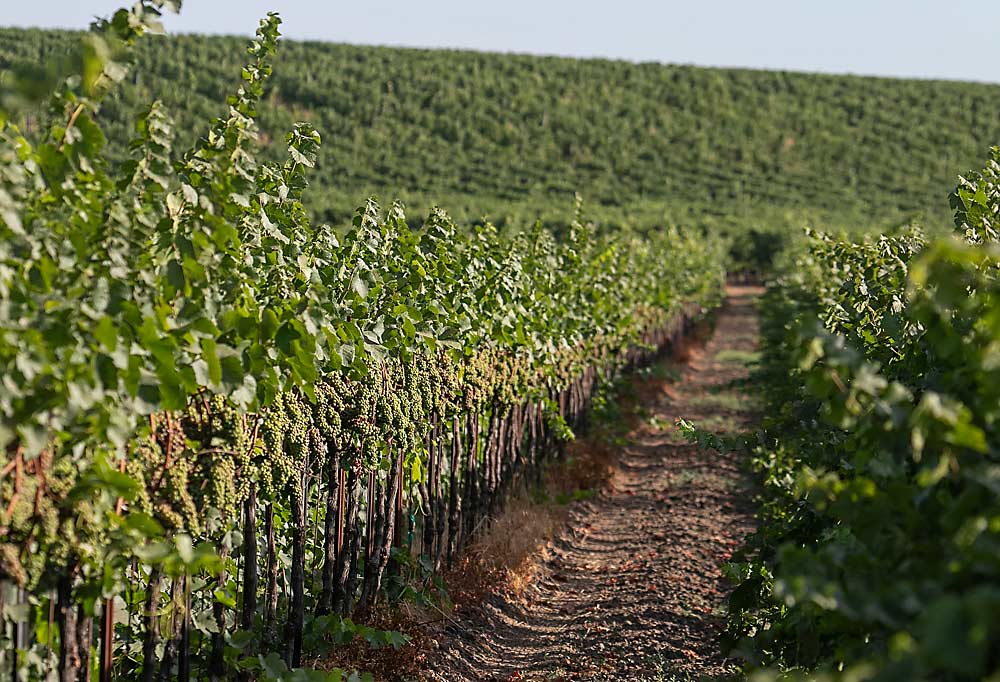
Most of the 214-acre vineyard is trained to the standard VSP, but Cabrera has deployed several variations to reduce labor demand. One approach is what he calls a hybrid flop, which uses one pass to tuck shoots into a fixed wire set in a 12-inch crossarm, about 18 inches above the high fruiting wire. A second pass pushes the growing shoots to sprawl over the west side, which provides protection from afternoon sun.
The Pinot Gris block, hanging 5 to 6 tons per acre, delivers a consistent, uniformly light-exposed fruit zone with a lot less work. The block is highly mechanized.
Cabrera adapted several Pinot Noir blocks by adding two extra canes, either by braiding two canes together or by spacing them on separate wires in what’s known as a double up or quad up system. He prefers the latter.
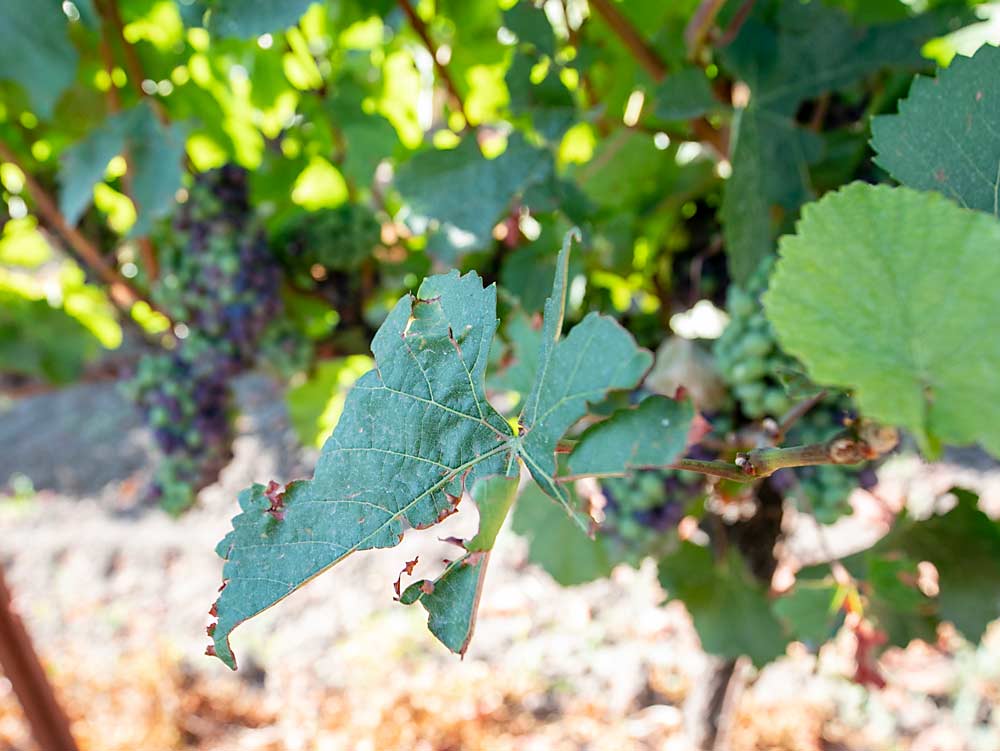
It almost doubled production, to 5 tons per acre, and while it does somewhat increase the need for pruning and shoot thinning, the shoot positioning and leaf pulling are similar to a standard single-cane system.
“We’re not doubling the labor input, but we are almost doubling fruit production,” he said.
For a new planting at SeaBreeze, Cabrera is taking the low-labor-input idea even further. His low-input VSP system features all fixed wires, held with 8-inch-wide clips, creating a larger space for the canopy. The system supports fewer and more widely spaced fruit positions. Tucking the shoots into the wires as they grow, rather than lifting wires, requires fewer passes, he said. He envisions it will need little to no shoot positioning.
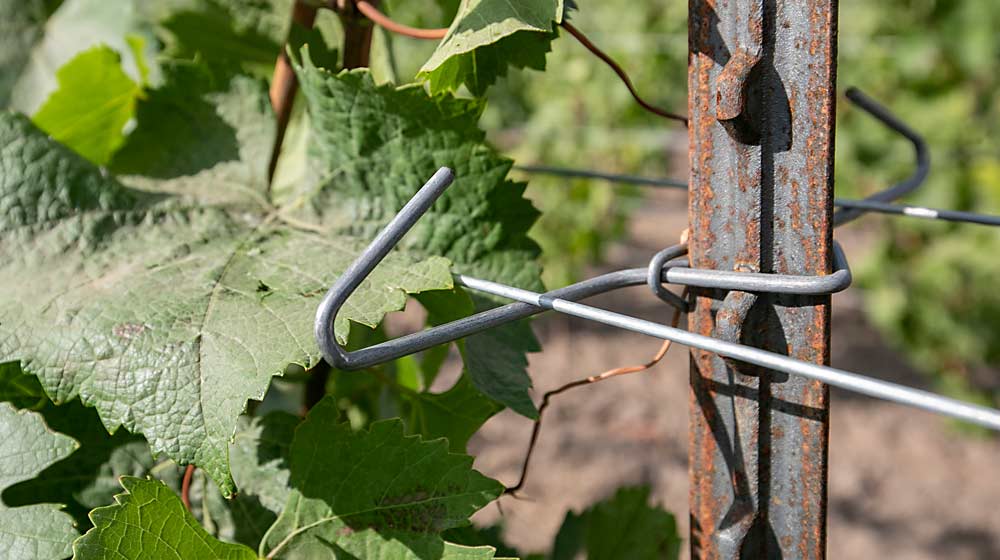
“Will everything look perfect with everything going straight up in the air? No, and that’s not what we want here,” he said. “It needs little manual input and reduces congestion.”
The block also features a beefed-up trellis with oil-field end posts and hefty T-posts to support a larger canopy, higher crop loads and more mechanization.
At nearby Huntington Hill Vineyard, a newly planted block features a highly engineered trellis system that will eventually be managed with a Klima brush removal machine developed in New Zealand. As it moves down the row, the machine unclips wires from posts, strips off and mulches all the previous season’s growth, and then replaces the wires. Only the renewal canes below will remain, ready to be trained onto the clean wires the next season, Cabrera said.
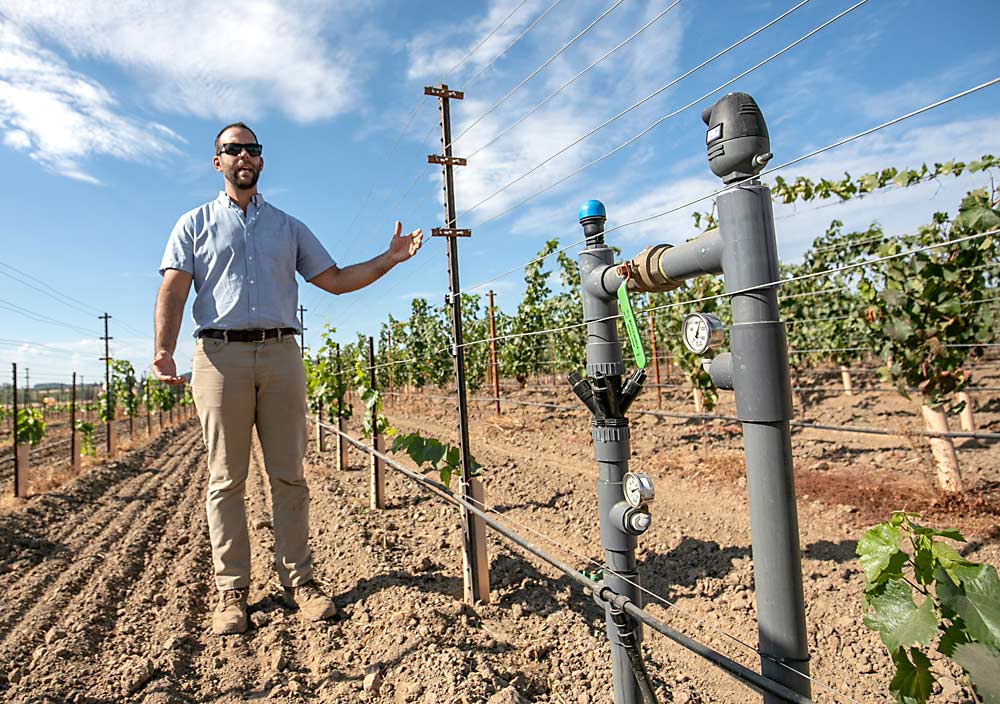
Designing for that specialized equipment, rather than retrofitting, is “the way to get the best bang for your buck from new equipment like this,” he said.
Canopy management will be done with his fixed-wire, shoot-tucking, low-input VSP approach. And it features another Willamette novelty: irrigation.
“If we want a higher crop, the limiting factors are heat units and water,” Cabrera said. He sees irrigation as an insurance policy for the overall investment in the vineyard.
—by Kate Prengaman
Leave A Comment