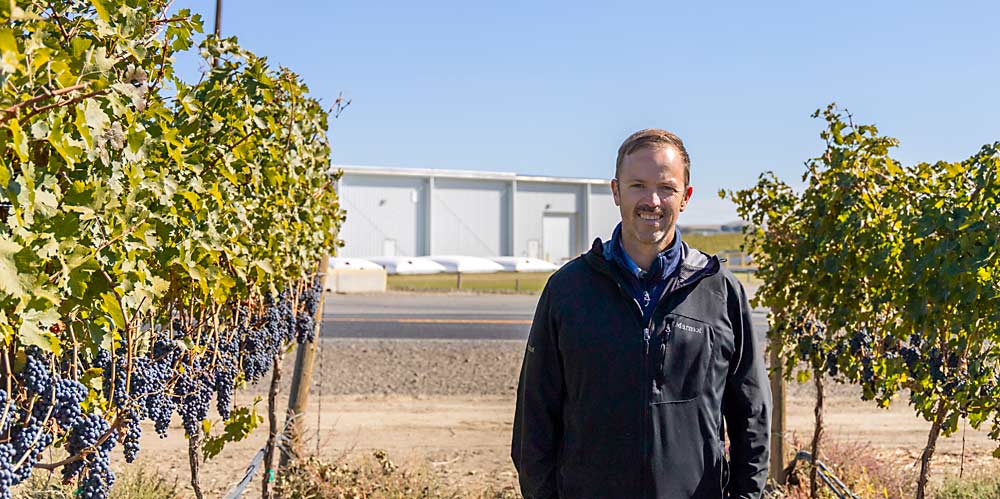
Growing Cabernet Sauvignon in the Yakima Valley is a gamble: As winemakers wait for the fruit to reach its flavor peak in the fall, season-ending frosts loom.
“I was raised that I couldn’t grow Cab in the Yakima Valley, that it’s too cold here to ripen,” said Marcus Miller, president of Airport Ranch Wine Estates and third-generation winegrower with over 800 acres of wine grapes in Sunnyside, Washington. “Today, I sell more Cab than the next two grapes combined.”
But to make Cabernet the core of his business, Miller said it’s been necessary to invest in the winery’s capacity, as well as equipment, to enable him to harvest all those late grapes in a hurry, clean and sort them, and have a place to put them.
At least one of those investments is readily visible: 6,000-gallon bulk wine bladders sit on the lawn outside the winery, providing extra tank space for a sudden onslaught of fresh fruit.
“Part of the reason I can let that Cab hang out is that we can open up a lot of space if we need to,” Miller said.
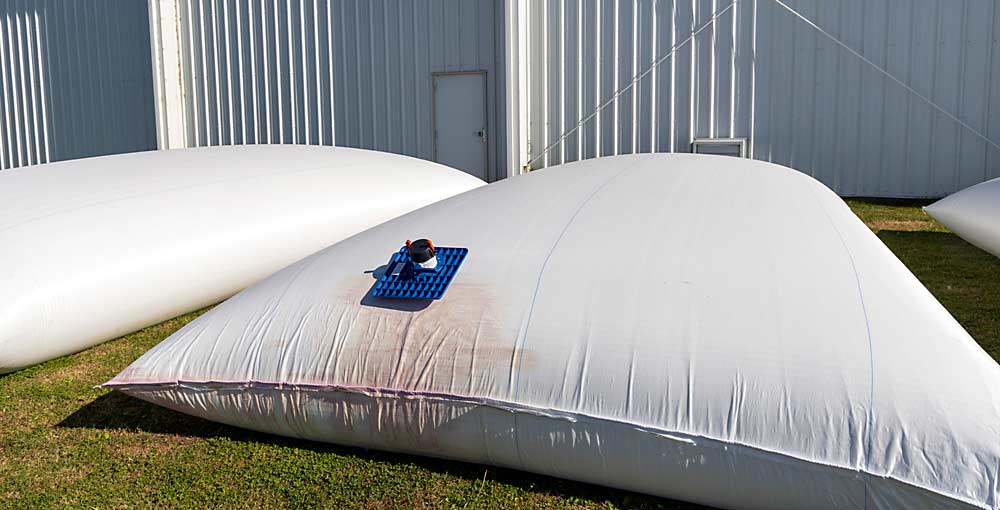
An increasing number of Cabernet plantings, and other late-harvest red grapes, in Washington vineyards can increase risks as well as returns, Leah Adint said during a session about risk management during the Washington Winegrowers Association’s annual meeting, known as WineVit, earlier this year. Adint is the winemaker for Chateau Ste. Michelle’s Canoe Ridge Estate, a reds-only winery.
During the session, Miller shared how his business is preparing for climate uncertainty. Airport Ranch’s Airfield Estates Winery has enjoyed many great vintages since his father founded the family’s winery in 2005, but the past several seasons have been marked by climate challenges including smoke, freeze, more smoke and then record-setting heat.
“We’ve had all these fastball vintages and we’ve succeeded in hitting a lot of home runs in producing great wines,” Miller said during his talk. “But in the future, we are seeing more uncertainty, more smoke. For us to succeed, we have to be able to hit Mother Nature’s off-speed pitches, too.”
Facing frost
When Good Fruit Grower visited in early October to learn more about Airport Ranch’s approach to climate adaptation, Miller was facing a weather forecast similar to 2019. He wanted to give the Cabernet another week, if possible, but a frost prediction looming in the next week could have forced a sudden change of plans.
In 2019, a succession of frost events hit in early October when a cool season had many grapes still hanging across Washington. After a freeze, grapes need to be picked quickly, but the crunchy, frozen leaves that are also raked in by mechanical harvesters can create unwanted floral aromas known as “rose taint” or “freeze taint.”
Airport Ranch suffered a lot of rose taint in 2011, and Miller wasn’t eager to repeat the experience in 2019.
“The frosted petioles are jammed with terpenes, and I don’t want any of that in my nice, dark Cabernet Sauvignon,” Miller said. “So, for me, the solution was to invest in clean processing equipment in a hurry.”
He connected with Grant De Vries of Vine Tech Equipment, after the first freeze event, and bought a 20-ton-per-hour Pellenc destemmer and berry sorter, along with an optical sorter, which De Vries delivered with “perfect” timing just before the second freeze hit less than two weeks later. It’s a second destemming pass, since Miller uses a Pellenc harvester with a destemmer as well.
A typical drum destemmer only removes the large stems, De Vries said, while the Pellenc Selectiv’ system uses rollers that remove petioles, small stems, seeds, jacks and bits of leaves. “Post-frost, it’s just a mound of petioles,” he said. Juice that is separated is screened and reclaimed, while the berries travel along a vibrating table to an optical sorter that uses blasts of air to kick anything other than ripe grapes off the line.
De Vries said he sells more of the destemming and berry sorting machine, especially to smaller wineries that hand harvest, and only a few optical sorters — the Pellenc model is too small for large wineries but also an outsized investment for most small wineries.
Miller bought both, thinking that the $300,000 investment in equipment he could use for years to come was a better solution than spending over $100,000 to hand harvest grapes to avoid the frozen leaves.
“It saved our vintage,” he said of 2019. “It wasn’t perfect, but it was pretty dang successful, so it gives me a diminished sense of dread.”
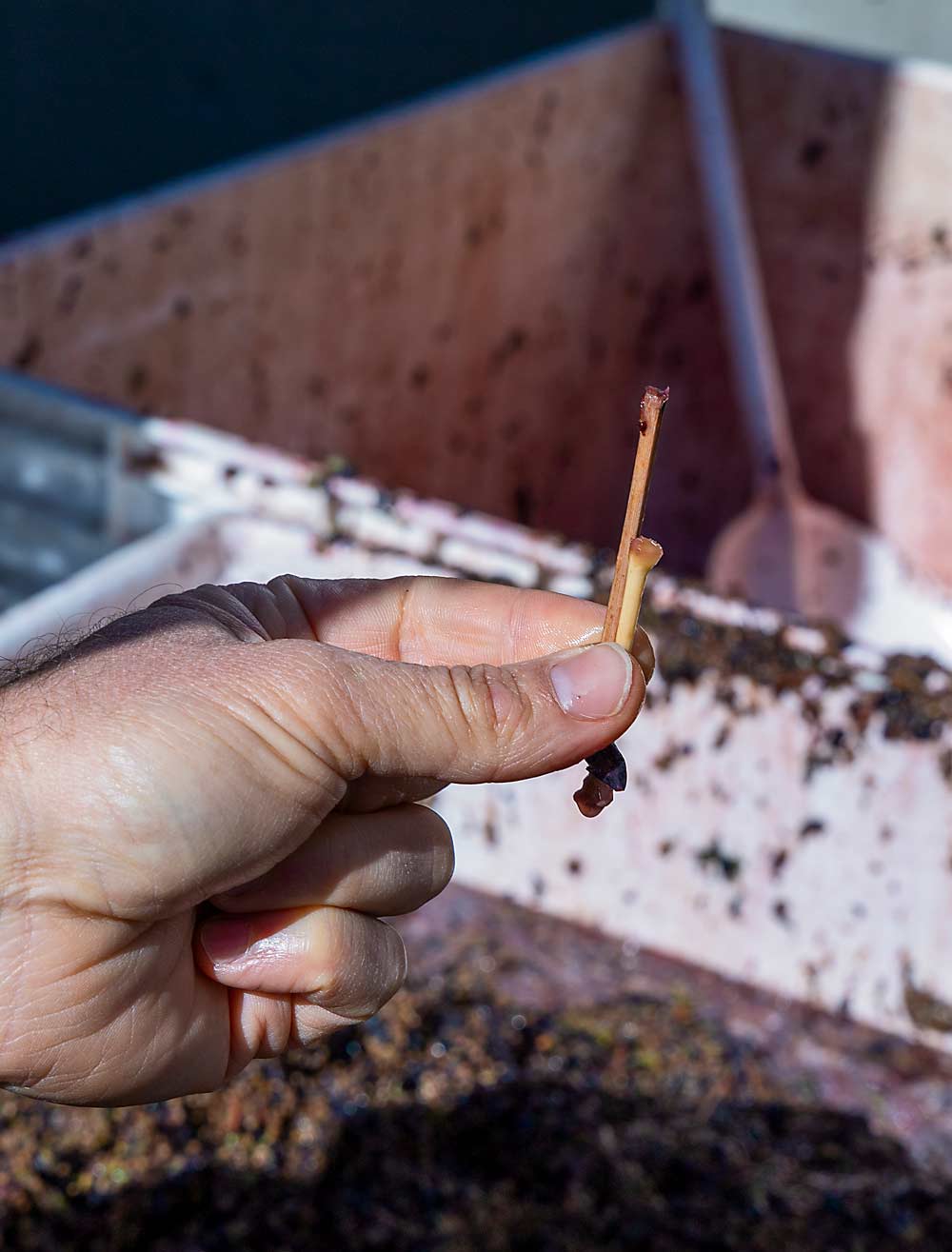
By mid-October, a freeze did hit just after the harvest of the late reds ramped up, but not as severe as 2019. Most of Airport Ranch’s remaining acreage was machine harvested in the first few days after the frost, but when Good Fruit Grower called to follow up, Miller was helping his crew hand harvest an estimated 100 tons of his premium Cabernet to minimize any risk from the frozen leaves.
Capacity to change
In a crisis — a sudden smoke event or freeze forecast — Airport Ranch can bring in about 100 tons of grapes in one day, with the clean processing equipment running at a maximum of 14 tons per hour.
This year, he had more grapes to bring in than expected, after realizing that his crop estimates for all the red grapes were low. Miller thinks the 2021 heat wave threw off his estimates in two ways: by temporarily stalling fruit growth when he made his estimates and due to increased vigor from when “we watered like crazy because we were scared of the heat.”
For example, one 12-acre block he estimated at 35 tons was picking 47.
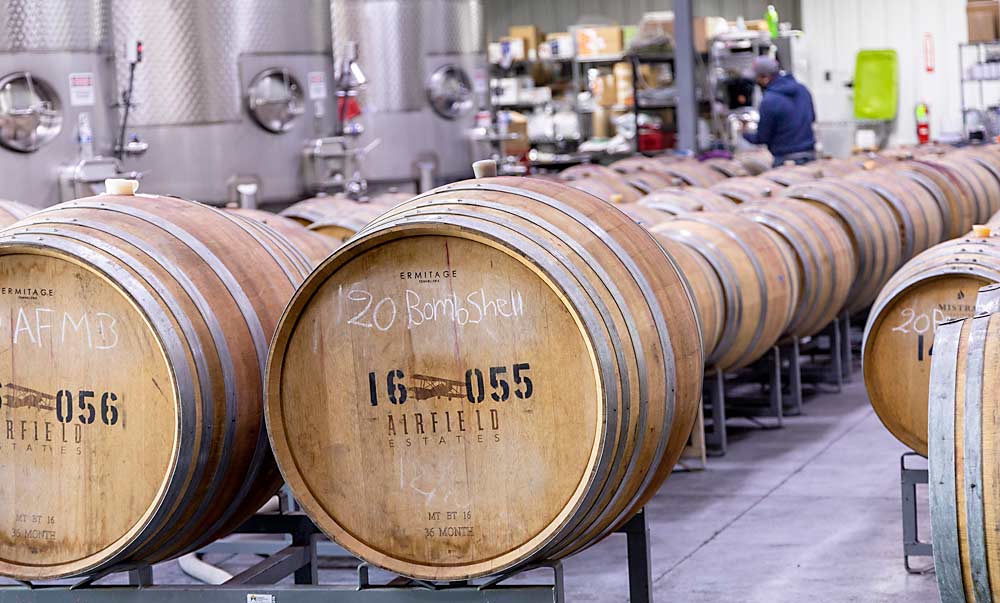
To hold all those grapes, Miller can turn to 80-ton “emergency” fermenters that can hold fruit outside if tank capacity inside the winery is limited. Meanwhile, his winemaker, Travis Maple, was shifting bulk wines into bladders that sit outside for a couple of months to free up tank space for the late-harvesting grapes. They keep more than a dozen of the $400 SIA Flexitanks on hand, just in case.
The focus on capacity extends to barrel storage, too. Airport Ranch built its Sunnyside facility in 2014, on the old military airfield that Miller’s grandfather converted into their farm’s headquarters in the 1940s. Each year, they add on more.
In 2018, they constructed 12,000 square feet of barrel space, and next year they plan to build another 12,000 square feet. That holds barrels of 2020 wines, as well as new concrete tanks and microfermentations going in bins.
Between the capacity at the winery and the clean processing equipment, it all helped Miller remain confident in his decision to let so much fruit stay on the vines. After a few more days of “hang time magic,” a lot of fruit was finally ready to pick and the harvest race against the frost began in earnest.
“Worst case scenario, it’s 2019 again — and we’ve been there, we’ve done that, and we came out the other end OK,” he said.
—by Kate Prengaman
Leave A Comment