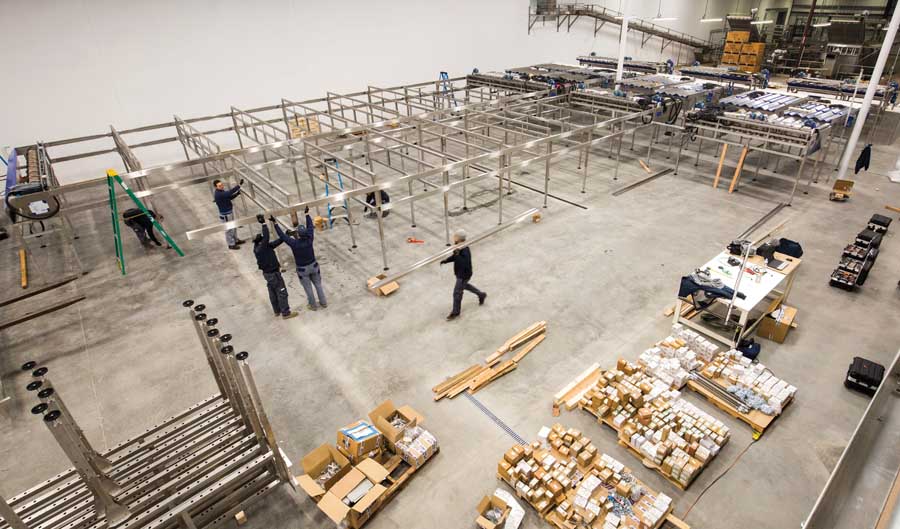
Workers install a cherry processing line that will feature optical equipment to sort fruit at The Dalles Fruit Co. in Dallesport, Washington, on January 13, 2016. (TJ Mullinax/Good Fruit Grower)
When the first of the Columbia Gorge’s sweet cherries come off the trees, Mt. Adams Orchards Corp., will begin using its new packing equipment in Dallesport, Washington.
Their neighbors across the Columbia River — Orchard View in The Dalles, Oregon — will do the same.
Both cherry companies have invested millions of dollars in 48 lanes each equipped with optical equipment that uses near-infrared technology to sort fruit by size, firmness, color and defect.
The gear, once a new technology that gave a packing house an advantage, is now becoming expected by buyers.
“It’s a new set of standards,” said Don Gibson, president of Mt. Adams.
Other packing houses in the Northwest are using sorters from other manufacturers this year, following the lead of still other companies that made similar investments over the past four or five years, Gibson said.
The two companies are the two largest packers in the Columbia Gorge, competing with packers in and around Yakima, Washington, for fruit grown in the area. Even at full capacity, the two packers could not pack all the cherries grown in the Gorge, Gibson said, though he declined to speculate a market share.
The Dalles Fruit Co., a packing subsidiary of the Mt. Adams ownership group, has invested tens of millions of dollars over the past four years to expand the facility to a total of 64 lanes of near-infrared optical sorting, Gibson said.
Mt. Adams formed The Dalles Fruit Co. in 2008 and completed the packing house in 2009, expanding in 2010 and 2014.
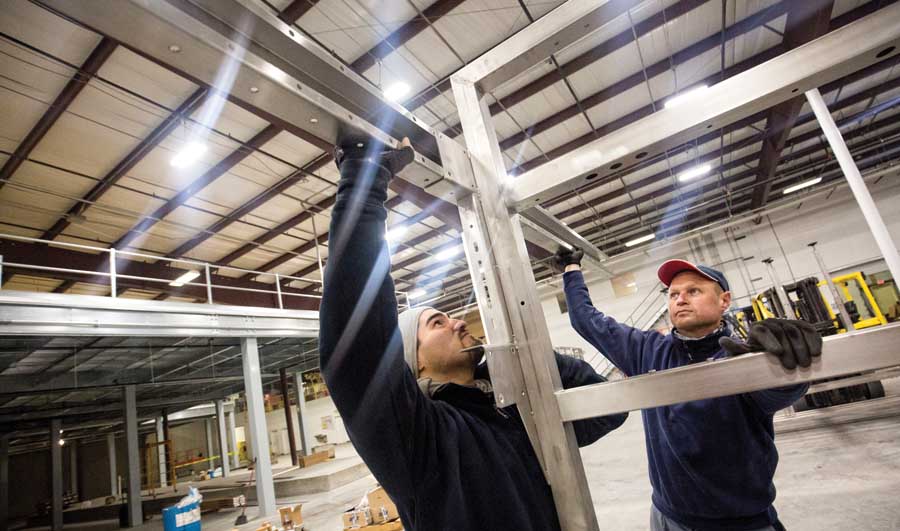
Arnulfo Valdez, left, and Vasile Gado work on the installation at The Dalles Fruit Co. The upgrades will expand capacity to 600 tons per day. (TJ Mullinax/Good Fruit Grower)
The 2014 expansion added 16 lanes of optical sorting. The latest round added 48 more, making the facility one of the largest to use the sorting technology in the Northwest.
The additional lanes should increase the plant’s capacity by 50 percent to 600 tons per day, Gibson said. At times, The Dalles Fruit Co. receives 550 tons of cherries per day.
“We have growers that have grown and we’re growing with them,” Gibson said.
The latest improvements are scheduled to be ready for operation in time for the 2016 cherry season.
Mt. Adams also packs apples and pears at its facilities in Bingen and uses the Dallesport buildings for cold storage for pears and apples.
In The Dalles, Orchard View added the equipment to create packing consistency, better packouts and higher returns for all of its varieties, said Brenda Thomas, company president.
“I believe it’s going to create a more consistent quality box of cherries,” she said.
The facility also includes a new water treatment system to cut down on the use of fungicides and a new post-packing rapid cooling system, she said.
“It’s the largest (monetary) investment we’ve ever made,” Thomas said.
Previously, the firm ran its Rainiers through a Red Pearl sorter and its dark sweets down a conventional, mechanical and hand-sorting line, she said.
The extra capacity also will come in handy on days when the company suddenly needs higher throughput to keep up with picking ahead of rain, she said. In the past, supervisors would have had to scramble to call in extra workers. •
– by Ross Courtney
Leave A Comment