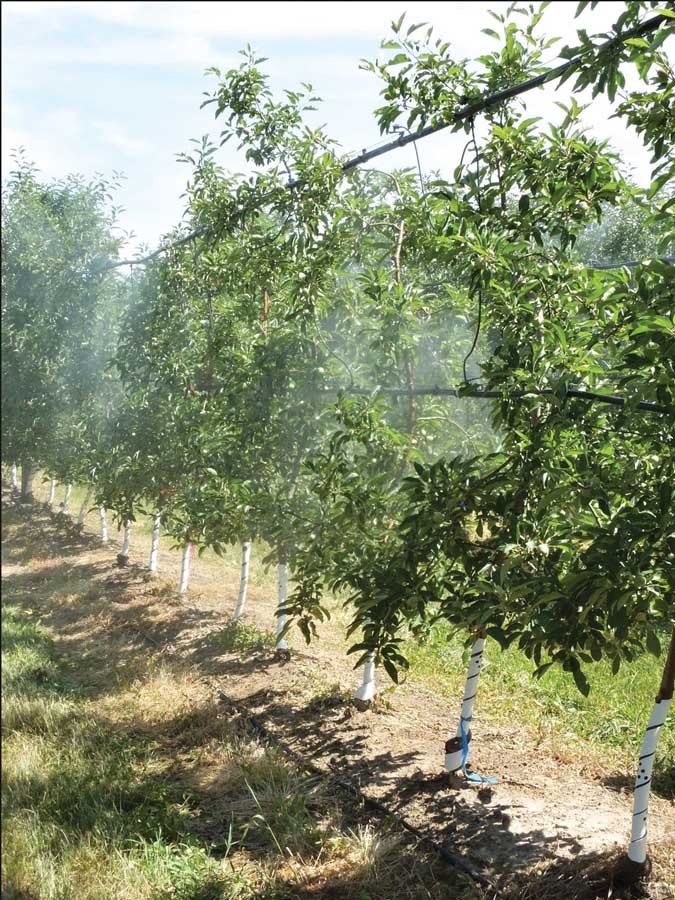
A Michigan State University research team is working on an improvement to its solid-set canopy delivery system (SSCDS), which will not only spray crops quickly, but may cut back on pesticide and other spray volumes. (Leslie Mertz/for Good Fruit Grower)
A Michigan State University research team demonstrated new progress on an innovative solid-set canopy delivery system (SSCDS) that the team believes could drastically cut the volume of pesticides and other sprays needed for orchards, vineyards and other crops.
This research builds on earlier SSCDS work that shows such a system increases the speed of application, distances workers from the application, and keeps tractors or other rolling spray-applying equipment out of tree and vine rows.
The demonstration was part of the MSU Clarksville Research Center Field Day held in southern Michigan on June 22.
Basically, the system consists of tubing running between and connecting to a series of microsprayers. A hydraulic pump and an air compressor are used to supply agrichemicals to the microsprayers and discharge the agrichemicals as a mist.
The research team developed and then tested the feasibility of the system from 2012-2014 and showed that the SSCDS got similar pest management results to those yielded by a traditional air-blast system (Read “A new way to apply chemicals” in the June issue of Good Fruit Grower).
“The basic concept for the delivery of agrichemicals is that, instead of using a tractor-based sprayer that you have to pull through the orchard, we distribute microsprayers throughout the canopy, and those microsprayers are fed by a pumping station that combines both a hydraulic and a pneumatic delivery system,” said Matthew Grieshop, the project director and associate professor at the MSU Entomology Department.
One major challenge remained: chemical waste. The chemicals cleared from the 500-foot-long tube system after spraying amounted to about 2 gallons, and the team wanted to reduce that amount.
With critical input from irrigation expert John Nye at Trickl-eez Irrigation, the team began considering the benefits of a canister-vent system, and last fall, it invited a group of five mechanical engineering students from Michigan State to make a run at the problem.
Within five short weeks, the students had a working prototype. Grieshop reported, “With the testing we did this winter, we had only about a cup and a half of residual fluid that came out of the bottom line, so we had about an 80 percent reduction in volume.”
At the center of the students’ prototype is a reservoir designed to release a fixed amount of liquid chemical. (A video of the SSCDS prototype in action is available at www.canopydelivery.msu.edu.)
Each reservoir is a small canister with a carburetor float-type mechanism.
The reservoir connects to a feed line on the bottom and an air line on the top.
When the pump is on and liquid chemical begins coursing along the lower feed line, it enters the first reservoir in the series.
As liquid fills from the bottom, a pingpong ball in the reservoir rises with the liquid, and when it reaches the top, it seals the reservoir.
The liquid continues along the tube to fill the next reservoir, and so on, until all reservoirs are filled. The air compressor then takes over and provides sufficient pressure to force the liquid from the canisters and through spaghetti tubing to microsprayers placed throughout the canopy.
“Our initial SSCDS design meant that you ended up having to pump many hundreds of gallons of liquid into your feeder lines to get the liquid where it needed to be to spray, but this new design does away with that essentially,” Grieshop said.
Grieshop and the SSCDS team are now working with AgroLiquid of St. Johns, Michigan, to test the system for foliar application of pesticides and nutrients, as well as other researchers who are evaluating it for distributing pheromones or other sprays.
They also are hoping to fine-tune the system, including the nozzles in the microsprayers, and look into commercialization.
“We’re really excited and we’ve got our fingers crossed that we’ll get some funding and move this project into more of a production phase,” he said. “There are just so many possibilities.” •
– by Leslie Mertz, Ph.D., a freelance writer based in Gaylord, Michigan.
Leave A Comment