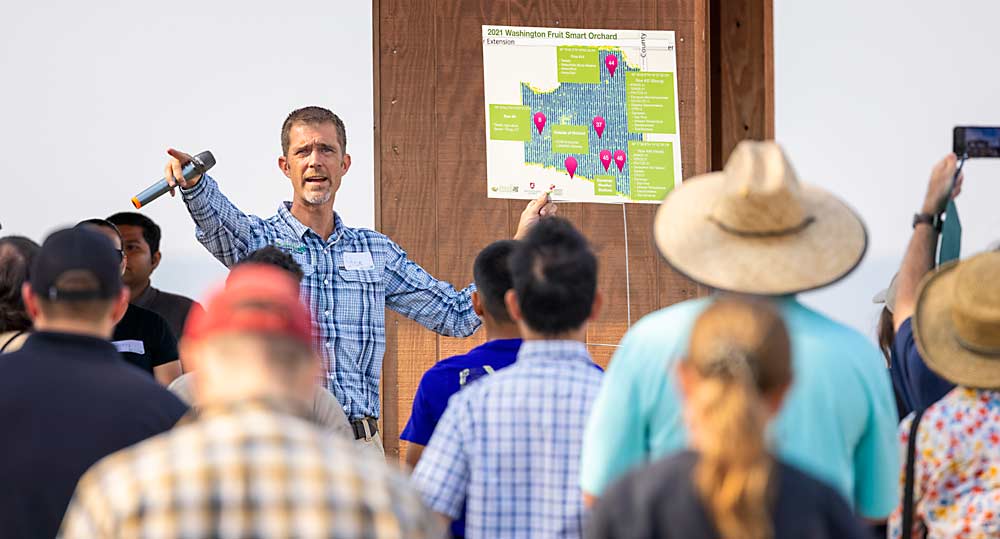
What makes the Smart Orchard smart? Is it the number of high-tech tools deployed to track water needs and fruit growth or map variability, the research to discover which offer information that improves fruit quality or yield, or the analytics to integrate all that disparate data into one management model?
The team behind the Smart Orchard project, a Washington Tree Fruit Research Commission-funded effort involving Washington State University scientists and tech companies, hopes the answer will be all of the above.
“We heard loud and clear from the industry that this is the way to go,” said Ines Hanrahan, director of the research commission, which put $115,000 toward the effort so far. Already, other specialty crop groups, including wine grapes and blueberries, have reached out about expanding the approach.
Now in its second year, the collaboration is hosted at two commercial orchard sites. The team conducted its first field day in July to introduce the approach to the industry.
There’s still a lot of data to crunch, but the team is closer to figuring out how to use imagery and sensor data to improve orchard management, said Steve Mantle, founder of Walla Walla-based ag data company innov8.ag and the facilitator of the Smart Orchard.
His company is developing a data integration platform and making the business case for some of the technologies it provides as a service, while scientists from WSU are studying a wide array of sensors in the same blocks.
“The advantage of this is there are several different groups of scientists coming together to test different approaches to look at the plant responses to the environment,” said Lee Kalcsits, the endowed chair for environmental physiology at WSU who is conducting research into plant-based water stress sensors at the Smart Orchard sites. “It also provides a nice test bed for products the industry might be interested in.”
In 2021, participating tech companies included: Aker Technologies, a drone imaging company; Arable, which offers climate and plant sensors; Ceres Imaging, an aerial imagery provider; Dynamax, which offers sap flow sensors and other plant and environmental sensors; and Thingy IoT, which set up connectivity networks and soil and climate sensors. Washington State University scientists also installed climate and plant water-use sensors and conducted drone-based imagery, while innov8.ag’s team brought soil- and canopy-mapping technology from SoilOptix and Green Atlas.
The project has an open door for tech companies, said Hanrahan, provided they are willing to collaborate with researchers and share their raw data.
Participating makes sense because tech integration is the way of the future for precision irrigation, said John Bourne, the vice president of marketing at Ceres. An aerial imaging provider that growers have long used to track weak spots or plugged emitters, Ceres recently released a new approach with plant-level insights that combines artificial intelligence with imaging to offer growers more data — and help the company compete in the increasingly crowded precision irrigation space.
“It’s not more data, it’s smarter data,” Bourne said. “It’s not just: ‘Here’s a map, what do I do with it?’ Here’s a map of how many trees are stressed more than last week.”
Ceres also shares its data with the WSU scientists developing image analysis algorithms, said Lav Khot, WSU ag engineer and AgWeatherNet director. Eventually, he thinks the tools his team develops with higher resolution drone data to model orchard microclimates and water demand could be run on the aerial images Ceres collects as well — making the approach more accessible to growers.
More broadly, having the Smart Orchard team act as the test bed for many emerging technologies should save growers some headaches, Khot said. For example, many sensors installed in the Smart Orchard can work with a common data interface, while others do not, creating data integration hurdles.
“The good thing, of course, for the growers, is they are not buying sensors and taking those failures, like they did with drones in the past,” Khot said. “So, growers are not buying a $3,000 weather station that doesn’t talk to the interface they want to use.”
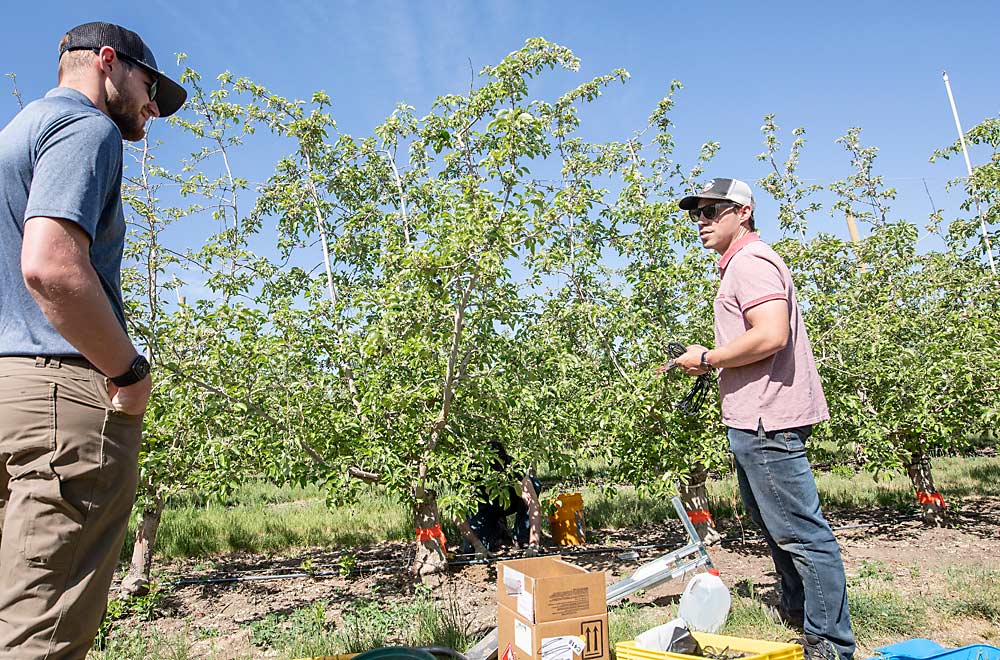
Location, location
The Smart Orchard started in a Gala block owned by Chiawana Orchards outside Pasco, Washington, in 2020. For the project’s second site, added in 2021, the Smart Orchard team wanted more variability, which is key to assessing sensors’ capabilities, Kalcsits said.
They found it in a Honeycrisp block in the Yakima Valley that’s owned by Washington Fruit and Produce.
“It’s a challenging site on this slope, hopefully that offers more variability to test these sensors out,” said Gilbert Plath of Washington Fruit. He also sits on the research commission’s tech committee and volunteered the orchard site. The company hopes the project will help to tie all the sensors together, so instead of having 12 apps on a phone or 20 tabs on a computer, “we can extract more data and get more value,” he said.
To make the case for value, the team is taking what Mantle calls a “yield-centric approach.”
“Last year, we came to the realization that we really need to have yield measurement throughout an orchard block so we could come closer to cause and effect,” he said.
He turned to crop load mapping technology from Australian tech company Green Atlas. With a camera system mounted onto an ATV, the system created a map of bloom density in April that the team then used to define different productivity zones and strategically target sensors in those zones.
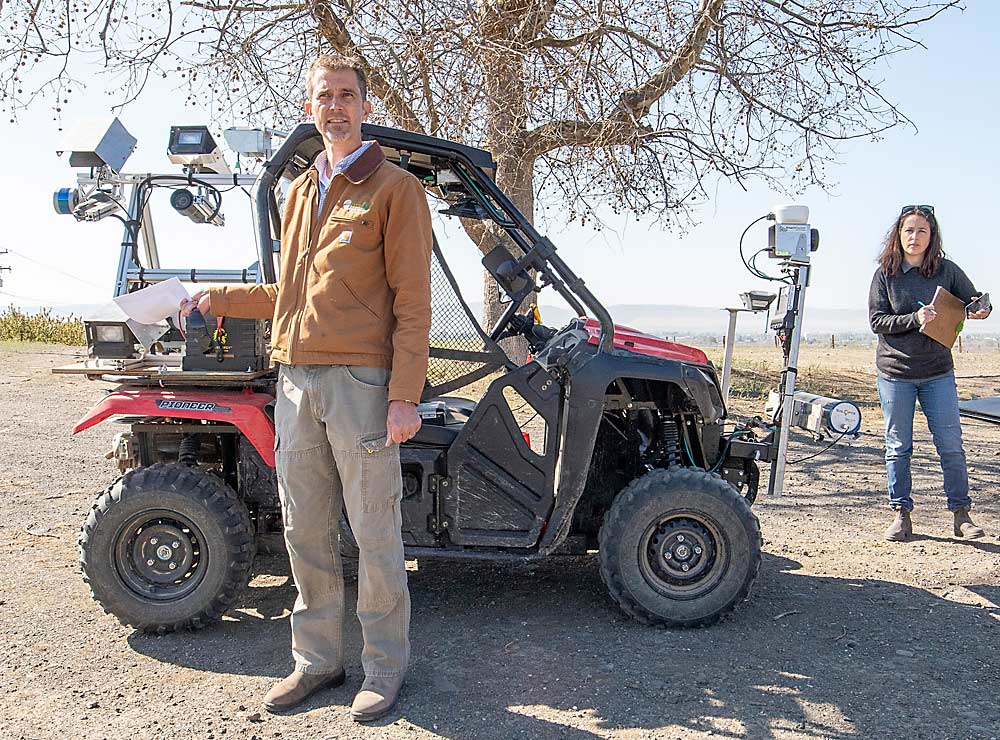
They repeat the spatial mapping throughout the season, examining fruit load and growth, along with canopy volume data collected by lidar sensors developed for smart spraying. Innov8.ag offers this approach to clients, but it’s also a foundation of the Smart Orchard efforts, Mantle said. The maps translate what other sensors can record at a specific point — soil moisture, microclimate, fruit growth — and extrapolate that to orchard zones that can be managed based on insights from the imaging.
Similarly, Mantle also uses a soil sensor, mounted to the front of the same ATV, to map soil composition and nutrient levels. He found significant variability in the sloping Washington Fruit orchard, which might have been missed by just randomly collecting two soil samples for lab testing.
The points where those various maps overlap with areas of low production offer actionable insights, and ultimately value, to growers, he said.
Data to dollars
The sensors also must be ground-truthed with traditional soil sample testing, for example, and preharvest yield maps compared with harvest data and, eventually, with fruit quality and packout.
“None of these sensors make any sense if we are not able to correlate to something that makes sense to the growers,” said WSU extension specialist Bernardita Sallato.
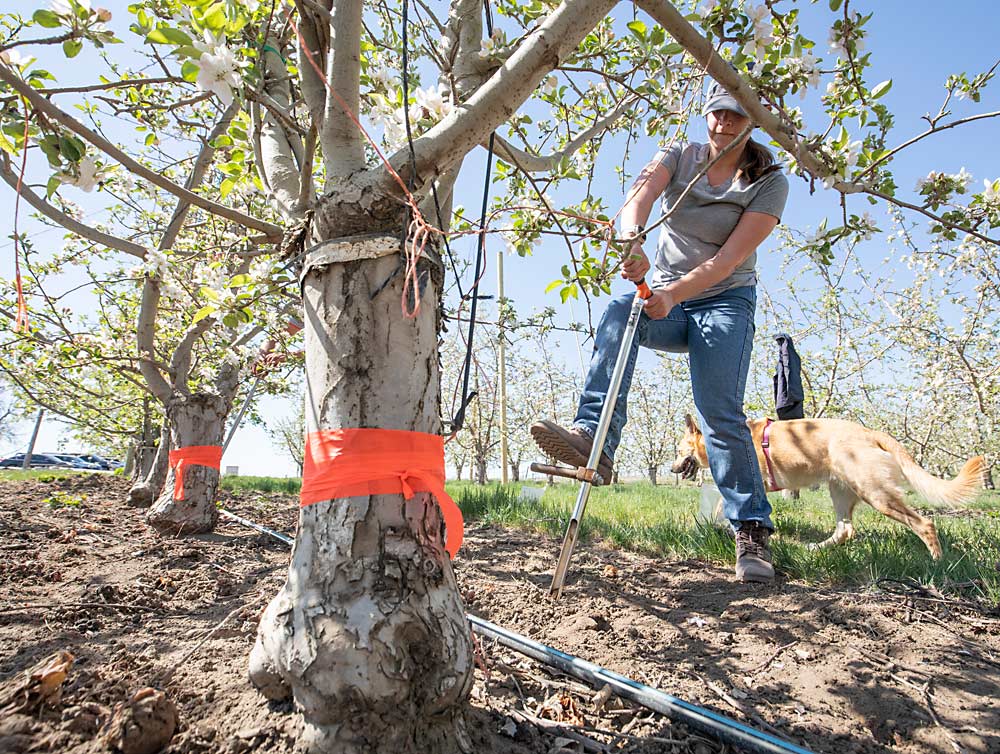
Those challenges mark the critical next phase of the project, Khot said: translating findings from sensor tests to management recommendations. And it’s easier said than done.
“From an extension point of view, I hope we are not confusing people,” he said, referring to the sheer volume of sensors, many redundant. “We are trying to put so many sensors in the field for research without telling people how they are going to use them for irrigation management or crop load management, yet.”
Integrating the data from imagery and weather data — Khot’s arena — with soil data from Sallato’s research and precision irrigation data from Kalcsits’ research, along with crop load data, should show which types of sensor data can inform better orchard operations and which fail to deliver a return on investment.
Meanwhile, Mantle said he sees a clear case to be made to growers with how the mapping approaches can reveal underperforming zones.
“What’s the packout if every tree in the block was performing optimally versus the percent of trees not achieving that optimal fruit load?” he said. “That’s the unrealized potential per block.”
—by Kate Prengaman
Dealing with ZeroG
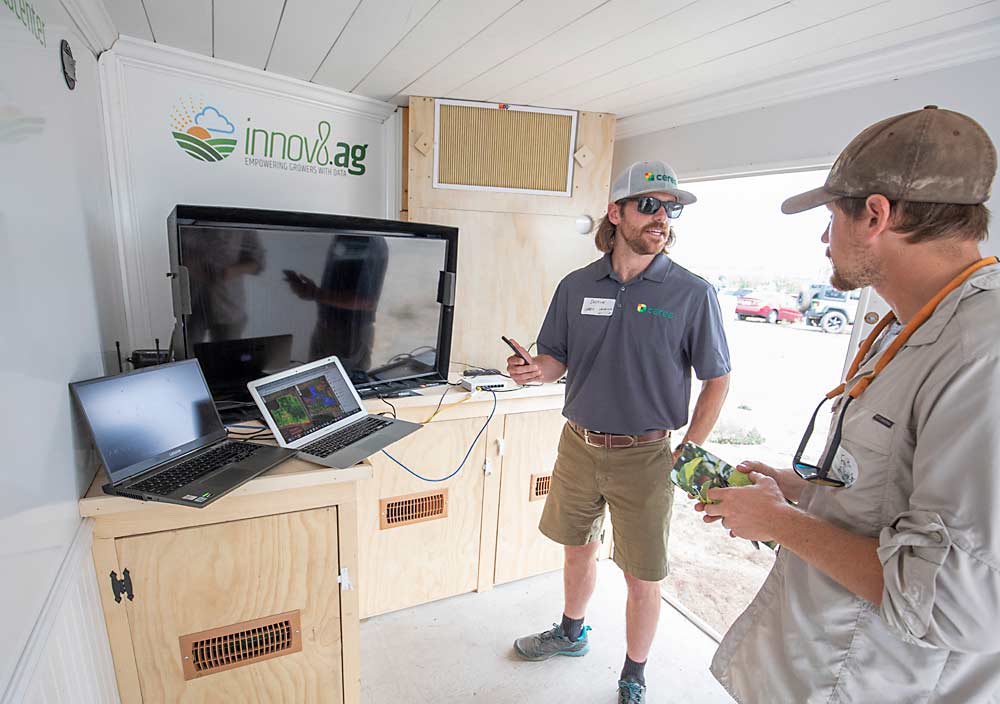
Even the smartest technology will be stopped short of growers’ goals if there’s no way to transmit the data from remote orchards for processing and, ultimately, to users’ phones.
“Can the grower access the data while in the orchard? That’s the crucial part,” said innov8.ag founder and Smart Orchard project leader Steve Mantle.
Connectivity is key, but how much connection — and at what cost — depends on the type of data orchards need to transmit.
Unfortunately, the economics don’t pencil out to build towers in remote locations with few users, Mantle said. But he’s hoping the Smart Orchard provides the critical mass that could draw cellular providers or others interested in the opportunity created by smart farm tech.
When it comes to cell networks, it’s important to evaluate the available cell service during the growing season, he added, because as the trees leaf out, they can block the hint of reception that may seem available in the off-season.
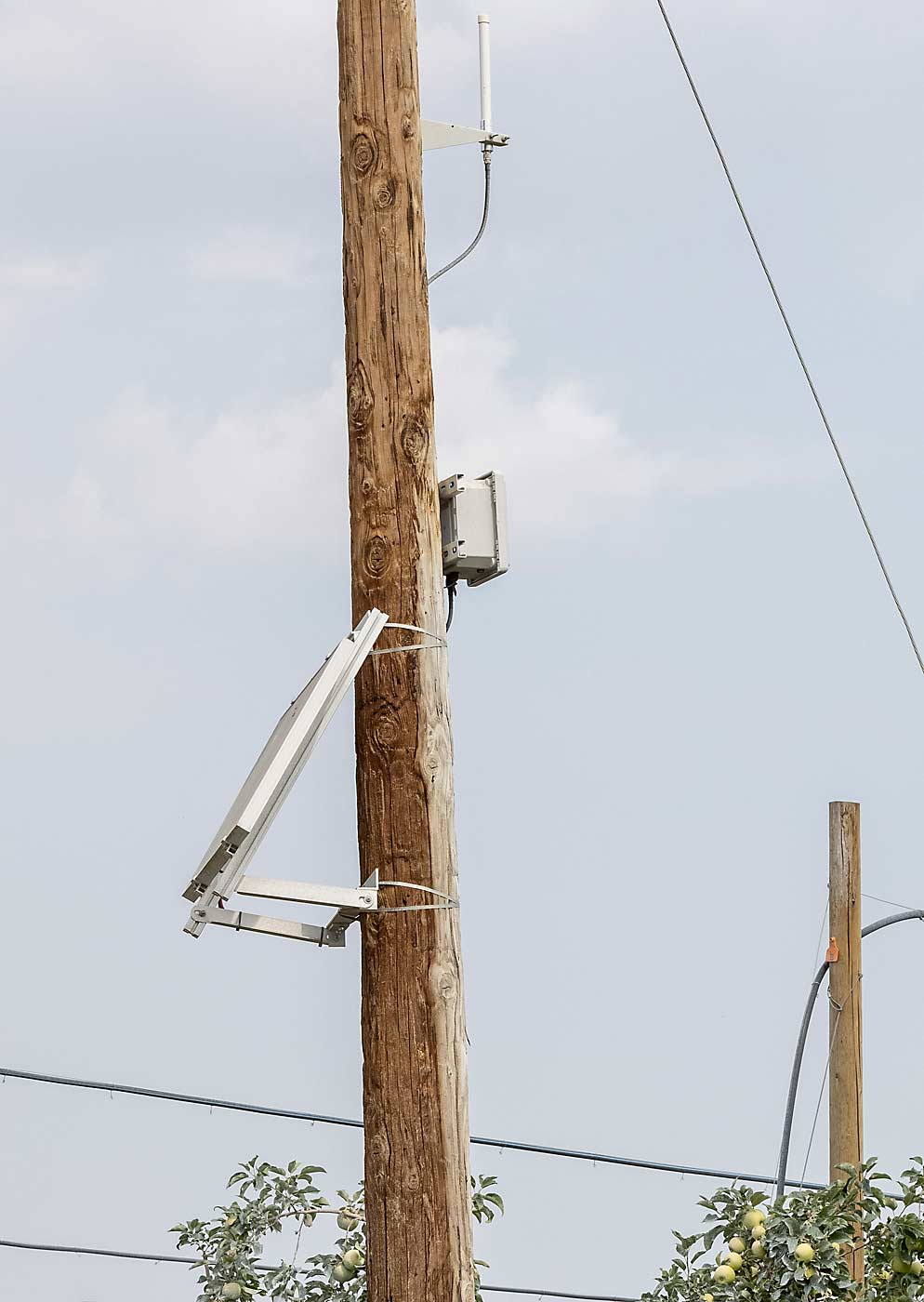
But growers dealing with “ZeroG” — no cellular network coverage, as opposed to the much-touted 4G or 5G with increased speeds cell carriers promote — don’t have to count themselves out of the data-driven tools, said Scott Waller. His company, perhaps aptly named Thingy IoT (IoT is short for Internet of Things — the idea of connecting all kinds of devices for data sharing), designs networks for growers to relay data from sensors reading conditions in real time.
At the Smart Orchard project, Waller installed two systems to deliver all the data from the orchard: a “lightweight” telemetry system for the little blips of data from soil or climate sensors and a wireless network for the “heavyweight” data from camera sensors and other imagery.
He prefers to use low-power, low-data-needs sensors and a networking approach called LoRaWAN (short for long-range, wide-area network) for long range, wireless communication. It’s a cost-effective approach, he said, with small devices that can run for years on just some AA batteries.
But if growers want to transmit imagery data for processing, they need a lot more data power, Waller and Mantle said. If there’s an internet connection at a farm office or shop nearby, a connectivity network can be built off that, but often there’s only enough data speed to run emails and payroll, not to power an autonomous tractor that’s continually analyzing imagery as it operates or crunch the crop load camera data.
The technology of wireless networking capable of handling such “big data” continues to advance, but it still comes at a cost.
Mantle’s approach, instead, is a “mobile ag data center” — a trailer equipped with generators and high-powered computers that he drives to a farm along with his sensor-laden ATV. Then, the data can be processed on site, as soon as it’s collected, with no need to transfer it somewhere else.
—K. Prengaman
Leave A Comment