Minimum wage increases in several key fruit producing U.S. states will drive up labor costs for growers this year and in the years ahead, pushing more growers and packers to find ways to reduce the need for hired labor.
The increases also are likely to persuade growers to look harder at employing tactics to mechanize some work on the farm.
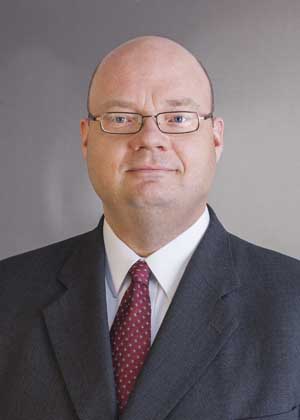
Jon DeVaney
“Automation technologies have always been a long-term research priority and interest, but the fact that the inflation of wages is only going to accelerate means the break-even point for automated technology is going to come along even sooner,” said Jon DeVaney, president of the Washington State Tree Fruit Association in Yakima, Washington.
Washington is among a handful of states that have seen a minimum wage increase in the past year. Michigan’s minimum wage is set at $8.90 an hour for 2017 and is scheduled to increase to $9.25 next year.
New York Gov. Andrew Cuomo has pledged to increase the minimum wage statewide to $15, phasing it in gradually over several years.
For 2017, the wage is $9.70 for most fruit producing regions and $12.50 by 2020 — $10.50 this year for growers in the Long Island area and $15 by 2020.
On the West Coast, the minimum wage rates are even higher for California and Washington. California’s minimum wage for 2017 is $10.50 an hour, increasing to $15 by 2022.
In Washington, the minimum wage is set at $11 in 2017 and will increase annually on a fixed schedule to $13.20 by 2020.
Implementation varies in some states by a company’s employee count. Some states also mandated benefits, such as paid sick and family leave, and changed overtime rules, which add to the increased financial cost to growers.
There’s no doubt the increases will have a significant impact on labor costs for growers and packers, DeVaney said, though how big an impact is still unclear.
Washington growers already face a competitive disadvantage compared with other states thanks to higher transportation costs to access most U.S. population centers, he said. Adding to the layer of labor costs makes it even harder to compete.
“We have to also remember that we think in terms of competing with other tree fruit producers, but consumers view produce as interchangeable: ‘Will I buy apples or the grapes that are on sale?’” he said. “We have to be thinking about all of the fruits and vegetables in the produce section and where they’re sourced and what their production costs are.”
Growers also always remember that half of the world’s apples are produced in China, which has a more relaxed regulatory climate and lower production costs, he said.
Ian LeMay, director of member relations and communications for the California Fresh Fruit Association, echoed those points.
“Thirty-two other states grow peaches, so when my growers are having to pay a base rate of $10.50 per hour, and other states follow the federal minimum wage of $7.25, it already puts my growers at a disadvantage to try to take their produce to market against other states,” he said.
In addition, growers there are already scrambling to find workers, and uncertainties about federal immigration policy don’t help.
“It’s going to be a continuing issue until we get some stabilization on federal immigration policy and, here in California, our growers see how the market and the consumer react to these increased costs and the ways in which we have to start operating our farms here in the next five years,” he said. “It doesn’t seem to concern our representative in Sacramento, but it’s definitely a concern for our growers in the Central Valley.”
On the farm
Andrew Sundquist grows apples, pears and cherries on about 1,800 acres in Washington’s Yakima Valley. A fourth-generation grower, Sundquist needs about 300 workers each year and sees a revolving door of them through a season.
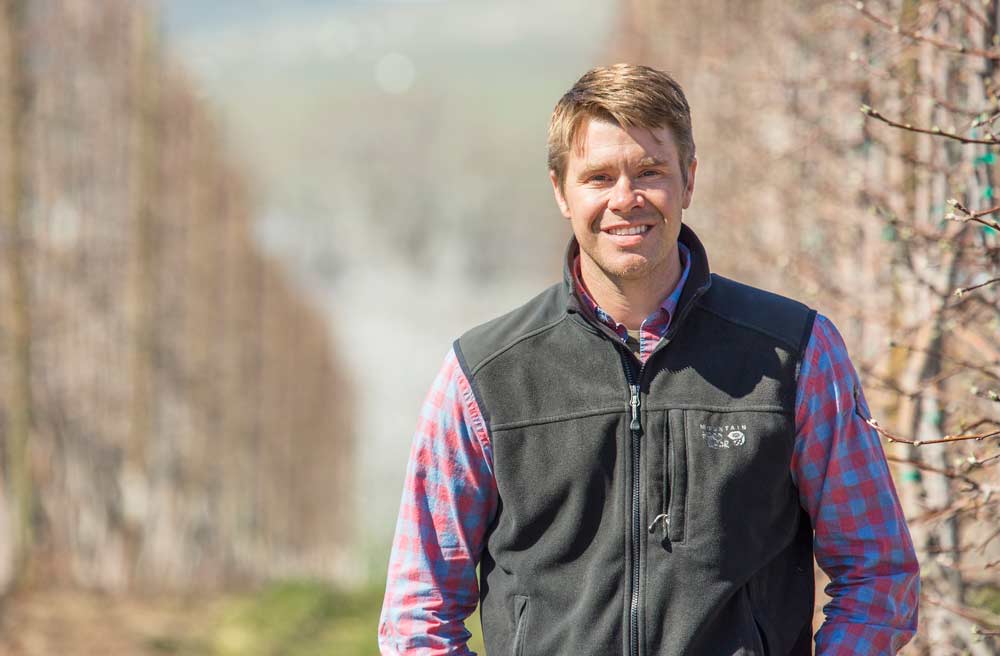
Andrew Sundquist, a grower in Washington’s Yakima Valley, employs about 300 workers each year. (TJ Mullinax/Good Fruit Grower)
“We have local workers, but it seems like the supply of local workers is dwindling considerably,” he said. Nervous that he wouldn’t get through all his pruning this year, he added a small crew of about 15 H-2A workers to help; other H-2A crews are staggered to arrive throughout the season, as in years past, beginning with hand thinning and through harvest.
Because labor is so tight, Sundquist has already been paying higher wages to retain local workers, so the short-term impact to raising the minimum wage would seem to be negligible.
But raising the wages for one worker means raising the wages for everyone, if you want to keep workers, he said, which often means increases across the board.
So what’s the cost of that increase to a grower? Suppose a grower has 300 workers who each work 40 hours per week over a season, for a total of 2,080 hours. Multiply the total number of hours by the cost increase, 70 cents, and the increase to the grower would be $436,800.
In Sundquist’s case, not all of his workers put in that many hours over the course of a season, but the example shows the potential impact.
Also, the increase to the minimum wage results in later increases to the H-2A adverse wage rate for the region. In Washington, that was $12.69 last year, increased to $13.38 in 2017.
New York’s tree fruit growers need about 20,000 workers for six to eight weeks during harvest, and many growers have turned to the H-2A program to supply them. The wage rate there this year is $12.38.
John Teeple of Teeple Farms in Wolcott, New York, grows apples on 350 acres, largely for the fresh market. He typically can get by with local laborers, about 20 to 25 workers, most of the year, then brings in another 40 or so H-2A workers for harvest.
“The adverse wage rate that’s been jumping up 50 cents-plus every year is becoming a real problem. Anybody who works for us in a like job classification has to be paid that minimum wage,” he said. “When we get to $15 minimum wage, what’s our adverse wage rate going to be?”
In his case, Sundquist said he’s hoping to find ways to do things more effectively and spend less on some jobs that need to be done. “We’re really trying to dial in what’s critical and what’s not critical, but we’re having to make choices,” he said.
Long term
Warehouses and growers are doing calculations now, depending on the number of employees and wage rates, to determine their increased costs. For large growers and packers, the increases could be in the millions of dollars.
DeVaney said he’s heard more discussion about automation technologies. “If you now have a predictable wage increase, you can factor out your increasing costs of labor versus a new packing line, new orchard platforms,” he said.
Some technologies, such as automated harvesters, are going to require more research and demonstration in the field before implementation, LeMay said. In short, they’re no quick fix. “Down the road, there may be ways to mitigate some of the labor needs, but they’re not going to be here in the next 30, 45 days,” he said.
The New York Farm Bureau continues to work in its state Legislature to mitigate the impact to growers.
Last year, the group successfully lobbied for workforce tax credits for farm employers: $250 per employee per farm for workers who put in a minimum of 500 hours per year.
Some $30 million was allocated for the fund, and the group is lobbying to double that fund to $60 million, according to Steve Ammerman, manager of public affairs for New York Farm Bureau.
Agriculture already faces too many economic problems: Declining commodity prices in some cases, increased water prices in others. Drought and freezes are hampering production, and rising labor costs just add another layer, he said.
One grower is turning to H-2A for the first time but said that if the program doesn’t work for him, he’ll probably cut down more apple trees, “because he just won’t have the labor to manage the crop properly.” •
– by Shannon Dininny
Leave A Comment