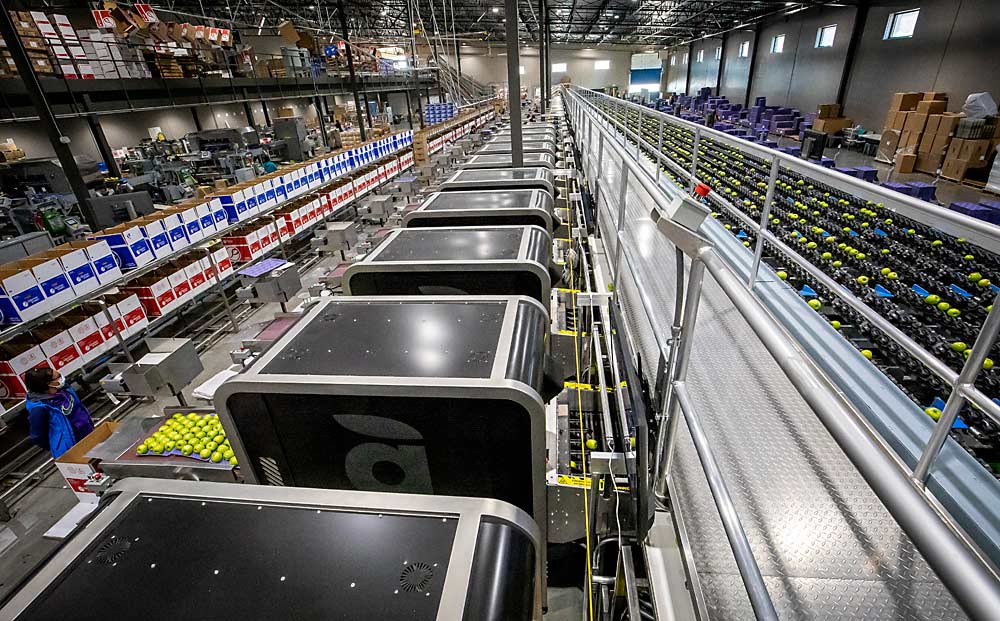
Fewer people on the packing line makes social distancing easier.
That’s what Hayden Dooney, general manager of the Norfolk Fruit Growers’ Association, learned from the coronavirus pandemic. The Simcoe, Ontario, company had been planning to upgrade its packing facility with a robotic arm that lifts bagged apples into shipping boxes sometime in the coming years. The coronavirus pandemic convinced the company to pull the trigger a little early.
The new equipment helped spread out workers, for sure, said Dooney, also a grower. But the biggest benefit was existential. When the pandemic first struck, about 40 percent of the company’s workforce chose to self-isolate, Dooney said. They installed the equipment just so they could keep up production and shipping.
Packers throughout the United States have been erecting barriers and creating distance between employees for worker safety during the pandemic. While robotic and automated equipment has been making its way to fruit packing lines for several years, usually in the name of efficiency and food safety, the coronavirus pandemic just provided executives and managers another reason to sing its praises.
“We’re trying to automate, too,” said Dale Davis, projects manager at Chelan Fruit in Chelan, Washington. “COVID is giving us another reason why.”
Chelan Fruit’s main packing line was built in 2016, replacing one destroyed by fire, with a variety of automated elements. For example, the company installed two robotic palletizers, arms that stack boxes on pallets, Davis said. Cost savings drove the decision, Davis said. Before the new palletizers, four to 10 employees worked in the area stacking boxes. Now, that’s down to two.
The company had palletizing equipment before the fire but upgraded afterward. The newer ones are more efficient, Davis said.
CPC International offers a similar story.
In the spring of 2019, almost a year before the pandemic, the Tieton, Washington, company completed a major overhaul with high-speed sizers, defect sorters, automatic baggers and automated palletizers purely for business reasons, said Gary Gredvig, production manager.
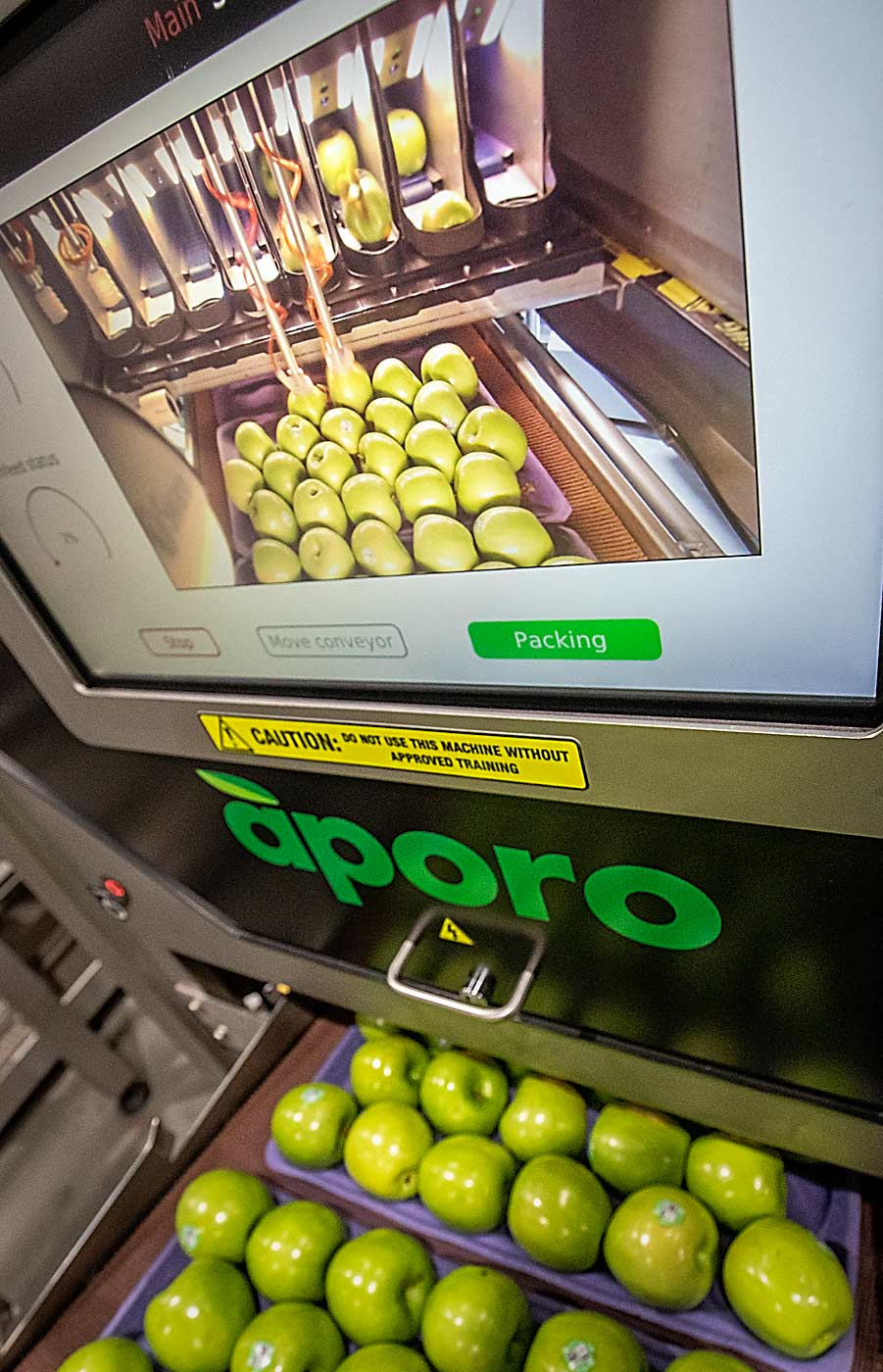
However, the modifications have given the company the ability to spread out people, Gredvig said. They are taking advantage of that ability because “our priority No. 1 is to keep people safe.”
Back in Ontario, Norfolk Fruit Growers first introduced automatic tray-fillers two years ago when a nearby bakery and egg equipment producer asked if they would try out a prototype. Dooney ended up purchasing about four of the machines.
This year, Norfolk Fruit began working with bag stackers as the next logical step, Dooney said. The $250,000 machine lifts and stacks about 25 bags per minute, a job that takes a physical toll on the body and saw a lot of turnover.
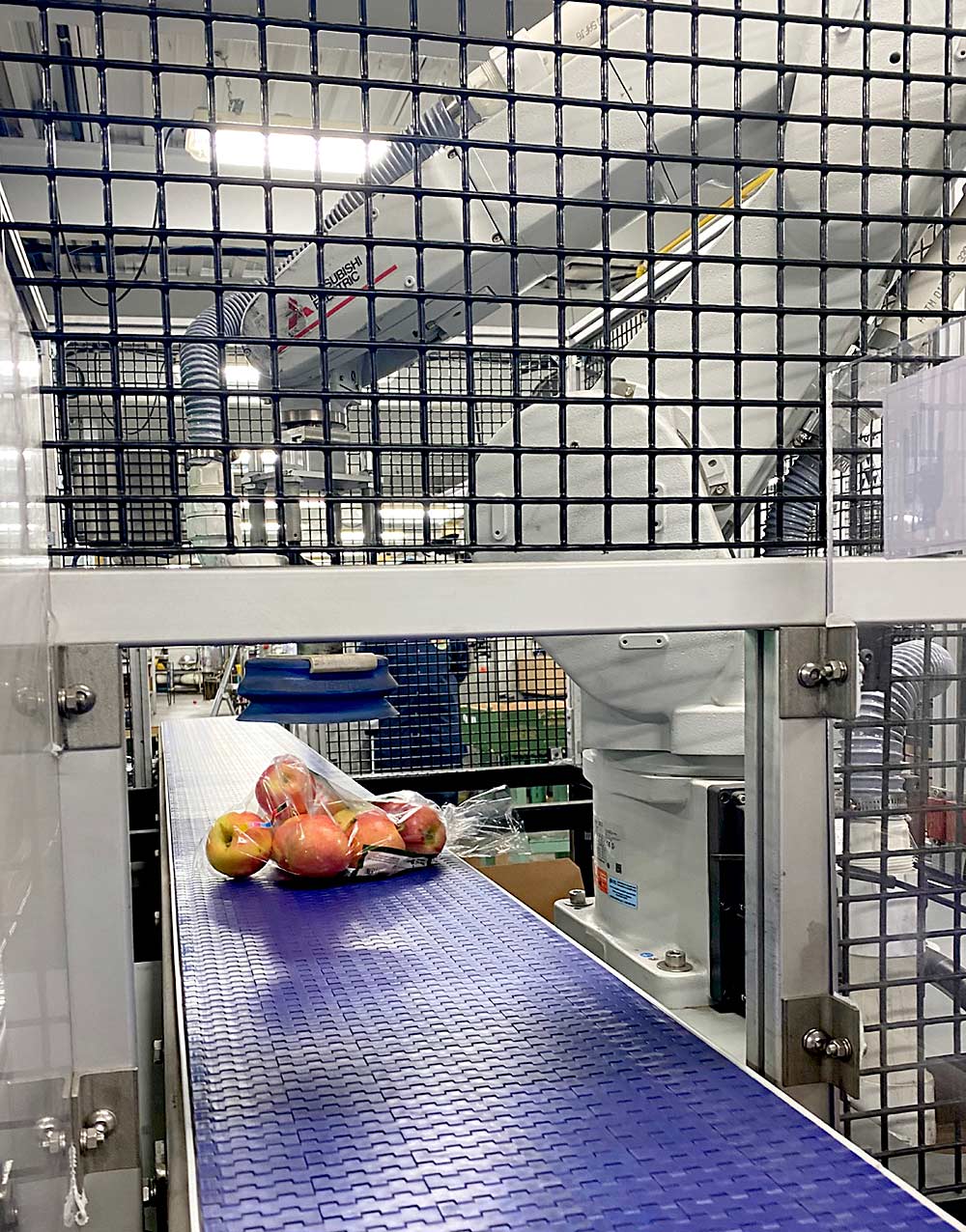
The coronavirus just bumped up the schedule by about a year, Dooney said. Today, the bagging area is staffed by only one person, compared to anywhere from two to six before the installation.
Dooney suspects automation will continue, especially on the orchard side.
“I think it’s going to be at an even higher pace in the field,” he said. •
—by Ross Courtney
Leave A Comment